Sintering is a critical process in materials science, used to create solid structures from powdered materials by applying heat without melting the material entirely. The types of sintering are broadly categorized based on the mechanisms and conditions involved, such as the presence of a liquid phase, the application of external pressure, or the use of advanced techniques like microwave or spark plasma sintering. Common types include solid-state sintering, liquid phase sintering, and reactive sintering, each serving specific industrial applications to enhance material properties and reduce porosity.
Key Points Explained:
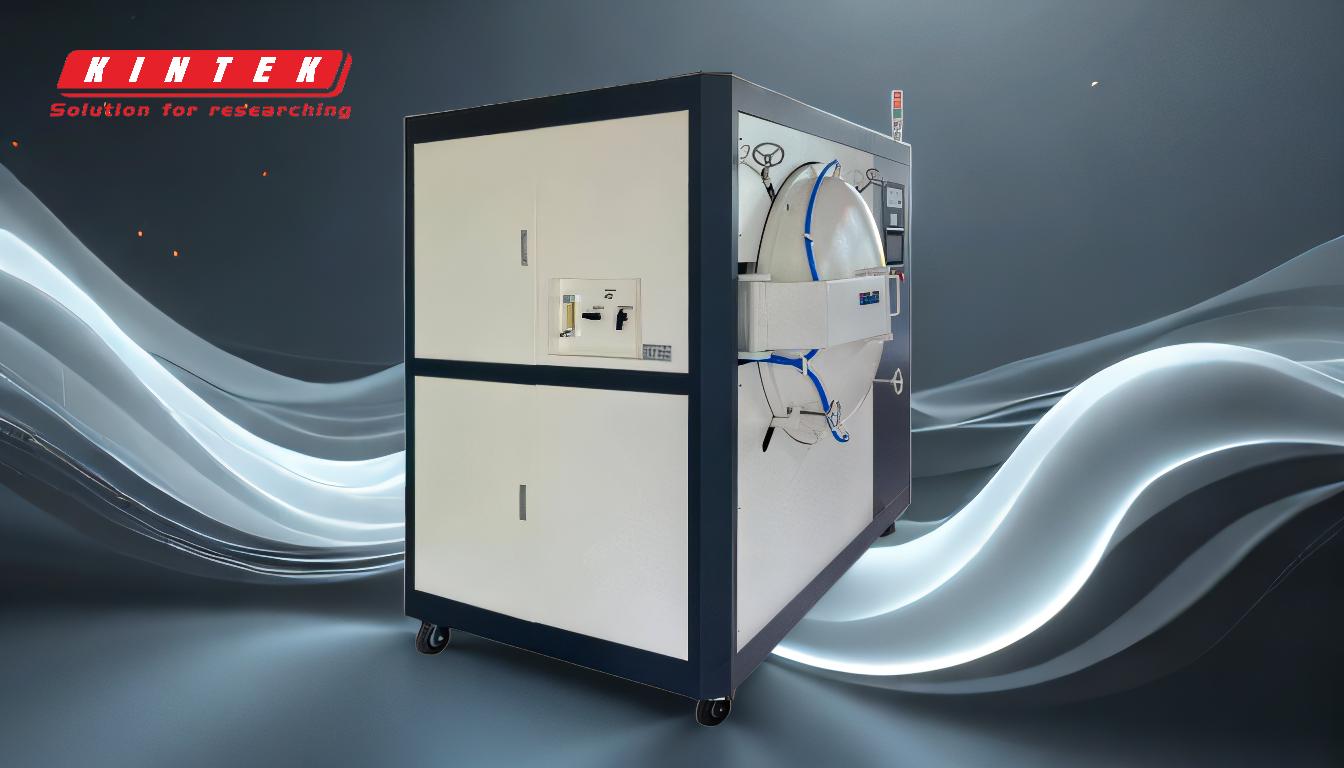
-
Solid-State Sintering:
- Definition: This process involves heating powdered materials just below their melting point, allowing particles to bond through atomic diffusion without the formation of a liquid phase.
- Applications: Widely used in ceramics and metals to produce components with high strength and low porosity.
- Advantages: Maintains the chemical composition of the material and minimizes shrinkage.
-
Liquid Phase Sintering:
- Definition: In this method, a liquid phase is introduced during sintering, which accelerates densification and bonding between particles.
- Applications: Commonly used in the production of cemented carbides and certain ceramics.
- Advantages: Enhances densification rates and improves mechanical properties.
-
Reactive Sintering:
- Definition: This involves a chemical reaction between powder particles during the heating process, leading to the formation of new compounds.
- Applications: Used in the synthesis of advanced materials like intermetallics and composites.
- Advantages: Allows for the creation of materials with unique properties not achievable through conventional methods.
-
Pressurized Sintering:
- Definition: This technique applies external pressure along with high temperature to the powder compact, enhancing densification.
- Types: Includes methods like hot isostatic pressing (HIP) and spark plasma sintering (SPS).
- Applications: Ideal for producing high-density components with minimal defects.
- Advantages: Reduces porosity and improves mechanical strength.
-
Advanced Sintering Techniques:
- Microwave Sintering: Uses microwave energy to heat the material, resulting in faster and more uniform heating.
- Spark Plasma Sintering: Combines electric current and physical compression to achieve rapid densification.
- Direct Metal Laser Sintering (DMLS): A 3D printing technique that uses a laser to sinter metal powder layer by layer.
- Applications: These methods are used in advanced manufacturing and prototyping.
- Advantages: Enables precise control over the sintering process and the production of complex geometries.
-
Special Sintering Processes:
- Loose Sintering: Involves sintering without forming a compact, often used for porous materials.
- Fusion Dipping: A process where the material is dipped into a molten phase to achieve sintering.
- Hot Pressing: Combines heat and pressure to achieve densification in a single step.
- Applications: These methods are used for specific applications requiring unique material properties.
By understanding these various types of sintering and their applications, manufacturers can select the most appropriate method for their specific needs, ensuring optimal material properties and performance. For more detailed information on the equipment used in these processes, you can explore sintering furnace.
Summary Table:
Type of Sintering | Key Features | Applications | Advantages |
---|---|---|---|
Solid-State Sintering | Heating below melting point, atomic diffusion, no liquid phase | Ceramics, metals | Maintains chemical composition, minimizes shrinkage |
Liquid Phase Sintering | Introduces liquid phase to accelerate densification | Cemented carbides, ceramics | Enhances densification, improves mechanical properties |
Reactive Sintering | Chemical reaction between particles, forms new compounds | Intermetallics, composites | Creates materials with unique properties |
Pressurized Sintering | Applies external pressure with heat (e.g., HIP, SPS) | High-density components | Reduces porosity, improves mechanical strength |
Advanced Techniques | Microwave sintering, spark plasma sintering, DMLS | Advanced manufacturing, prototyping | Precise control, complex geometries |
Special Processes | Loose sintering, fusion dipping, hot pressing | Porous materials, unique properties | Tailored for specific applications |
Need help selecting the right sintering method for your materials? Contact our experts today!