Biomass conversion technologies are essential for transforming organic materials into energy and biofuels. These technologies are broadly categorized into thermochemical and biochemical methods. Thermochemical methods include combustion, gasification, and pyrolysis, which convert biomass into heat, syngas, and bio-oil. Biochemical methods, such as anaerobic digestion and fermentation, break down biomass into biofuels through microbial processes. Each method has its unique advantages and challenges, with thermochemical processes being more versatile and biochemical methods being environmentally friendly but less commercially stable. Understanding these technologies helps in selecting the right approach for energy production based on the type of biomass and desired end product.
Key Points Explained:
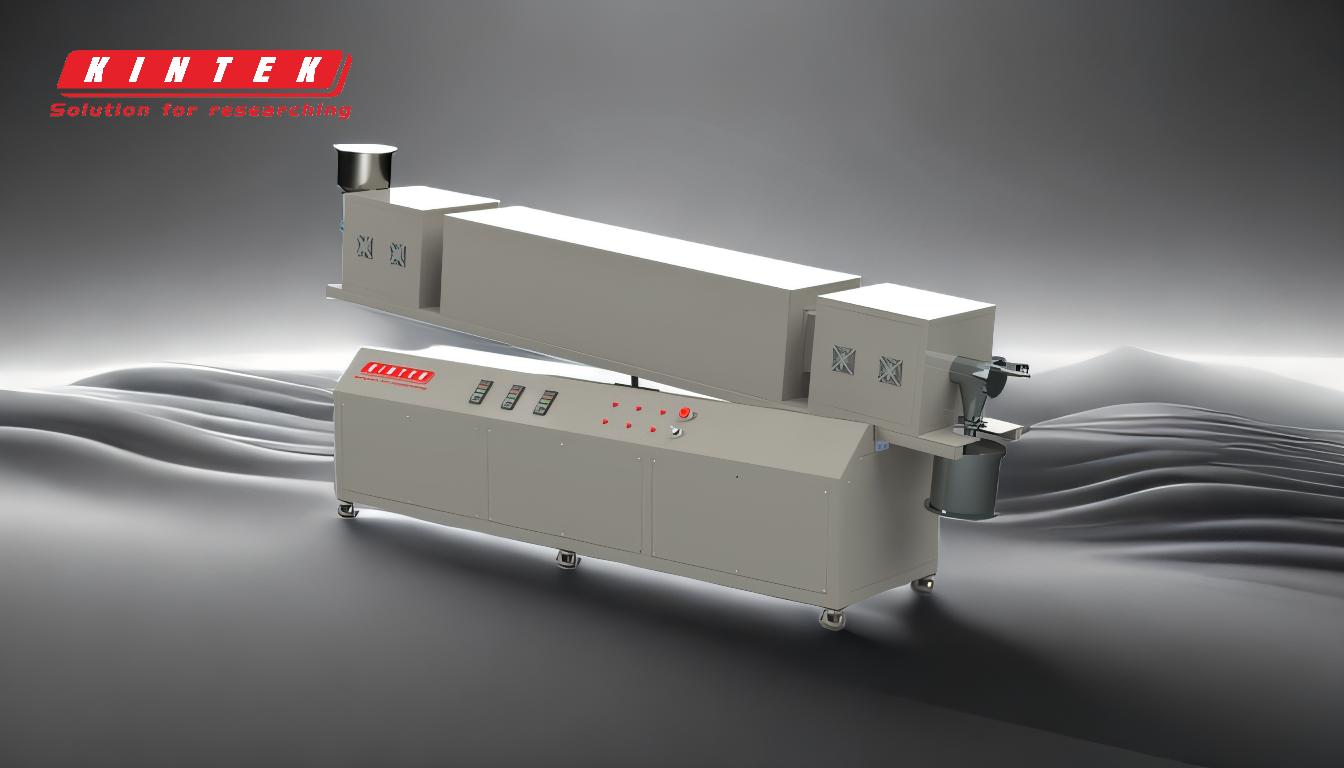
-
Thermochemical Conversion Technologies:
-
Combustion:
- Direct burning of biomass to produce heat and electricity.
- Commonly used in power plants and industrial settings.
