The sintering process is influenced by several critical variables that determine the final properties of the sintered material. These variables include temperature, heating rate, applied pressure, particle size, composition, and the sintering atmosphere (such as air, vacuum, or inert gases like argon/nitrogen). Each of these factors plays a unique role in the sintering kinetics, densification, and overall material behavior. For instance, higher temperatures and finer particle sizes generally enhance densification, while the choice of atmosphere can affect oxidation or contamination. Understanding and optimizing these variables is essential for achieving desired material properties such as tensile strength, bending fatigue strength, and impact energy.
Key Points Explained:
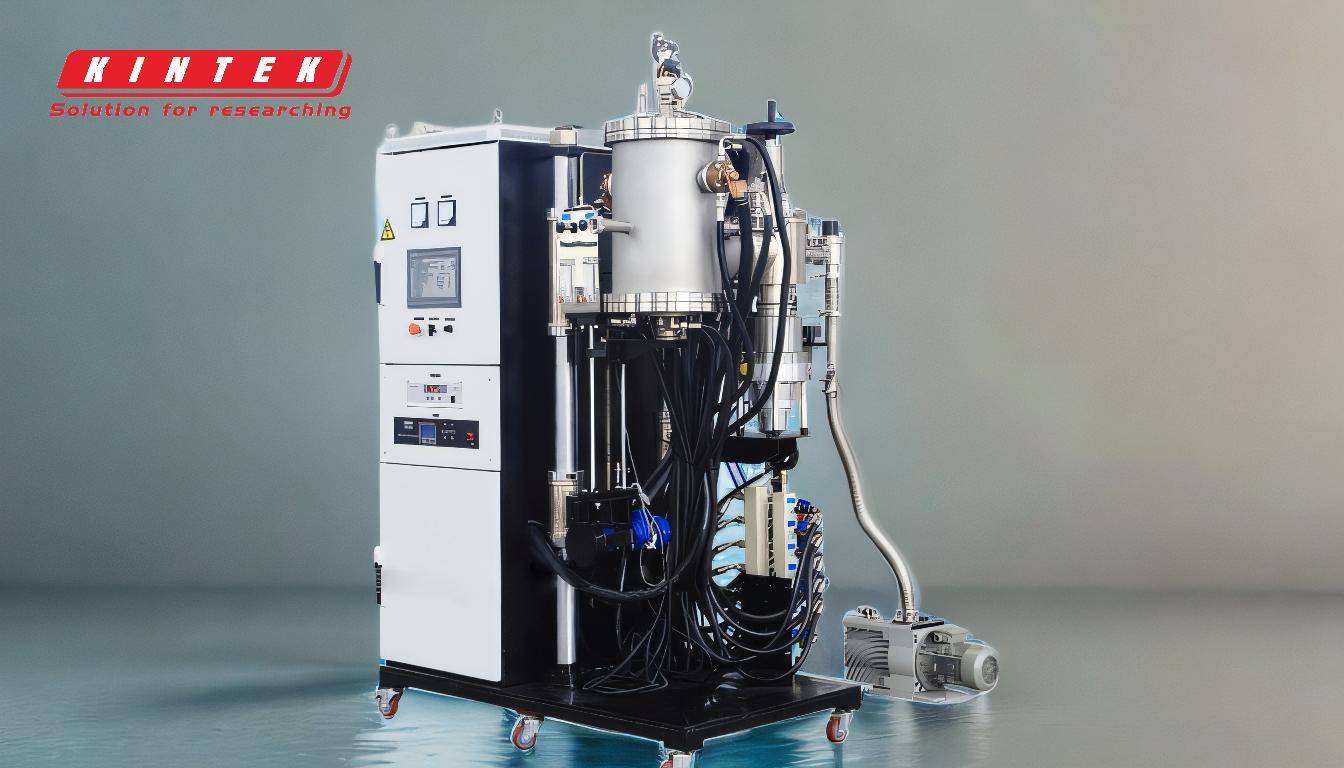
-
Temperature:
- Temperature is one of the most critical variables in sintering. It directly influences sintering kinetics and the final material properties.
