Sintering furnaces are essential in various industries for the consolidation of powdered materials into dense, solid components. They come in different types, each designed for specific applications, materials, and temperature requirements. Common types include pusher furnaces, walking-beam furnaces, vacuum sintering furnaces, resistance sintering furnaces, and induction sintering furnaces. These furnaces can be further classified based on heating methods (e.g., ceramic elements or microwaves), temperature ranges, and vacuum levels. Additionally, sintering techniques such as solid-state sintering, liquid-phase sintering, and microwave sintering are employed to achieve desired material properties. Understanding these types and their applications is crucial for selecting the right equipment for specific manufacturing needs.
Key Points Explained:
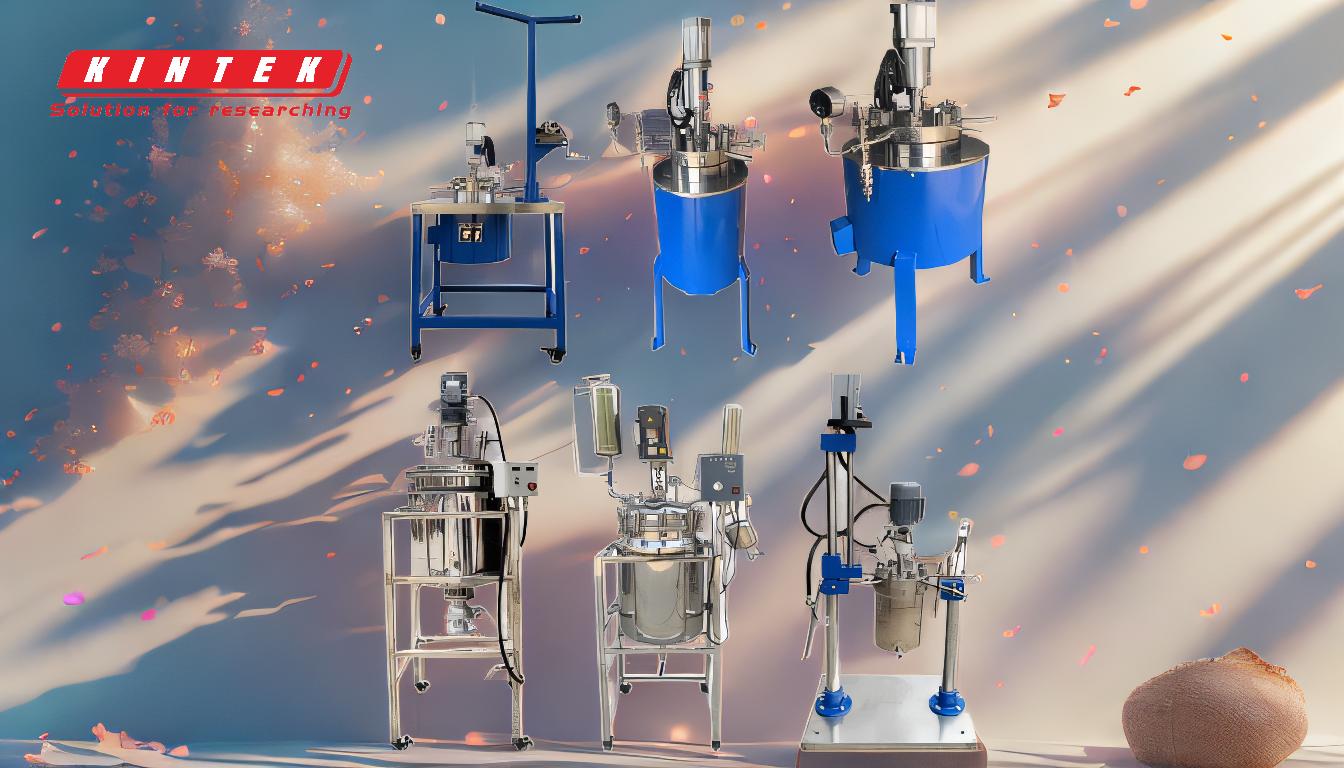
-
Pusher Furnaces and Walking-Beam Furnaces:
- Pusher Furnaces: These furnaces move workpieces through the furnace on a series of boats or plates in a continuous train. They are ideal for high-volume production and are commonly used in industries requiring consistent and uniform heating.
