Atomic Layer Deposition (ALD) is a highly precise thin-film deposition technique that enables the creation of uniform, conformal coatings at the atomic level. It is widely used in industries such as semiconductors, energy storage, optics, and biomedical devices. ALD's ability to produce ultra-thin films with exceptional control over thickness and composition makes it indispensable for applications like transistor gate oxides, protective coatings, and nanomaterials. Its versatility and scalability further enhance its utility in both research and industrial settings.
Key Points Explained:
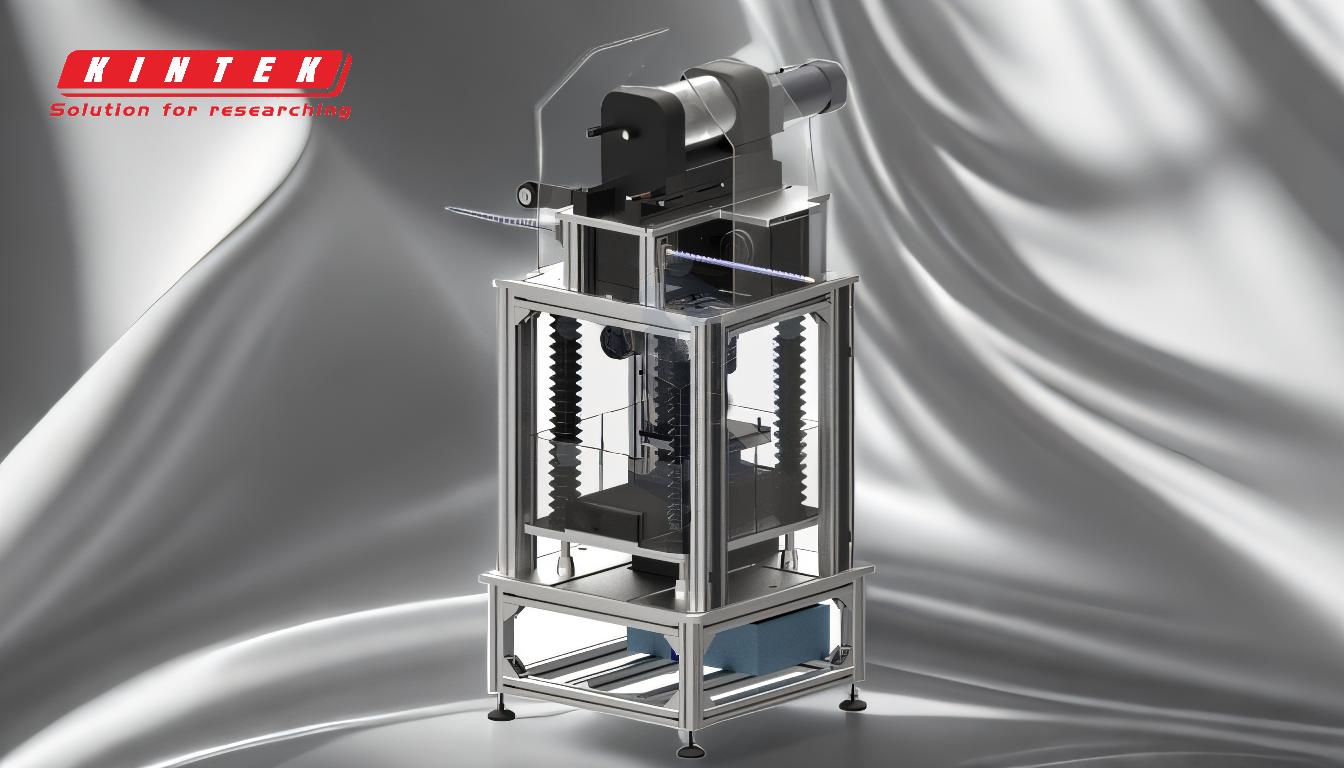
-
Semiconductor Industry Applications:
- Transistor Gate Oxides: ALD is extensively used to deposit high-k dielectric materials (e.g., hafnium oxide) in transistors, enabling smaller and more efficient semiconductor devices.
- Interconnects and Barriers: It creates thin, uniform barrier layers to prevent diffusion of metals like copper into silicon, improving device reliability.
- 3D NAND Memory: ALD is critical for depositing layers in complex 3D structures, ensuring uniformity even in high-aspect-ratio features.
-
Energy Storage and Conversion:
- Lithium-Ion Batteries: ALD is used to coat electrodes with ultrathin films, enhancing conductivity, stability, and lifespan.
- Solar Cells: It improves the efficiency of photovoltaic devices by depositing anti-reflective and passivation layers.
- Fuel Cells: ALD coatings enhance the performance and durability of catalysts and membranes.
-
Optics and Photonics:
- Anti-Reflective Coatings: ALD deposits precise layers on optical components to reduce reflection and improve light transmission.
- Waveguides and Filters: It enables the fabrication of nanoscale optical devices with tailored properties.
-
Biomedical Applications:
- Biocompatible Coatings: ALD is used to create thin films on medical implants, improving biocompatibility and reducing rejection.
- Drug Delivery Systems: It can coat nanoparticles for controlled drug release, enhancing therapeutic efficacy.
-
Protective and Functional Coatings:
- Corrosion Resistance: ALD provides ultra-thin, conformal coatings that protect metals and alloys from environmental degradation.
- Hydrophobic and Hydrophilic Surfaces: It can tailor surface properties for specific applications, such as self-cleaning or anti-fogging.
-
Nanotechnology and Research:
- Nanomaterials: ALD is used to synthesize and modify nanomaterials with precise control over size, shape, and composition.
- Catalysis: It deposits catalytic materials with high surface area and activity, improving reaction efficiency.
-
Advantages of ALD:
- Atomic-Level Precision: ALD allows for thickness control at the angstrom level, ensuring uniformity and reproducibility.
- Conformality: It can coat complex geometries and high-aspect-ratio structures with ease.
- Scalability: ALD is compatible with both laboratory-scale research and industrial-scale production.
-
Challenges and Future Directions:
- Cost and Speed: ALD can be slower and more expensive than other deposition methods, but ongoing research aims to improve throughput and reduce costs.
- Material Diversity: Expanding the range of materials that can be deposited via ALD remains an active area of research.
In summary, ALD is a transformative technology with applications spanning electronics, energy, optics, and biomedicine. Its unparalleled precision and versatility make it a cornerstone of modern materials science and engineering.
Summary Table:
Industry | Applications |
---|---|
Semiconductors | Transistor gate oxides, interconnects, 3D NAND memory |
Energy Storage | Lithium-ion batteries, solar cells, fuel cells |
Optics & Photonics | Anti-reflective coatings, waveguides, filters |
Biomedical Devices | Biocompatible coatings, drug delivery systems |
Protective Coatings | Corrosion resistance, hydrophobic/hydrophilic surfaces |
Nanotechnology | Nanomaterials synthesis, catalysis |
Advantages | Atomic-level precision, conformality, scalability |
Challenges | Cost, speed, material diversity |
Discover how ALD can revolutionize your projects—contact our experts today for tailored solutions!