Thin film deposition techniques are methods used to apply thin layers of material onto a substrate, ranging from nanometers to micrometers in thickness. These techniques are broadly categorized into Physical Vapor Deposition (PVD) and Chemical Vapor Deposition (CVD), with each category encompassing various specialized methods. PVD techniques involve the physical transfer of material from a source to a substrate, typically in a vacuum environment, while CVD techniques rely on chemical reactions to deposit thin films. Other advanced methods, such as Atomic Layer Deposition (ALD) and Spray Pyrolysis, offer precise control over film thickness and composition. These techniques are widely used in industries like electronics, optics, and energy to create high-performance coatings and functional layers.
Key Points Explained:
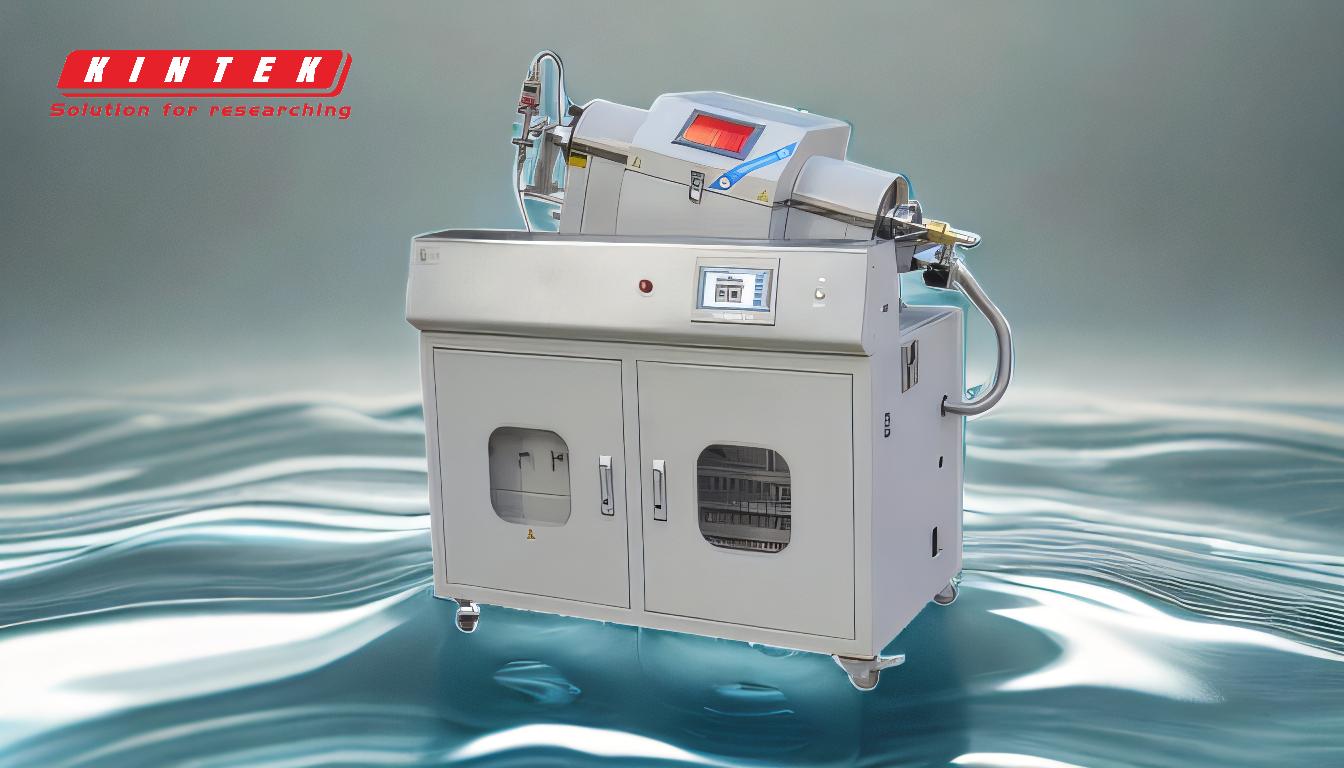
-
Overview of Thin Film Deposition
- Thin film deposition involves applying a thin layer of material onto a substrate.
- The thickness of these films can range from nanometers to micrometers.
- These techniques are essential in industries such as semiconductors, optics, and renewable energy.
