Annealing is a heat treatment process used to alter the physical and sometimes chemical properties of a material, typically metals, to increase its ductility and reduce its hardness, making it more workable. The process involves heating the material to a specific temperature, holding it at that temperature for a certain period, and then cooling it slowly. The two primary types of annealing are full annealing and process annealing. Full annealing involves heating the material above its upper critical temperature and then cooling it slowly to refine its grain structure and relieve internal stresses. Process annealing, on the other hand, is performed at lower temperatures and is typically used to soften the material for further cold working without significantly altering its microstructure.
Key Points Explained:
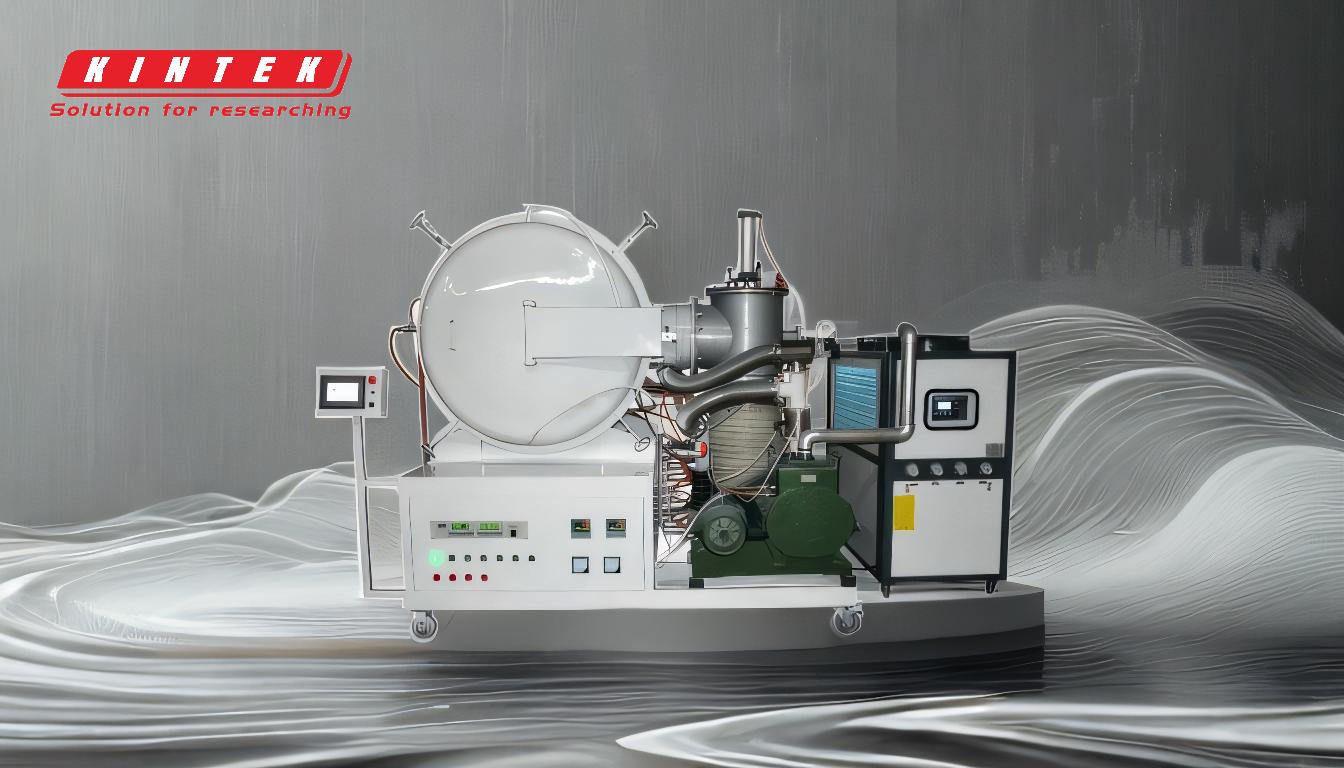
-
Full Annealing:
- Definition: Full annealing involves heating the metal above its upper critical temperature (Ac3 for steels) and then cooling it slowly, usually in a furnace. This process allows the material to fully austenitize, meaning it transforms into a uniform austenitic structure.
- Purpose: The main goal of full annealing is to produce a refined grain structure, improve ductility, and relieve internal stresses caused by previous manufacturing processes like casting or machining.
- Temperature Range: For steels, full annealing typically occurs at temperatures between 816°C – 927°C (1500°F – 1700°F).
- Cooling Rate: The material is cooled slowly, often in the furnace, to ensure that the new grain structure is stable and free from internal stresses.
-
Process Annealing:
- Definition: Process annealing is performed at temperatures below the lower critical temperature (Ac1 for steels). It is often used to soften metals that have been work-hardened during cold working processes like rolling or drawing.
- Purpose: The primary purpose of process annealing is to restore ductility to a material that has become too hard or brittle due to cold working, allowing it to be further processed without cracking or breaking.
- Temperature Range: Process annealing typically occurs at temperatures between 538°C – 649°C (1000°F – 1200°F) for steels.
- Cooling Rate: The cooling rate is less critical in process annealing compared to full annealing, and the material can often be air-cooled.
-
Other Types of Annealing:
- While full annealing and process annealing are the two primary types, there are several other specialized annealing processes, such as:
- Subcritical Annealing: Performed just below the Ac1 temperature, this process is used to soften the material without significantly altering its microstructure.
- Isothermal Annealing: Involves cooling the material to a specific temperature and holding it there to allow the microstructure to stabilize before further cooling.
- Spheroidizing Annealing: Used to produce a spheroidal or globular form of carbide in the microstructure, which improves machinability and reduces brittleness.
- While full annealing and process annealing are the two primary types, there are several other specialized annealing processes, such as:
-
Stages of Annealing:
- Recovery: The first stage where the material is heated to a temperature that allows dislocations in the crystal structure to move, relieving internal stresses.
- Recrystallization: At higher temperatures, new strain-free grains begin to form, replacing the deformed grains from the cold-working process.
- Grain Growth: If the material is held at high temperatures for too long, the newly formed grains can grow larger, which may not be desirable for certain applications.
-
Applications of Annealing:
- Full Annealing: Commonly used in the manufacturing of steel components that require high ductility and low hardness, such as gears, shafts, and structural components.
- Process Annealing: Often applied in industries where metals undergo extensive cold working, such as in the production of wires, sheets, and tubes.
In summary, the two main types of annealing—full annealing and process annealing—serve different purposes and are applied based on the desired outcome for the material. Full annealing is used to refine the grain structure and relieve internal stresses, while process annealing is used to restore ductility in work-hardened materials. Understanding these processes is crucial for selecting the appropriate heat treatment method for specific applications.
Summary Table:
Type of Annealing | Purpose | Temperature Range | Cooling Rate |
---|---|---|---|
Full Annealing | Refine grain structure, improve ductility, relieve internal stresses | 816°C – 927°C (1500°F – 1700°F) | Slow cooling (often in furnace) |
Process Annealing | Restore ductility in work-hardened materials | 538°C – 649°C (1000°F – 1200°F) | Air-cooled or less critical cooling |
Need help choosing the right annealing process for your application? Contact our experts today!