Physical Vapor Deposition (PVD) is a widely used technique for depositing thin films of material onto a substrate. The process involves the transition of a coating substance from a condensed form to a vapor form and then back to a condensed form as a thin film on the surface of items. The major variants of PVD include vacuum or thermal evaporation, ion plating, and sputtering. Each of these methods has its own unique characteristics and applications, but they all share the common principle of being dry coating methods.
Key Points Explained:
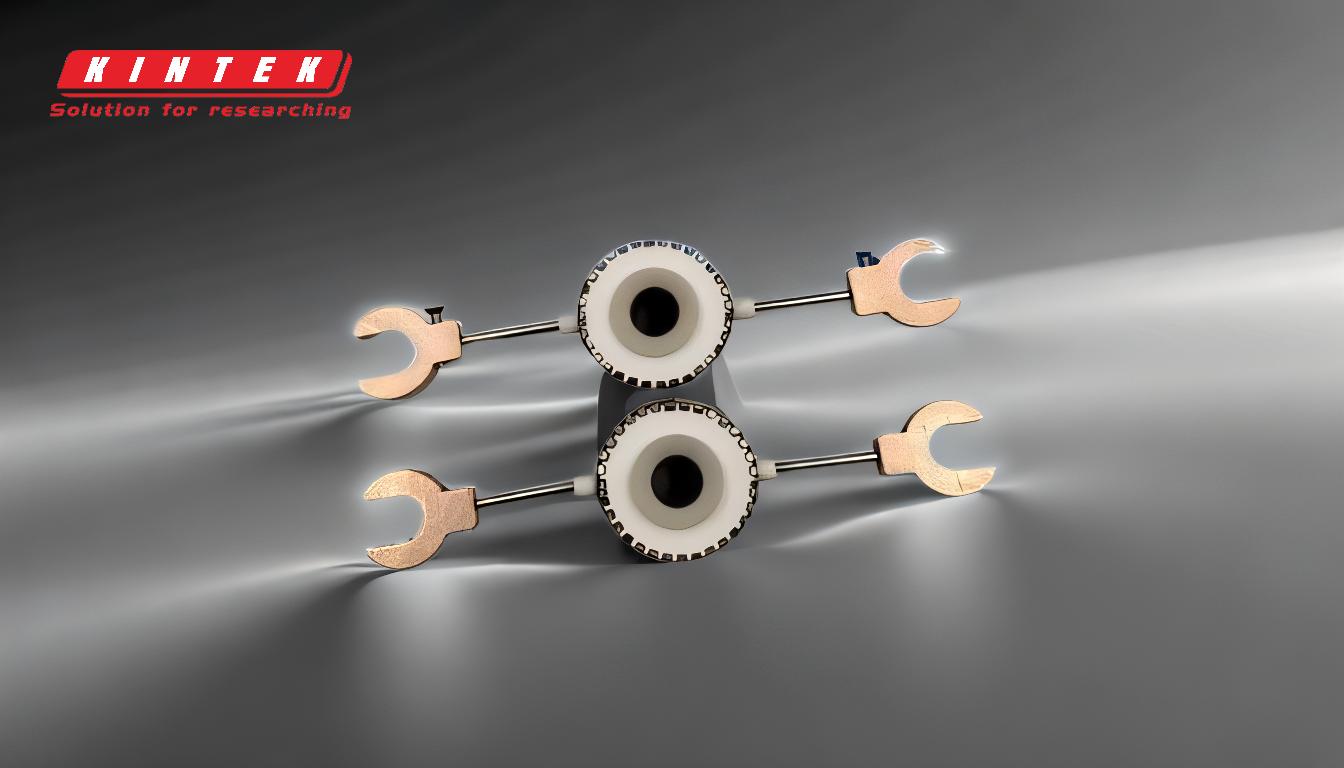
-
Vacuum or Thermal Evaporation:
- Process: In this method, the material to be deposited is heated in a vacuum until it vaporizes. The vapor then condenses on the cooler substrate, forming a thin film.
