A controlled atmosphere furnace is a specialized heating system that uses specific gases to create an environment tailored to the needs of the material being processed. The atmosphere within the furnace can be adjusted to prevent oxidation, facilitate chemical reactions, or protect the material from contamination. Common gases used include hydrogen, nitrogen, argon, and helium, each serving unique purposes depending on the application. These furnaces are widely used in industries such as metallurgy, ceramics, and additive manufacturing, offering advantages like precise control, improved efficiency, and reduced labor requirements. Understanding the types of furnace atmospheres and their applications is crucial for selecting the right setup for specific processes.
Key Points Explained:
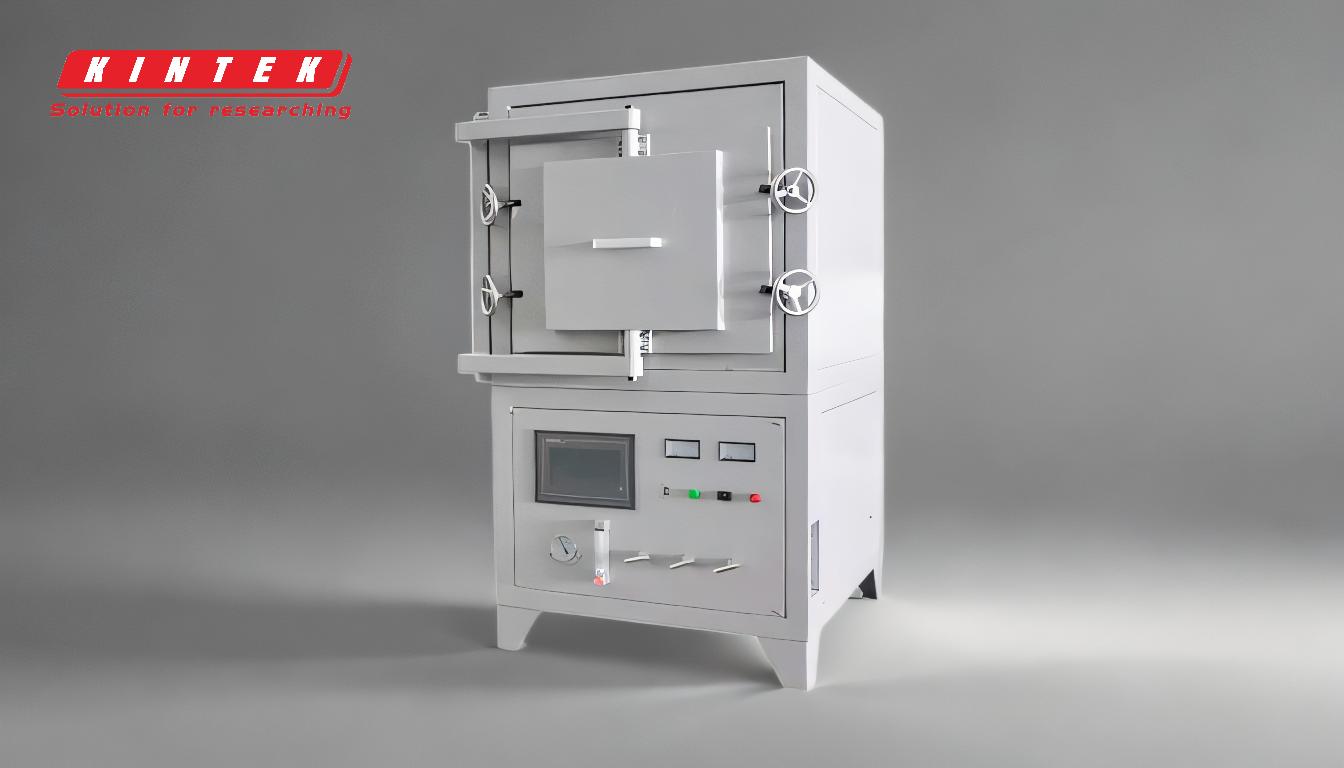
-
Types of Furnace Atmospheres:
- Hydrogen: Often used for reducing atmospheres, hydrogen helps remove oxides from metal surfaces, making it ideal for processes like annealing and sintering.
- Nitrogen: An inert gas that prevents oxidation and is commonly used in processes where a non-reactive environment is required.
- Argon: Another inert gas, argon is used in applications requiring high purity and protection from contamination.
- Helium: Known for its high thermal conductivity, helium is used in specialized applications where rapid heat transfer is necessary.
- Oxygen: While not inert, oxygen is used in specific processes where controlled oxidation is required, such as in the production of certain ceramics.
-
Applications of Controlled Atmosphere Furnaces:
- Pyrolysis: This process involves decomposing materials at high temperatures in an inert atmosphere, preventing unwanted chemical reactions.
- Additive Manufacturing: In 3D printing, controlled atmospheres are used to create intricate metal structures without oxidation or contamination.
- Heat Treatment: Controlled atmospheres are crucial for processes like hardening, where the atmosphere acts as a carrier for key elements that react with the material's surface.
-
Benefits of Controlled Atmosphere Furnaces:
- Precision Control: These furnaces offer better control over the processing environment, ensuring consistent results.
- Efficiency: They are more efficient than traditional furnaces like box or salt bath furnaces, reducing energy consumption and processing time.
- Labor Savings: Automated systems reduce the need for manual intervention, lowering labor costs.
-
Common Gases and Their Roles:
- Argon and Nitrogen: These inert gases displace room air, creating a protective environment that prevents oxidation and contamination.
- Hydrogen: Used for its reducing properties, hydrogen helps in processes where oxide removal is necessary.
- Oxygen: In controlled amounts, oxygen can facilitate specific chemical reactions, such as in ceramic production.
-
Industrial and Academic Use:
- Controlled atmosphere furnaces are widely used in laboratories and industrial settings for various applications, including chemical analysis, sintering, and heat treatment. They are particularly valuable in educational institutions for research and development purposes.
-
Protective Atmosphere Furnace:
- This type of furnace is designed to protect materials from exposure to harmful elements in the air, such as oxygen and water vapor. By introducing specific gases, it ensures that the material remains uncontaminated during processing.
For more detailed information on controlled atmosphere furnaces, you can refer to this resource: controlled atmosphere furnace.
Summary Table:
Gas Type | Role | Applications |
---|---|---|
Hydrogen | Reduces oxides, ideal for annealing and sintering | Metallurgy, heat treatment |
Nitrogen | Prevents oxidation, non-reactive environment | Ceramics, additive manufacturing |
Argon | High purity, protects from contamination | Research labs, semiconductor production |
Helium | High thermal conductivity, rapid heat transfer | Specialized industrial processes |
Oxygen | Controlled oxidation | Ceramic production, specific chemical reactions |
Need help choosing the right furnace atmosphere for your application? Contact our experts today for personalized advice!