Injection molding machines are versatile manufacturing tools primarily used to produce plastic products through the injection molding process. These machines melt plastic material, inject it into a press mold, and allow it to cool and solidify into the desired shape. The process is widely used across industries to create a vast array of products, from small components like bottle caps to larger items such as automotive parts and household appliances. The technology is valued for its efficiency, precision, and ability to produce high volumes of identical parts with minimal waste.
Key Points Explained:
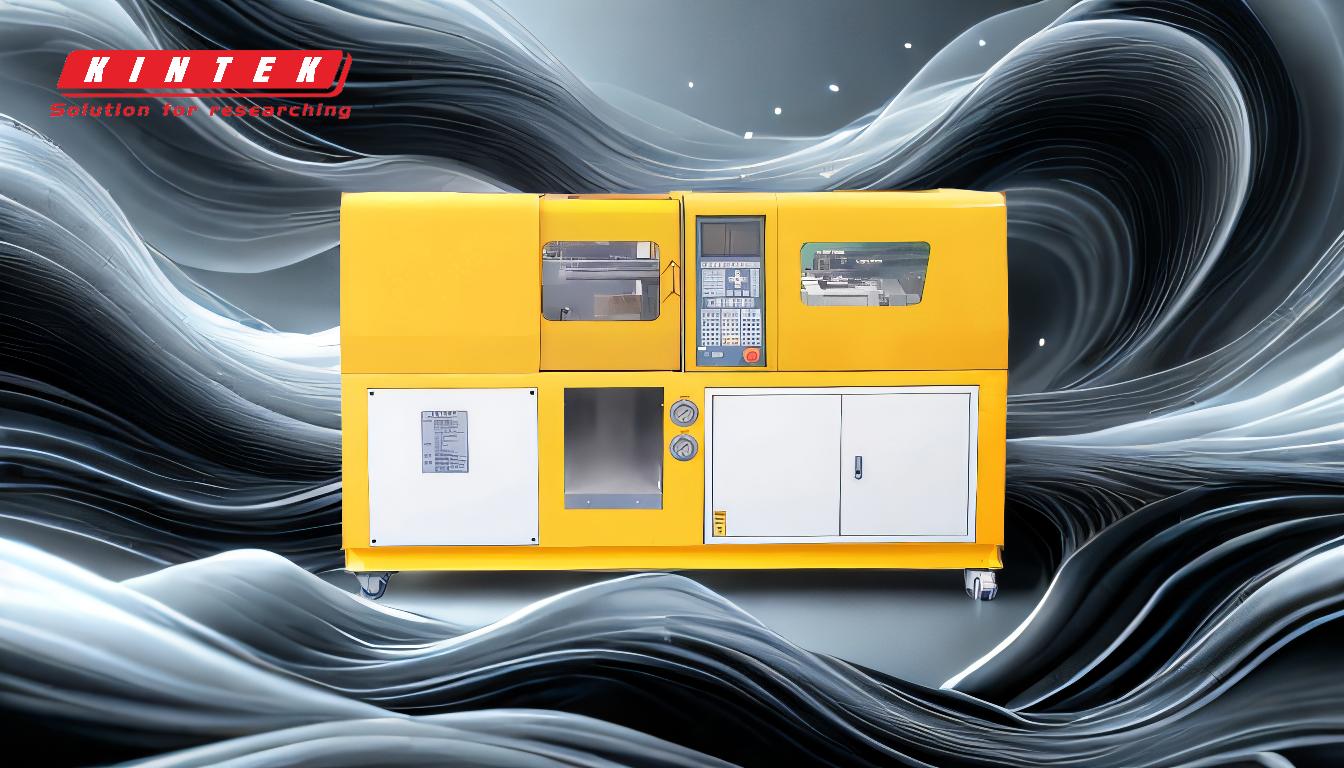
-
Primary Function of Injection Molding Machines:
- Injection molding machines are designed to manufacture plastic products by injecting molten plastic into a mold. The process involves heating plastic pellets until they melt, then forcing the molten material into a mold cavity where it cools and solidifies into the desired shape. This method is highly efficient for mass-producing plastic parts with consistent quality.