- Walking-Beam Furnaces: These use a pusher mechanism to move boats through the furnace on beams that lift, push forward, and lower to "walk" the boat through the furnace. This design reduces friction and wear, making it suitable for delicate or high-precision components.
-
Vacuum Sintering Furnaces:
-
Classification by Temperature:
- Ordinary Sintering Furnaces: Operate at temperatures up to 1300℃.
- Medium Temperature Sintering Furnaces: Operate between 1300℃ and 1600℃.
- High Temperature Sintering Furnaces: Operate between 1600℃ and 2400℃.
-
Classification by Vacuum Level:
- Low Vacuum: Suitable for materials requiring minimal oxidation control.
- High Vacuum: Used for materials needing stringent oxidation and contamination control.
- Ultra-High Vacuum: Ideal for advanced materials requiring the highest purity and minimal contamination.
-
Application-Based Types:
- Ceramic Vacuum Sintering Furnaces: Designed for ceramic materials.
- Metal Vacuum Sintering Furnaces: Tailored for metal materials.
- Composite Materials Vacuum Sintering Furnaces: Used for composite materials.
-
Classification by Temperature:
-
Heating Methods:
- Ceramic Elements: Commonly made from materials like molybdenum disilicide (MoSi2) or silicon carbide (SiC), these elements provide consistent and reliable heating.
- Microwave Sintering: A newer method that uses microwaves to achieve rapid and uniform heating, often resulting in faster sintering times and improved material properties.
-
Resistance and Induction Sintering Furnaces:
- Resistance Sintering Furnaces: Convert electrical energy into heat energy through electric heating elements. They are versatile and widely used in various industries.
- Induction Sintering Furnaces: Use electromagnetic induction to excite electric currents in metal, generating heat. This method is efficient and suitable for conductive materials.
-
Sintering Techniques:
- Solid-State Sintering: Involves heating powdered material just below its melting point to bond particles through atomic diffusion. This method is common for ceramics and metals.
- Liquid Phase Sintering: Uses a solvent liquid to induce low porosity and bonding, which is then driven off by heating. This technique is often used for materials requiring high density and strength.
- Reactive Sintering: Involves a chemical reaction of powder particles during heating, leading to the formation of new compounds or phases.
- Microwave Sintering: Utilizes microwaves for rapid heating and integration, often resulting in improved material properties and reduced processing times.
- Spark Plasma Sintering: Employs electric current and physical compression to achieve rapid sintering, often used for advanced materials.
- Hot Isostatic Pressing: Applies high pressure and temperature to form and fuse powder particles, resulting in high-density components with excellent mechanical properties.
Understanding the different types of sintering furnaces and their applications is crucial for selecting the right equipment based on material properties, production volume, and desired outcomes. Each type offers unique advantages, making them suitable for specific industrial needs.
Summary Table:
Type of Sintering Furnace | Key Features | Applications |
---|---|---|
Pusher Furnaces | Continuous train, high-volume production | Uniform heating for ceramics, metals |
Walking-Beam Furnaces | Low friction, high precision | Delicate or high-precision components |
Vacuum Sintering Furnaces | Temperature ranges (up to 2400℃), vacuum levels | Ceramics, metals, composites |
Resistance Sintering Furnaces | Electric heating elements | Versatile industrial use |
Induction Sintering Furnaces | Electromagnetic induction | Conductive materials |
Microwave Sintering | Rapid, uniform heating | Advanced materials, faster processing |
Need help choosing the right sintering furnace? Contact our experts today for tailored solutions!