Hydraulic presses, particularly hydraulic hot press machines, are widely used in industrial applications due to their ability to generate high pressure and precise control. However, they also have several weaknesses that can impact their efficiency, cost, and usability. These include reliance on operator skill, high production costs, sensitivity to temperature and air in the hydraulic fluid, and limitations in speed and automation. Understanding these weaknesses is crucial for making informed decisions when purchasing or operating hydraulic press equipment.
Key Points Explained:
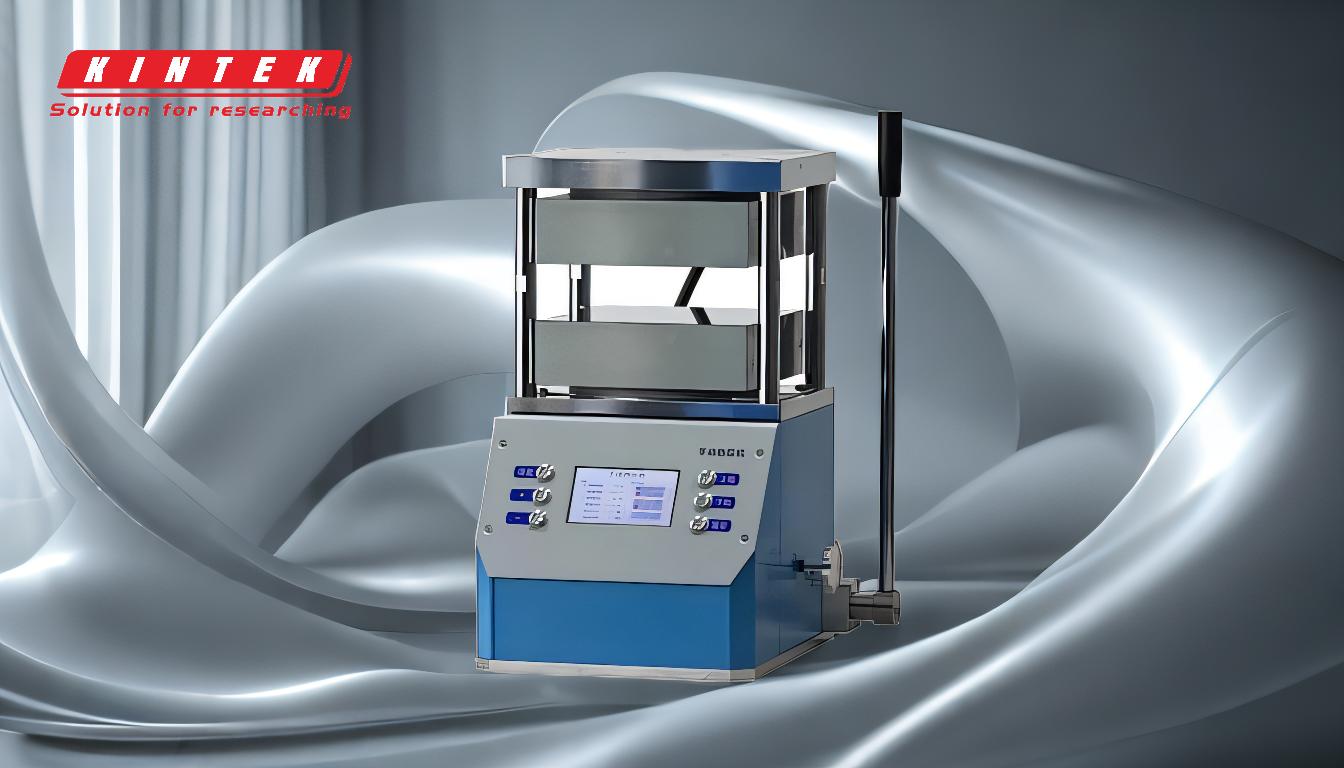
-
Dependence on Operator Skill
- Manual hydraulic presses require significant physical effort and operator involvement, making them labor-intensive and time-consuming for repetitive tasks.
- The pressure applied can vary depending on the operator, leading to inconsistencies in output quality.
- Unlike automated systems, manual presses lack pre-programmed controls, which reduces precision and repeatability.
-
High Production Costs
- Hydraulic systems require robust components to withstand high pressures, increasing manufacturing and maintenance costs.
- The need for solid construction and specialized materials contributes to higher initial investment and operational expenses.
-
Temperature Sensitivity
- Hydraulic fluids are sensitive to high temperatures, with operational limits typically around 50 degrees Celsius.
- Excessive heat can degrade the fluid, leading to reduced efficiency and potential system failures.
- Cooling systems may be required to maintain optimal operating conditions, adding to the complexity and cost.
-
Air in Hydraulic Fluid
- Air trapped in the hydraulic fluid can cause noise, vibration, and disruptions in speed balance.
- This issue can lead to uneven performance and increased wear on system components.
- Regular maintenance is necessary to prevent air contamination, adding to operational downtime and costs.
-
Low Flow Rate and Speed Limitations
- Hydraulic systems generally operate at low speeds due to their low flow rate.
- This limitation can reduce productivity, especially in applications requiring rapid cycling or high-speed operations.
- Alternatives like pneumatic or electric systems may be more suitable for high-speed tasks.
-
Limited Automation in Manual Models
- Manual hydraulic presses lack advanced automation features, such as pre-programmed controls or real-time monitoring.
- This limitation can hinder efficiency and consistency in large-scale or complex operations.
- Automated hydraulic presses, while available, often come at a higher cost and require more sophisticated maintenance.
-
Maintenance and Operational Challenges
- Hydraulic systems require regular maintenance to ensure optimal performance and longevity.
- Issues like fluid leaks, component wear, and contamination can lead to frequent downtime and repair costs.
- Operators need specialized training to handle maintenance and troubleshooting effectively.
By understanding these weaknesses, purchasers and operators of hydraulic hot press machines can make informed decisions, implement mitigation strategies, and explore alternative solutions where necessary. While hydraulic presses offer significant advantages in terms of pressure generation and precision, addressing their limitations is essential for maximizing their utility and cost-effectiveness.
Summary Table:
Weakness | Impact |
---|---|
Dependence on Operator Skill | Labor-intensive, inconsistent output, reduced precision |
High Production Costs | Increased manufacturing, maintenance, and operational expenses |
Temperature Sensitivity | Fluid degradation, system failures, added cooling costs |
Air in Hydraulic Fluid | Noise, vibration, uneven performance, increased wear |
Low Flow Rate and Speed | Reduced productivity, unsuitable for high-speed operations |
Limited Automation | Hindered efficiency, higher costs for automated models |
Maintenance Challenges | Frequent downtime, repair costs, specialized training required |
Looking for solutions to overcome hydraulic press limitations? Contact our experts today to explore alternatives and optimize your operations!