- Applications: This method is commonly used for depositing metals, alloys, and some compounds. It is particularly useful for applications requiring high purity and uniformity.
- Advantages: High deposition rates, good uniformity, and the ability to deposit a wide range of materials.
- Limitations: Limited to materials that can be vaporized at reasonable temperatures, and the process can be less effective for complex geometries.
-
Ion Plating:
- Process: Ion plating involves the use of a plasma to ionize the vaporized material before it deposits on the substrate. This can be done by either sputtering or evaporation, with the addition of a plasma to enhance adhesion and film properties.
- Applications: This method is used for applications requiring strong adhesion, such as in the coating of cutting tools, optical components, and decorative finishes.
- Advantages: Improved adhesion, better density, and enhanced film properties due to the ion bombardment.
- Limitations: More complex equipment and process control are required compared to simple evaporation or sputtering.
-
Sputtering:
- Process: Sputtering involves bombarding a target material with high-energy ions, causing atoms to be ejected from the target and deposited onto the substrate.
- Applications: This method is widely used in the semiconductor industry, for coating optical components, and in the production of thin-film solar cells.
- Advantages: Ability to deposit a wide range of materials, including metals, alloys, and compounds, with good uniformity and control over film properties.
- Limitations: Lower deposition rates compared to evaporation, and the process can be more complex and costly.
-
Ion Beam Deposition:
- Process: In this method, a focused ion beam is used to sputter material from a target, which is then deposited onto the substrate. The ion beam can be directed and controlled with high precision.
- Applications: This technique is used for applications requiring precise control over film thickness and composition, such as in the production of microelectronic devices and optical coatings.
- Advantages: High precision and control over the deposition process, ability to deposit complex materials.
- Limitations: Limited deposition rates and higher equipment costs.
-
Other Variants:
- Arc Vapor Deposition: This method uses an electric arc to vaporize the target material, which is then deposited onto the substrate. It is particularly useful for depositing hard coatings, such as titanium nitride.
- Pulsed Laser Deposition (PLD): In PLD, a high-power laser is used to ablate material from a target, which is then deposited onto the substrate. This method is used for depositing complex oxides and other materials with precise stoichiometry.
In summary, the major variants of PVD—vacuum or thermal evaporation, ion plating, and sputtering—each have their unique processes, applications, advantages, and limitations. Understanding these variants is crucial for selecting the appropriate PVD method for specific applications, ensuring optimal performance and efficiency in thin-film deposition processes.
Summary Table:
Variant | Process | Applications | Advantages | Limitations |
---|---|---|---|---|
Vacuum Evaporation | Material is heated in a vacuum until vaporized, then condenses on substrate. | Metals, alloys, high-purity applications. | High deposition rates, good uniformity, wide material range. | Limited to vaporizable materials, less effective for complex geometries. |
Ion Plating | Uses plasma to ionize vaporized material before deposition. | Cutting tools, optical components, decorative finishes. | Improved adhesion, better density, enhanced film properties. | Requires complex equipment and process control. |
Sputtering | Target material is bombarded with ions, ejecting atoms for deposition. | Semiconductors, optical components, thin-film solar cells. | Wide material range, good uniformity, precise control over film properties. | Lower deposition rates, higher complexity and cost. |
Ion Beam Deposition | Focused ion beam sputters material for precise deposition. | Microelectronics, optical coatings. | High precision, ability to deposit complex materials. | Limited deposition rates, higher equipment costs. |
Other Variants | Includes arc vapor deposition and pulsed laser deposition (PLD). | Hard coatings (e.g., titanium nitride), complex oxides with precise stoichiometry. | Specific advantages for niche applications. | Varied limitations based on method. |
Need help selecting the right PVD method for your application? Contact our experts today for tailored solutions!