- Example: Burning wood or agricultural residues to generate steam for turbines.
-
Gasification:
- Converts biomass into syngas (a mixture of hydrogen, carbon monoxide, and methane) through partial oxidation at high temperatures.
- Syngas can be used for electricity generation or as a precursor for chemicals.
- Example: Converting wood chips into syngas for power generation.
-
Pyrolysis:
- Thermal decomposition of biomass in the absence of oxygen to produce bio-oil, syngas, and biochar.
- Bio-oil can be refined into fuels, while biochar is used as a soil amendment.
- Example: Heating agricultural waste to produce bio-oil for fuel.
-
Combustion:
-
Biochemical Conversion Technologies:
-
Anaerobic Digestion:
- Breakdown of organic matter by microorganisms in the absence of oxygen to produce biogas (mainly methane and carbon dioxide).
- Biogas can be used for heating, electricity, or as a vehicle fuel.
- Example: Processing animal manure in biogas plants to produce methane.
-
Fermentation:
- Conversion of sugars in biomass into biofuels like ethanol through microbial action.
- Commonly used for producing bioethanol from crops like corn or sugarcane.
- Example: Fermenting corn starch to produce ethanol for blending with gasoline.
-
Anaerobic Digestion:
-
Comparison of Thermochemical and Biochemical Methods:
-
Thermochemical Methods:
- More versatile, capable of handling a wide range of biomass types.
- Higher energy efficiency and faster processing times.
- Example: Gasification can process both dry and wet biomass.
-
Biochemical Methods:
- Environmentally friendly, with lower greenhouse gas emissions.
- Limited by the type of biomass (e.g., fermentation requires sugar-rich feedstocks).
- Example: Anaerobic digestion is effective for wet waste but not for dry materials.
-
Thermochemical Methods:
-
Steps in Biomass Energy Conversion:
-
Collection and Preparation:
- Biomass is collected, dried, and processed to remove impurities.
- Example: Harvesting and chipping wood for combustion.
-
Conversion:
- Biomass undergoes thermochemical or biochemical processes to produce energy or biofuels.
- Example: Burning wood in a boiler to produce steam.
-
Energy Utilization:
- The produced energy (heat, electricity, or biofuels) is used for various applications.
- Example: Using biogas from anaerobic digestion to generate electricity.
-
Collection and Preparation:
-
Challenges and Considerations:
-
Feedstock Availability:
- The type and availability of biomass influence the choice of conversion technology.
- Example: Agricultural residues are suitable for combustion, while wet waste is better for anaerobic digestion.
-
Commercial Viability:
- Biochemical methods are less stable at a commercial level due to reliance on food-based raw materials.
- Example: Fermentation for bioethanol production competes with food supply.
-
Environmental Impact:
- Thermochemical methods may produce emissions, while biochemical methods are more sustainable.
- Example: Pyrolysis produces biochar, which can sequester carbon in soil.
-
Feedstock Availability:
-
Future Trends:
-
Integration of Technologies:
- Combining thermochemical and biochemical methods for more efficient energy production.
- Example: Using pyrolysis to produce bio-oil and then refining it through biochemical processes.
-
Advanced Feedstocks:
- Development of non-food biomass sources like algae and energy crops.
- Example: Cultivating algae for biofuel production through fermentation.
-
Integration of Technologies:
Understanding these biomass conversion technologies is crucial for optimizing energy production and addressing environmental concerns. Each method has its strengths and limitations, making it essential to choose the right technology based on specific needs and conditions.
Summary Table:
Category | Technologies | Key Processes | Examples |
---|---|---|---|
Thermochemical Methods | Combustion, Gasification, Pyrolysis | Direct burning, partial oxidation, thermal decomposition | Wood combustion, syngas production, bio-oil from agricultural waste |
Biochemical Methods | Anaerobic Digestion, Fermentation | Microbial breakdown of organic matter, sugar conversion to biofuels | Biogas from manure, ethanol from corn starch |
Comparison | Thermochemical vs. Biochemical | Versatility vs. environmental friendliness, energy efficiency vs. feedstock limits | Gasification for diverse biomass, fermentation for sugar-rich feedstocks |
Discover the best biomass conversion technology for your needs—contact our experts today!