- Higher temperatures generally accelerate atomic diffusion, leading to better particle bonding and densification.
- However, excessively high temperatures can cause undesirable grain growth or melting, which may compromise material integrity.
-
Heating Rate:
- The heating rate determines how quickly the material reaches the sintering temperature.
- A controlled heating rate is essential to avoid thermal shock, which can lead to cracking or uneven densification.
- Faster heating rates can sometimes improve productivity but must be balanced against the risk of defects.
-
Applied Pressure:
- Pressure enhances particle rearrangement and helps eliminate porosity during sintering.
- Higher pressures can lead to more uniform densification and improved mechanical properties.
- Pressure-assisted sintering techniques, such as hot pressing or spark plasma sintering, are often used to achieve high-density materials.
-
Particle Size:
- Smaller particle sizes generally promote better densification due to increased surface area and higher driving forces for sintering.
- Fine powders can lead to more homogeneous microstructures and improved mechanical properties.
- However, excessively fine particles may agglomerate, requiring careful handling and processing.
-
Composition:
- The chemical composition of the material affects its sintering behavior and final properties.
- Homogeneous compositions tend to sinter more uniformly, while heterogeneous compositions may lead to uneven densification or phase separation.
- The presence of additives or dopants can also influence sintering kinetics and material performance.
-
Sintering Atmosphere:
- The choice of sintering atmosphere (e.g., air, vacuum, or inert gases like argon/nitrogen) can significantly impact the final material properties.
- An inert atmosphere prevents oxidation and contamination, which is particularly important for reactive materials.
- Vacuum sintering can help remove volatile impurities and reduce porosity, but it may require specialized equipment.
-
Cooling Rate:
- The cooling rate after sintering affects the microstructure and mechanical properties of the material.
- Controlled cooling can help achieve desired phase transformations and minimize residual stresses.
- Rapid cooling may lead to a finer grain structure but could also introduce thermal stresses.
-
Liquid Phase Control:
- In some sintering processes, a liquid phase may form, which can enhance densification but must be carefully controlled.
- Excessive liquid phase can lead to grain boundary weakening or phase separation, compromising material properties.
- The amount of liquid phase is often optimized based on the desired microstructure and mechanical performance.
By carefully controlling these variables, manufacturers can tailor the sintering process to achieve specific material properties, such as increased tensile strength, bending fatigue strength, and impact energy. Each variable interacts with the others, making it essential to consider the entire sintering system when optimizing the process.
Summary Table:
Variable | Role in Sintering | Key Considerations |
---|---|---|
Temperature | Influences sintering kinetics and densification | Higher temps enhance bonding; excessive temps risk grain growth or melting. |
Heating Rate | Determines speed to sintering temperature | Controlled rates prevent thermal shock; faster rates improve productivity but risk defects. |
Applied Pressure | Enhances particle rearrangement and porosity elimination | Higher pressures improve densification; techniques like hot pressing are used for high-density results. |
Particle Size | Smaller particles promote better densification | Fine powders improve microstructure; excessive fineness may cause agglomeration. |
Composition | Affects sintering behavior and final properties | Homogeneous compositions sinter uniformly; additives or dopants influence performance. |
Sintering Atmosphere | Impacts oxidation, contamination, and porosity | Inert gases prevent oxidation; vacuum reduces impurities but requires specialized equipment. |
Cooling Rate | Affects microstructure and mechanical properties | Controlled cooling minimizes stresses; rapid cooling may refine grain structure but introduce stresses. |
Liquid Phase Control | Enhances densification but must be controlled | Excessive liquid phase can weaken grain boundaries; optimization is key for desired properties. |
Optimize your sintering process for superior material properties—contact our experts today!