-
Categorization of Thin Film Deposition Techniques
- Thin film deposition methods are broadly divided into two categories:
- Physical Vapor Deposition (PVD)
- Chemical Vapor Deposition (CVD)
- Each category includes multiple specialized techniques tailored for specific applications.
- Thin film deposition methods are broadly divided into two categories:
-
Physical Vapor Deposition (PVD)
- PVD involves the physical transfer of material from a source to a substrate, typically in a vacuum environment.
- Common PVD techniques include:
- Sputtering: A target material is bombarded with ions, causing atoms to be ejected and deposited onto the substrate.
- Thermal Evaporation: The source material is heated until it vaporizes and condenses on the substrate.
- Electron Beam Evaporation: An electron beam heats the source material to high temperatures, causing it to vaporize.
- Pulsed Laser Deposition (PLD): A laser ablates the target material, creating a plume that deposits onto the substrate.
- PVD is widely used for creating high-purity, uniform coatings.
-
Chemical Vapor Deposition (CVD)
- CVD relies on chemical reactions to deposit thin films.
- Common CVD techniques include:
- Chemical Bath Deposition: A solution containing the desired material is used to coat the substrate.
- Plasma-Enhanced CVD (PECVD): Plasma is used to enhance the chemical reactions, allowing deposition at lower temperatures.
- Atomic Layer Deposition (ALD): Films are deposited one atomic layer at a time, offering exceptional precision and uniformity.
- CVD is ideal for producing high-purity, conformal coatings, especially in semiconductor manufacturing.
-
Advanced and Hybrid Techniques
-
Atomic Layer Deposition (ALD):
- ALD is a subset of CVD that deposits films one atomic layer at a time.
- It offers unparalleled control over film thickness and uniformity, making it ideal for nanoscale applications.
-
Spray Pyrolysis:
- A solution containing the desired material is sprayed onto the substrate and thermally decomposed to form a thin film.
- This method is cost-effective and suitable for large-area coatings.
-
Atomic Layer Deposition (ALD):
-
Applications of Thin Film Deposition Techniques
- Electronics: Used in semiconductor devices, solar cells, and displays.
- Optics: Applied in anti-reflective coatings, mirrors, and optical filters.
- Energy: Utilized in thin-film batteries and photovoltaic cells.
- Medical Devices: Used for biocompatible coatings and sensors.
-
Advantages and Limitations
- PVD Advantages: High-purity films, excellent adhesion, and suitability for a wide range of materials.
- PVD Limitations: Requires a vacuum environment, which can be expensive and time-consuming.
- CVD Advantages: Conformal coatings, high throughput, and versatility in material choices.
- CVD Limitations: Often requires high temperatures and can involve hazardous chemicals.
- ALD Advantages: Atomic-level precision, excellent uniformity, and low defect density.
- ALD Limitations: Slow deposition rates and high equipment costs.
-
Choosing the Right Technique
- The choice of deposition technique depends on factors such as:
- Desired film properties (e.g., thickness, uniformity, purity).
- Substrate material and geometry.
- Cost and scalability requirements.
- For example, ALD is preferred for nanoscale applications, while CVD is ideal for high-throughput industrial processes.
- The choice of deposition technique depends on factors such as:
-
Future Trends in Thin Film Deposition
- Development of hybrid techniques combining PVD and CVD for enhanced performance.
- Increased use of ALD in emerging technologies like quantum computing and advanced sensors.
- Adoption of environmentally friendly and cost-effective methods like spray pyrolysis for large-scale applications.
By understanding these key points, a purchaser can make informed decisions about which thin film deposition technique best suits their specific needs, balancing factors such as performance, cost, and scalability.
Summary Table:
Category | Key Techniques | Applications |
---|---|---|
Physical Vapor Deposition (PVD) | Sputtering, Thermal Evaporation, Electron Beam Evaporation, Pulsed Laser Deposition | High-purity coatings, optics, semiconductor devices |
Chemical Vapor Deposition (CVD) | Chemical Bath Deposition, Plasma-Enhanced CVD, Atomic Layer Deposition (ALD) | Semiconductor manufacturing, conformal coatings, nanoscale applications |
Advanced Techniques | Atomic Layer Deposition (ALD), Spray Pyrolysis | Nanoscale precision, large-area coatings, cost-effective solutions |
Need help choosing the right thin film deposition technique? Contact our experts today for tailored solutions!