Sintering is a critical process in materials science, used to bond powdered materials into a solid structure through heat and/or pressure. There are several types of sintering processes, each tailored to specific materials and applications. These include Solid-State Sintering, Liquid Phase Sintering, Reactive Sintering, Microwave Sintering, Spark Plasma Sintering (SPS), Hot Isostatic Pressing (HIP), Conventional Sintering, High-Temperature Sintering, Direct Metal Laser Sintering (DMLS), and Electric Current-Assisted Sintering. Each method has unique mechanisms and advantages, making them suitable for different industrial and manufacturing needs.
Key Points Explained:
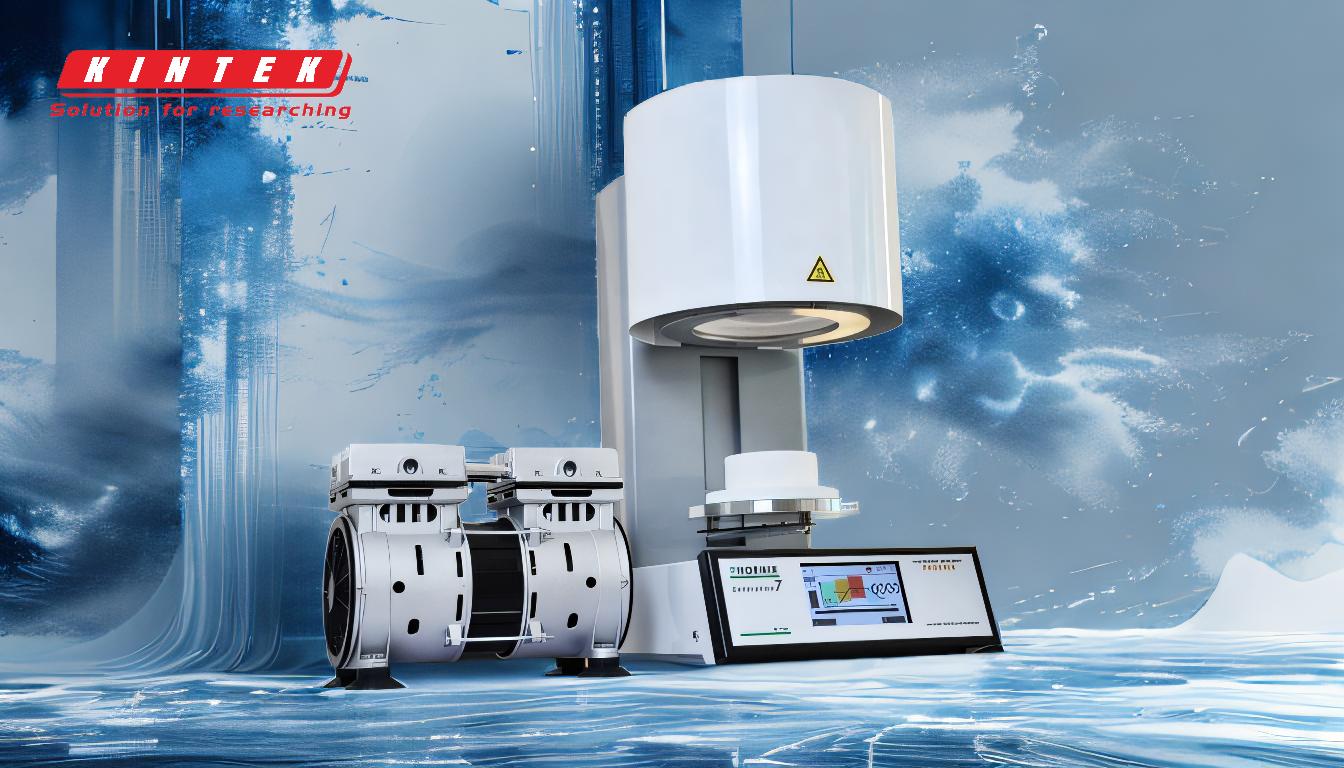
-
Solid-State Sintering
- Mechanism: Powdered material is heated just below its melting point, allowing atomic diffusion to bond particles without liquefaction.
- Applications: Commonly used for ceramics and metals where maintaining material purity is critical.
