Overheating the brazing joint before adding filler metal can lead to several detrimental outcomes. The primary risks include oxidation of the base metals, degradation of the joint's mechanical properties, and potential failure of the brazing process. When the joint is overheated, the base metals can oxidize, forming a layer that prevents proper wetting and bonding of the filler metal. This oxidation layer can also weaken the joint, making it more susceptible to cracking or failure under stress. Additionally, overheating can cause the base metals to warp or distort, leading to misalignment and poor joint fit-up. In some cases, excessive heat can even melt the base metals, further compromising the integrity of the joint. To avoid these issues, it is crucial to control the heating process carefully, ensuring that the joint reaches the optimal temperature for brazing without exceeding it.
Key Points Explained:
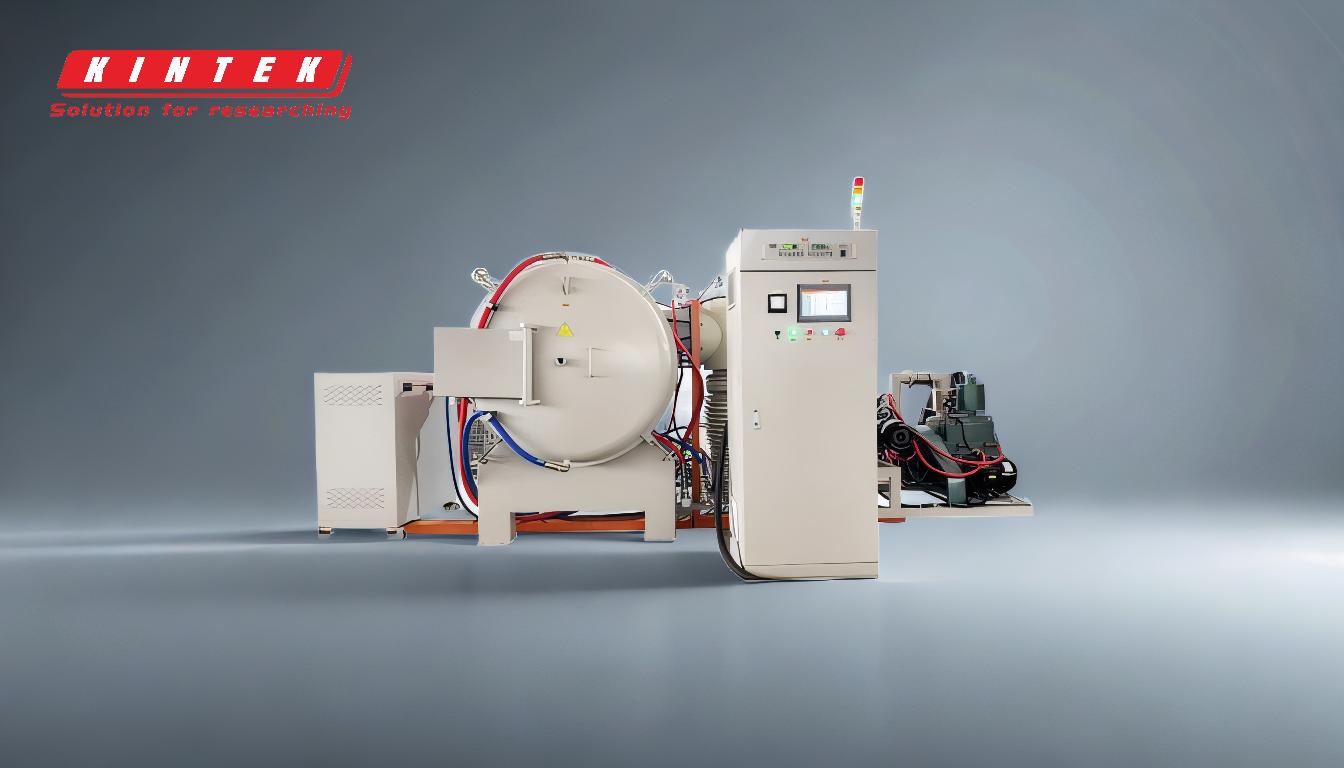
-
Oxidation of Base Metals:
- Overheating the brazing joint can cause the base metals to oxidize. This oxidation forms a layer on the surface of the metals, which can prevent the filler metal from properly wetting and bonding to the base metals.
- The presence of this oxide layer can significantly reduce the strength and integrity of the joint, making it more prone to failure.
-
Degradation of Mechanical Properties:
- Excessive heat can alter the microstructure of the base metals, leading to a degradation of their mechanical properties. This can result in a joint that is weaker and less durable.
- The joint may become brittle, increasing the likelihood of cracking or breaking under stress or load.
-
Warping or Distortion:
- Overheating can cause the base metals to warp or distort. This distortion can lead to misalignment of the joint, making it difficult to achieve a proper fit-up.
- Misaligned joints can result in uneven distribution of the filler metal, leading to weak spots and potential failure points.
-
Melting of Base Metals:
- In extreme cases, overheating can cause the base metals to melt. This melting can compromise the structural integrity of the joint, making it unsuitable for its intended application.
- Melting can also lead to the formation of voids or gaps in the joint, further weakening it.
-
Poor Wetting and Bonding:
- Proper wetting and bonding of the filler metal to the base metals are essential for a strong brazed joint. Overheating can prevent the filler metal from flowing and bonding correctly, resulting in a weak or incomplete joint.
- Poor wetting can also lead to the formation of voids or inclusions within the joint, which can act as stress concentrators and lead to failure.
-
Increased Risk of Joint Failure:
- All of the above factors contribute to an increased risk of joint failure. A joint that has been overheated is more likely to fail under operational stresses, leading to potential safety hazards and costly repairs.
- The failure of a brazed joint can have serious consequences, especially in critical applications such as aerospace, automotive, or industrial equipment.
-
Prevention and Control:
- To prevent these issues, it is essential to control the heating process carefully. This includes using appropriate heating methods, monitoring the temperature closely, and ensuring that the joint reaches the optimal brazing temperature without exceeding it.
- Proper preparation of the joint surfaces, including cleaning and applying flux, can also help to minimize the risk of oxidation and improve the quality of the brazed joint.
By understanding the potential consequences of overheating a brazing joint, you can take the necessary precautions to ensure a successful and durable brazing process.
Summary Table:
Risk | Consequence |
---|---|
Oxidation of Base Metals | Forms a layer preventing proper bonding, weakening the joint. |
Degradation of Mechanical Properties | Weakens and brittles the joint, increasing failure risk. |
Warping or Distortion | Causes misalignment, leading to poor joint fit-up and weak spots. |
Melting of Base Metals | Compromises structural integrity, creating voids or gaps. |
Poor Wetting and Bonding | Results in weak or incomplete joints with potential voids. |
Increased Risk of Joint Failure | Higher likelihood of failure under stress, posing safety and cost concerns. |
Prevention and Control | Use proper heating methods, monitor temperature, and prepare surfaces carefully. |
Ensure your brazing process is flawless—contact our experts today for tailored solutions!