Physical Vapor Deposition (PVD) is a sophisticated thin-film coating process used to deposit materials on a substrate at an atomic level. It is performed in a vacuum environment and involves four key stages: evaporation, transportation, reaction, and deposition. PVD is widely regarded as an alternative to traditional electroplating, offering superior durability, precision, and environmental benefits. This process is commonly used in industries such as aerospace, automotive, electronics, and medical devices to enhance the surface properties of components, including wear resistance, corrosion resistance, and aesthetic appeal.
Key Points Explained:
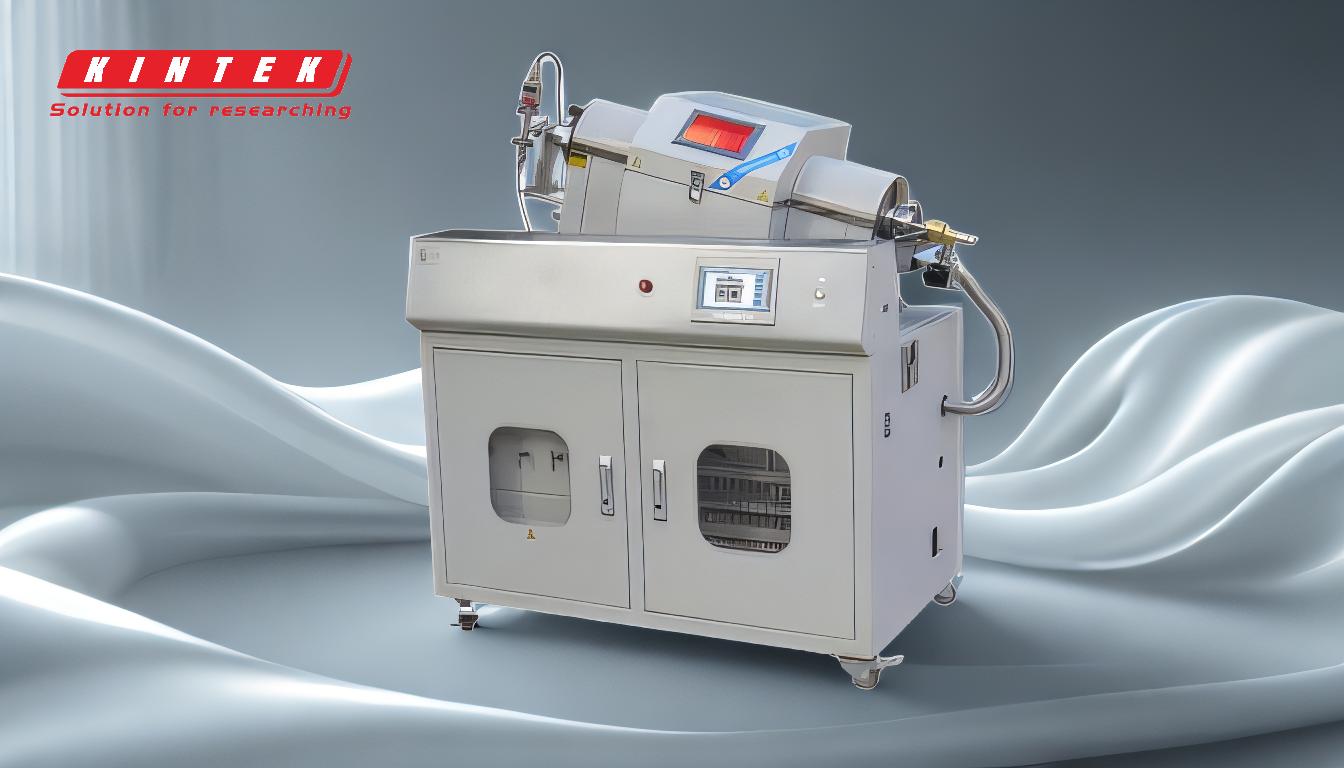
-
Definition of PVD:
- PVD stands for Physical Vapor Deposition, a process where a solid material is vaporized in a vacuum environment and deposited onto a substrate as a thin film. This technique is used to create coatings with specific properties, such as improved hardness, wear resistance, or corrosion resistance.
-
Stages of the PVD Process:
- Evaporation: The target material (e.g., metal or ceramic) is vaporized using methods like sputtering, arc vaporization, or electron beam heating. This converts the solid material into a vapor state.
- Transportation: The vaporized material is transported through the vacuum chamber to the substrate. This step ensures the material reaches the target surface uniformly.
- Reaction: In some cases, the vaporized material reacts with a gas (e.g., nitrogen or oxygen) introduced into the chamber to form a compound coating (e.g., titanium nitride).
- Deposition: The vaporized or reacted material condenses on the substrate, forming a thin, uniform coating.
-
Advantages of PVD:
- Durability: PVD coatings are highly durable and resistant to wear, corrosion, and high temperatures.
- Precision: The process allows for precise control over coating thickness and composition, making it ideal for complex geometries.
- Environmental Benefits: PVD is more environmentally friendly than electroplating, as it produces fewer hazardous byproducts.
- Aesthetic Appeal: PVD coatings can be tailored to achieve specific colors and finishes, enhancing the visual appeal of components.
-
Applications of PVD:
- Aerospace: Used to coat turbine blades and other critical components to improve performance and longevity.
- Automotive: Applied to engine parts, cutting tools, and decorative trim to enhance durability and appearance.
- Electronics: Used in semiconductor manufacturing and to coat connectors for improved conductivity and corrosion resistance.
- Medical Devices: Coating surgical instruments and implants to improve biocompatibility and wear resistance.
-
Comparison to Electroplating:
- PVD is often preferred over electroplating due to its ability to produce thinner, more uniform coatings with superior adhesion and environmental benefits. Electroplating, on the other hand, involves chemical baths and can produce hazardous waste.
-
Materials Used in PVD:
- Common materials include metals (e.g., titanium, chromium, aluminum), ceramics (e.g., titanium nitride, zirconium nitride), and alloys. These materials are chosen based on the desired properties of the final coating.
-
Vacuum Environment:
- The vacuum chamber is essential for the PVD process, as it prevents contamination and allows for precise control over the deposition process. The absence of air or other gases ensures the purity and quality of the coating.
-
Customization and Flexibility:
- PVD allows for a high degree of customization, enabling manufacturers to tailor coatings to specific applications. This flexibility makes it a versatile solution for a wide range of industries.
By understanding these key points, a purchaser can make informed decisions about whether PVD coatings are suitable for their specific needs, considering factors such as performance requirements, environmental impact, and cost-effectiveness.
Summary Table:
Key Aspect | Details |
---|---|
Definition | A process to deposit thin films on substrates in a vacuum environment. |
Stages | Evaporation, Transportation, Reaction, Deposition. |
Advantages | Durability, Precision, Environmental Benefits, Aesthetic Appeal. |
Applications | Aerospace, Automotive, Electronics, Medical Devices. |
Comparison to Electroplating | Thinner, more uniform coatings with superior adhesion and fewer hazards. |
Materials Used | Metals (e.g., titanium), Ceramics (e.g., titanium nitride), Alloys. |
Customization | High flexibility to tailor coatings for specific applications. |
Discover how PVD coatings can enhance your product performance—contact our experts today!