- Advantages: Produces dense, high-strength materials with minimal impurities.
-
Liquid Phase Sintering (LPS)
- Mechanism: A solvent liquid is introduced to reduce porosity and enhance bonding, which is later driven off by heating.
- Applications: Ideal for materials like tungsten carbide and certain ceramics.
- Advantages: Accelerates densification and improves material uniformity.
-
Reactive Sintering
- Mechanism: Involves a chemical reaction between powder particles during heating, forming a new compound.
- Applications: Used in advanced ceramics and intermetallic compounds.
- Advantages: Enables the creation of unique material properties through in-situ reactions.
-
Microwave Sintering
- Mechanism: Uses microwave energy to heat the material uniformly and rapidly.
- Applications: Particularly effective for ceramics and composites.
- Advantages: Faster processing times and energy efficiency compared to conventional methods.
-
Spark Plasma Sintering (SPS)
- Mechanism: Combines electric current and physical compression to sinter materials at lower temperatures and shorter times.
- Applications: Suitable for advanced materials like nanomaterials and composites.
- Advantages: Reduces grain growth and enhances material properties.
-
Hot Isostatic Pressing (HIP)
- Mechanism: Applies high pressure and temperature simultaneously to densify and fuse powder particles.
- Applications: Used in aerospace and medical industries for high-performance components.
- Advantages: Produces materials with near-theoretical density and excellent mechanical properties.
-
Conventional Sintering
- Mechanism: Involves heating the powder compact without external pressure.
- Applications: Widely used in traditional ceramics and metal powder industries.
- Advantages: Simple and cost-effective for large-scale production.
-
High-Temperature Sintering
- Mechanism: Operates at elevated temperatures to reduce surface oxidation and improve mechanical properties.
- Applications: Common in refractory materials and high-performance alloys.
- Advantages: Enhances material strength and durability.
-
Direct Metal Laser Sintering (DMLS)
- Mechanism: A 3D printing technique that uses a laser to sinter metal powder layer by layer.
- Applications: Used in additive manufacturing for complex metal components.
- Advantages: Allows for intricate designs and rapid prototyping.
-
Electric Current-Assisted Sintering
- Mechanism: Utilizes electric current to facilitate sintering, often combined with pressure.
- Applications: Suitable for advanced materials like conductive ceramics.
- Advantages: Reduces processing time and energy consumption.
Each sintering method has its own set of advantages and limitations, making it essential to choose the appropriate technique based on the material properties and desired outcomes. Understanding these processes is crucial for optimizing manufacturing efficiency and achieving high-quality end products.
Summary Table:
Sintering Method | Mechanism | Applications | Advantages |
---|---|---|---|
Solid-State Sintering | Heated just below melting point, atomic diffusion bonds particles | Ceramics, metals requiring high purity | Dense, high-strength materials with minimal impurities |
Liquid Phase Sintering (LPS) | Solvent liquid enhances bonding, driven off by heating | Tungsten carbide, certain ceramics | Accelerates densification, improves uniformity |
Reactive Sintering | Chemical reaction forms new compounds during heating | Advanced ceramics, intermetallic compounds | Creates unique material properties through in-situ reactions |
Microwave Sintering | Microwave energy heats material uniformly and rapidly | Ceramics, composites | Faster processing, energy-efficient |
Spark Plasma Sintering (SPS) | Electric current + compression at lower temperatures | Nanomaterials, composites | Reduces grain growth, enhances material properties |
Hot Isostatic Pressing (HIP) | High pressure + temperature densifies powder particles | Aerospace, medical components | Near-theoretical density, excellent mechanical properties |
Conventional Sintering | Heating without external pressure | Traditional ceramics, metal powder industries | Simple, cost-effective for large-scale production |
High-Temperature Sintering | Elevated temperatures reduce oxidation, improve mechanical properties | Refractory materials, high-performance alloys | Enhances strength and durability |
Direct Metal Laser Sintering (DMLS) | Laser sinters metal powder layer by layer | Additive manufacturing for complex metal components | Intricate designs, rapid prototyping |
Electric Current-Assisted Sintering | Electric current facilitates sintering, often with pressure | Conductive ceramics | Reduces processing time, energy-efficient |
Need help selecting the right sintering method for your application? Contact our experts today for personalized guidance!