Induction heating is a non-contact heating process that uses electromagnetic induction and the Joule effect to generate heat within conductive materials. The two primary methods of induction heating are coreless induction heating and channel (core-type) induction heating. Coreless induction heating is widely used for melting metals and creating alloys, as it relies on a magnetic field to induce eddy currents directly in the material. Channel induction heating, on the other hand, uses a transformer-like design with a molten metal loop to generate heat, making it suitable for holding and maintaining molten metal temperatures. Both methods leverage electromagnetic induction and Joule heating but differ in design and application.
Key Points Explained:
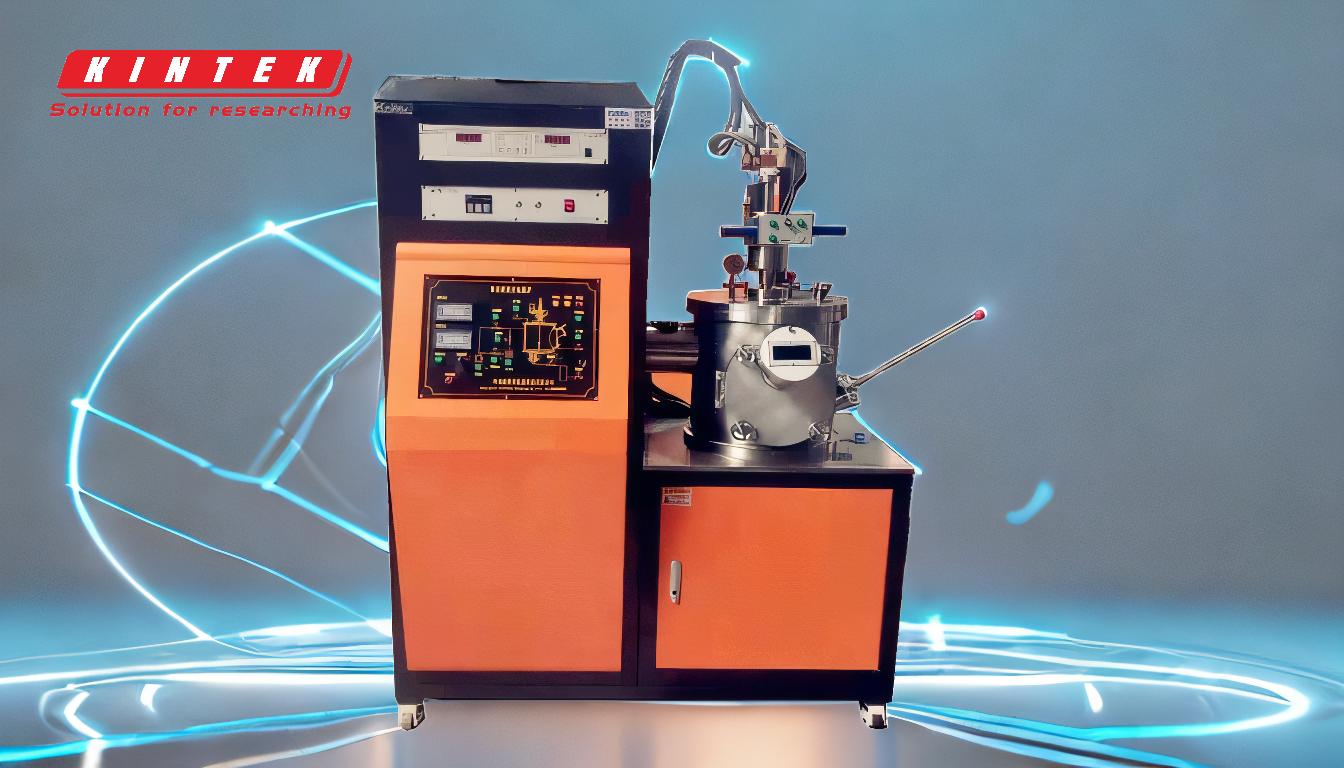
-
Coreless Induction Heating:
- Principle: Coreless induction heating relies on a coil that generates a high-frequency alternating magnetic field. This field induces eddy currents within the conductive material, which in turn produce heat due to the Joule effect.
- Design: The furnace consists of a refractory-lined crucible surrounded by a water-cooled copper coil. There is no iron core, hence the name "coreless."
- Applications: This method is ideal for melting metals, creating alloys, and heat treatment processes. It is widely used in industries like steelmaking, foundries, and metalworking due to its flexibility and efficiency.
-
Advantages:
- No direct contact between the heating source and the material, reducing contamination.
- High heating efficiency and precise temperature control.
- Suitable for a wide range of materials and batch sizes.
-
Disadvantages:
- Higher energy consumption compared to channel furnaces for certain applications.
- Requires a higher initial investment due to complex coil and power supply systems.
-
Channel (Core-Type) Induction Heating:
- Principle: Channel induction heating operates similarly to a transformer. A primary coil induces current in a secondary loop of molten metal, which generates heat through the Joule effect.
- Design: The furnace includes a refractory-lined channel that forms a loop of molten metal. The primary coil surrounds the channel, and the molten metal acts as a single-turn secondary winding.
- Applications: This method is primarily used for holding and maintaining molten metal temperatures in applications like die casting, metal holding, and continuous casting.
-
Advantages:
- Highly energy-efficient for maintaining molten metal temperatures over long periods.
- Lower operating costs compared to coreless furnaces for specific applications.
- Compact design and lower electromagnetic interference.
-
Disadvantages:
- Limited to applications where a continuous molten metal loop can be maintained.
- Less flexible for melting different types of metals or alloys compared to coreless furnaces.
-
Comparison of Coreless and Channel Induction Heating:
- Efficiency: Coreless furnaces are more efficient for melting and rapid heating, while channel furnaces excel in energy efficiency for holding molten metal.
- Flexibility: Coreless furnaces are more versatile and can handle a wider range of materials and processes. Channel furnaces are specialized for specific applications like metal holding.
- Cost: Coreless furnaces have higher initial costs but offer greater flexibility. Channel furnaces have lower operating costs but are limited in application scope.
-
Key Physical Phenomena in Induction Heating:
- Electromagnetic Induction: A varying magnetic field induces eddy currents in the conductive material, which generate heat.
- Joule Heating: The resistance of the material to the induced currents converts electrical energy into thermal energy, raising the material's temperature.
-
Advantages of Induction Heating Over Traditional Methods:
- Non-Contact Heating: No direct flame or physical contact, reducing contamination and wear.
- Precision: Allows for precise control over heating rates and temperatures.
- Energy Efficiency: Minimizes heat loss and maximizes energy transfer to the material.
- Safety: Eliminates open flames, reducing fire hazards and improving workplace safety.
By understanding the differences and applications of coreless and channel induction heating, purchasers can make informed decisions based on their specific needs, whether for melting, alloying, or maintaining molten metal temperatures.
Summary Table:
Aspect | Coreless Induction Heating | Channel Induction Heating |
---|---|---|
Principle | Magnetic field induces eddy currents in the material. | Transformer-like design with a molten metal loop. |
Applications | Melting metals, creating alloys, heat treatment. | Holding and maintaining molten metal temperatures. |
Advantages | No contamination, precise control, versatile. | Energy-efficient, lower operating costs, compact. |
Disadvantages | Higher energy use, higher initial cost. | Limited flexibility, requires molten metal loop. |
Best For | Melting, alloying, and rapid heating. | Maintaining molten metal over long periods. |
Need help choosing the right induction heating method? Contact our experts today for tailored solutions!