Sintering is a critical process in materials science, particularly in the production of high-performance materials like zirconia restorations. By subjecting materials to high temperatures in a furnace, sintering enhances their physical and chemical properties, making them more suitable for various applications. Two significant advantages of putting sinter into the furnace are the improvement of material properties, such as strength and conductivity, and the reduction of porosity, which leads to denser and more durable materials. These benefits are achieved through controlled heating and cooling processes, which optimize the material's microstructure.
Key Points Explained:
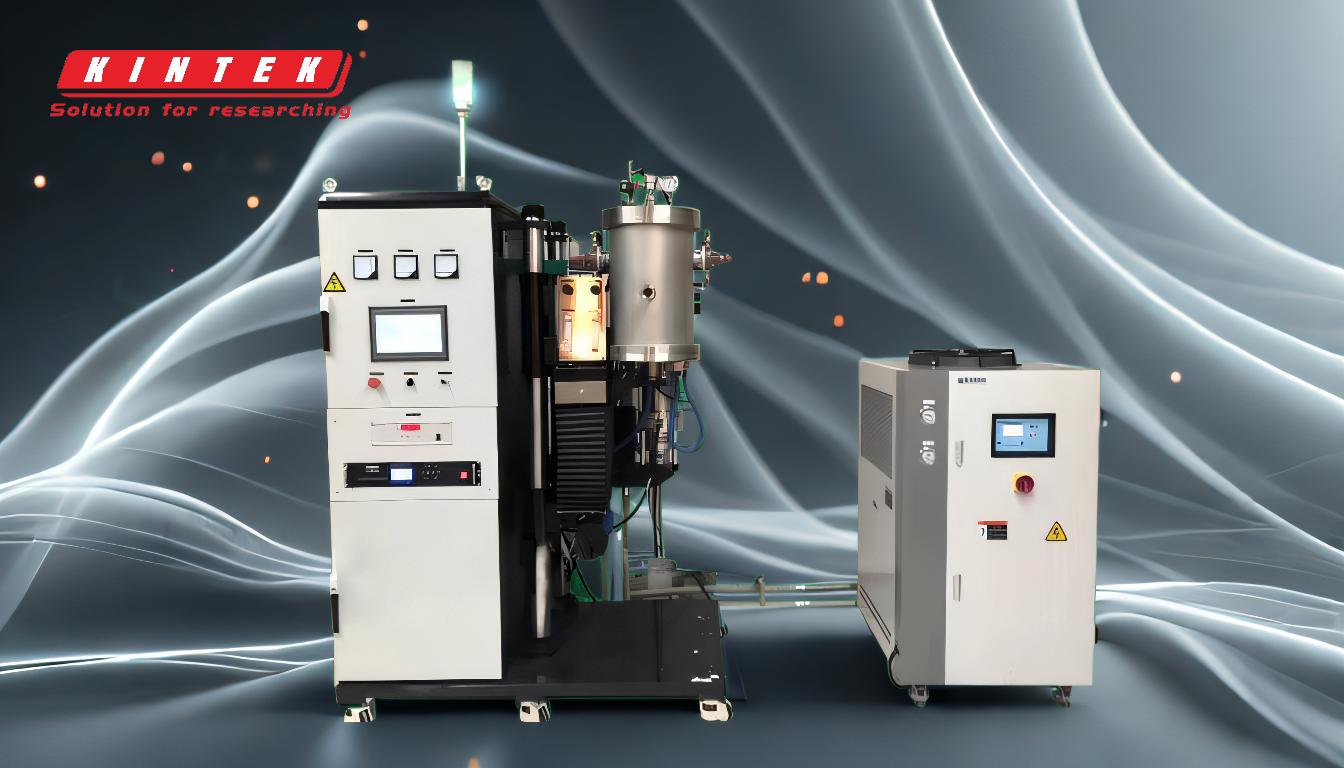
-
Enhancement of Material Properties:
- Sintering significantly improves the mechanical, thermal, and electrical properties of materials. For instance, it increases material strength and integrity, making the final product more durable and reliable.
- The process also enhances thermal and electrical conductivity, which is crucial for applications requiring efficient heat transfer or electrical performance.
- In the case of zirconia restorations, sintering improves translucency, making the material more aesthetically pleasing for dental applications.
-
Reduction of Porosity:
- Sintering effectively reduces the porosity of materials, leading to a denser and more uniform structure. This reduction in porosity enhances properties such as strength, transparency, and thermal conductivity.
- Lower porosity also means fewer defects and a higher-quality final product, which is essential for applications where material integrity is critical, such as in medical devices or aerospace components.
-
Energy Efficiency and Productivity:
- Modern sintering furnaces are designed with high-grade insulation materials that ensure low energy consumption and high heating rates. This efficiency translates to cost savings and faster production times.
- The use of vacuum sintering furnaces, in particular, offers additional benefits such as clean, bright parts and superior quality with fewer defects. These furnaces also provide incredible design flexibility and quick turnaround times, maximizing productivity.
-
Versatility and Application-Specific Benefits:
- Sintering is a versatile process that can be tailored to meet specific application requirements. For example, it can be used to increase strength while maintaining gas absorbency, which is useful in filters or catalysts.
- The ability to customize the sintering process allows for the production of materials with unique properties, making it suitable for a wide range of industries, from healthcare to manufacturing.
In summary, putting sinter into the furnace offers significant advantages, including the enhancement of material properties and the reduction of porosity. These benefits are achieved through controlled heating and cooling processes, which optimize the material's microstructure and lead to higher-quality, more durable products. Additionally, modern sintering furnaces offer energy efficiency and design flexibility, further enhancing the overall productivity and versatility of the sintering process.
Summary Table:
Advantage | Description |
---|---|
Enhancement of Material Properties | Improves mechanical, thermal, and electrical properties, increasing strength and conductivity. |
Reduction of Porosity | Reduces porosity, leading to denser, more durable materials with fewer defects. |
Energy Efficiency | Modern furnaces ensure low energy consumption, high heating rates, and cost savings. |
Versatility | Customizable process for unique material properties, suitable for various industries. |
Unlock the full potential of sintering for your materials—contact us today to learn more!