-
Types of Products Made:
- Injection molding machines can produce a wide variety of plastic products, including:
- Small Components: Items like bottle caps, buttons, and small gears.
- Consumer Goods: Products such as toys, kitchen utensils, and containers.
- Automotive Parts: Components like dashboards, bumpers, and interior trim.
- Medical Devices: Items such as syringes, IV components, and surgical instruments.
- Industrial Parts: Tools, housings, and machinery components.
- Packaging: Items like plastic bottles, lids, and trays.
- Injection molding machines can produce a wide variety of plastic products, including:
-
Industries Utilizing Injection Molding:
- Injection molding is a cornerstone of manufacturing in numerous industries, including:
- Automotive: For lightweight, durable parts.
- Consumer Electronics: For casings, connectors, and other components.
- Medical: For sterile, precision parts.
- Packaging: For creating containers and closures.
- Construction: For fittings, pipes, and insulation materials.
- Injection molding is a cornerstone of manufacturing in numerous industries, including:
-
Advantages of Injection Molding:
- High Efficiency: Capable of producing large quantities of parts quickly.
- Precision and Consistency: Ensures uniformity in product dimensions and quality.
- Material Versatility: Can process a wide range of thermoplastics and some thermosetting plastics.
- Minimal Waste: Excess material can often be recycled and reused.
- Complex Geometries: Allows for intricate designs and detailed features.
-
Process Overview:
- The injection molding process involves several key steps:
- Material Preparation: Plastic pellets are fed into the machine's hopper.
- Melting: The pellets are heated and melted in the machine's barrel.
- Injection: The molten plastic is injected into the mold under high pressure.
- Cooling: The plastic cools and solidifies within the mold.
- Ejection: The finished part is ejected from the mold, and the cycle repeats.
- The injection molding process involves several key steps:
-
Materials Used:
- Injection molding machines can process a variety of materials, including:
- Thermoplastics: Such as polyethylene (PE), polypropylene (PP), polystyrene (PS), and polycarbonate (PC).
- Thermosetting Plastics: Such as epoxy and phenolic resins.
- Elastomers: For flexible parts.
- Composites: Reinforced plastics with fibers or fillers for enhanced properties.
- Injection molding machines can process a variety of materials, including:
-
Customization and Flexibility:
- Injection molding machines offer significant customization options, allowing manufacturers to produce parts with specific shapes, sizes, and properties. This flexibility is achieved through:
- Mold Design: Custom molds can be created to produce unique shapes and features.
- Material Selection: Different plastics can be chosen based on the desired properties of the final product.
- Process Parameters: Adjustments to temperature, pressure, and cooling times can optimize the molding process.
- Injection molding machines offer significant customization options, allowing manufacturers to produce parts with specific shapes, sizes, and properties. This flexibility is achieved through:
-
Economic and Environmental Considerations:
- Injection molding is cost-effective for large-scale production due to its high output rates and low per-unit costs. Additionally, the process is relatively environmentally friendly, as it generates minimal waste and allows for the recycling of plastic materials.
In summary, injection molding machines are essential tools in modern manufacturing, capable of producing a wide range of plastic products with high precision and efficiency. Their versatility, coupled with the ability to customize molds and materials, makes them indispensable across various industries.
Summary Table:
Key Aspect | Details |
---|---|
Primary Function | Manufactures plastic products by injecting molten plastic into molds. |
Types of Products | Small components, consumer goods, automotive parts, medical devices, etc. |
Industries Served | Automotive, consumer electronics, medical, packaging, construction. |
Advantages | High efficiency, precision, material versatility, minimal waste. |
Process Steps | Material preparation, melting, injection, cooling, ejection. |
Materials Used | Thermoplastics, thermosetting plastics, elastomers, composites. |
Customization | Mold design, material selection, process parameter adjustments. |
Economic & Environmental | Cost-effective for large-scale production, recyclable materials. |
Ready to enhance your manufacturing process? Contact us today to learn more about injection molding solutions!