The annealing process is a critical heat treatment method used to alter the physical and sometimes chemical properties of materials, primarily metals, to increase their ductility and reduce hardness. The process typically involves three fundamental stages: Recovery, Recrystallization, and Grain Growth. These stages occur as the material is heated to specific temperatures and then cooled at controlled rates. Understanding these stages is essential for achieving the desired material properties, such as improved machinability, reduced internal stresses, and enhanced structural integrity.
Key Points Explained:
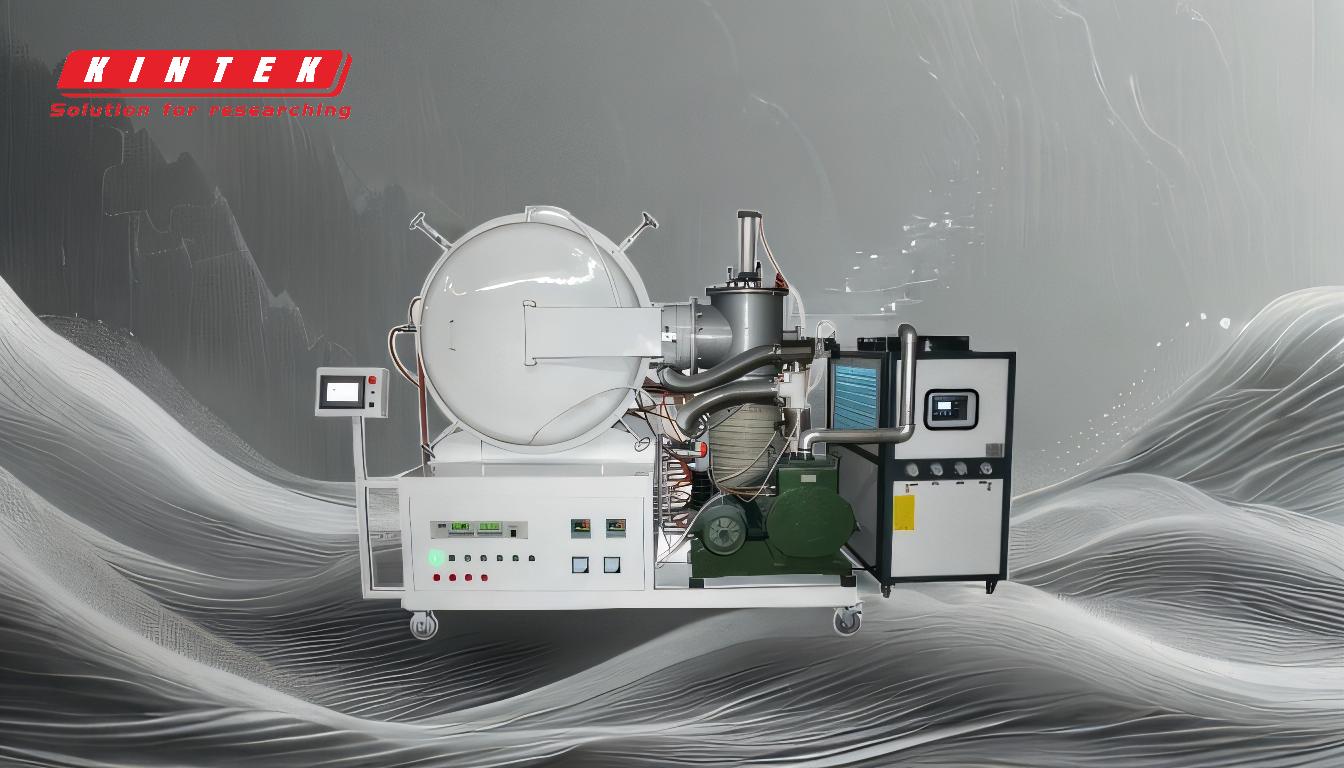
-
Recovery:
- Definition: The first stage of the annealing process where the material is heated to a temperature below its recrystallization point. This stage aims to relieve internal stresses caused by previous mechanical working or thermal processes.
- Process: During recovery, dislocations in the material's crystal structure begin to move and rearrange themselves, reducing the internal energy of the material. This results in a slight reduction in hardness and an increase in ductility.
- Importance: Recovery is crucial for preparing the material for the next stages of annealing, as it sets the foundation for the recrystallization process by stabilizing the microstructure.
-
Recrystallization:
- Definition: The second stage of annealing, where the material is heated to a temperature above its recrystallization point but below its melting point. This stage leads to the formation of new, strain-free grains.
- Process: As the temperature increases, new grains begin to form in areas where the material was previously deformed. These new grains replace the old, deformed grain structure, resulting in a significant reduction in hardness and a substantial increase in ductility.
- Importance: Recrystallization is vital for restoring the material's properties to a more workable state, making it easier to shape or form without cracking or breaking.
-
Grain Growth:
- Definition: The final stage of the annealing process, where the newly formed grains continue to grow as the material is held at the annealing temperature.
- Process: During grain growth, the smaller grains merge to form larger grains, which can lead to a coarser grain structure. This stage is controlled by the holding time at the annealing temperature and the cooling rate.
- Importance: While grain growth can reduce the material's strength, it can also improve its ductility and toughness. However, excessive grain growth can lead to undesirable properties, so it is essential to control this stage carefully.
Practical Considerations:
- Temperature Control: Precise temperature control is crucial throughout the annealing process. Each stage requires specific temperature ranges to achieve the desired material properties.
- Cooling Rate: The rate at which the material is cooled after annealing can significantly affect the final properties. Slow cooling rates are typically used to prevent the introduction of new stresses.
- Material Type: Different materials have different annealing temperature ranges and requirements. For example, steel and aluminum will have distinct annealing processes tailored to their specific properties.
By understanding and carefully controlling these three stages—Recovery, Recrystallization, and Grain Growth—manufacturers can optimize the annealing process to produce materials with the desired mechanical properties for various applications.
Summary Table:
Stage | Definition | Process | Importance |
---|---|---|---|
Recovery | Relieves internal stresses by heating below recrystallization temperature. | Dislocations rearrange, reducing hardness and increasing ductility. | Prepares material for recrystallization by stabilizing microstructure. |
Recrystallization | Forms new, strain-free grains by heating above recrystallization temperature. | New grains replace deformed structure, reducing hardness and increasing ductility. | Restores material properties for easier shaping or forming. |
Grain Growth | Final stage where newly formed grains grow as material is held at temperature. | Smaller grains merge into larger grains, potentially coarsening the structure. | Improves ductility and toughness but must be controlled to avoid excessive growth. |
Optimize your annealing process for superior material properties—contact our experts today!