An induction coil is a device that uses electromagnetic induction to transfer energy from an electrical current to a conductive material, typically metal, to achieve heating, melting, or other processes. It consists of a coil of conductive material, such as copper, which generates a magnetic field when an electrical current passes through it. This magnetic field induces eddy currents in the conductive material, leading to heating due to resistance. Induction coils are widely used in applications such as metal melting, surface heating, welding, and even in ignition systems for gasoline engines. Their efficiency and precision make them essential in industries like metallurgy, semiconductor manufacturing, and automotive engineering.
Key Points Explained:
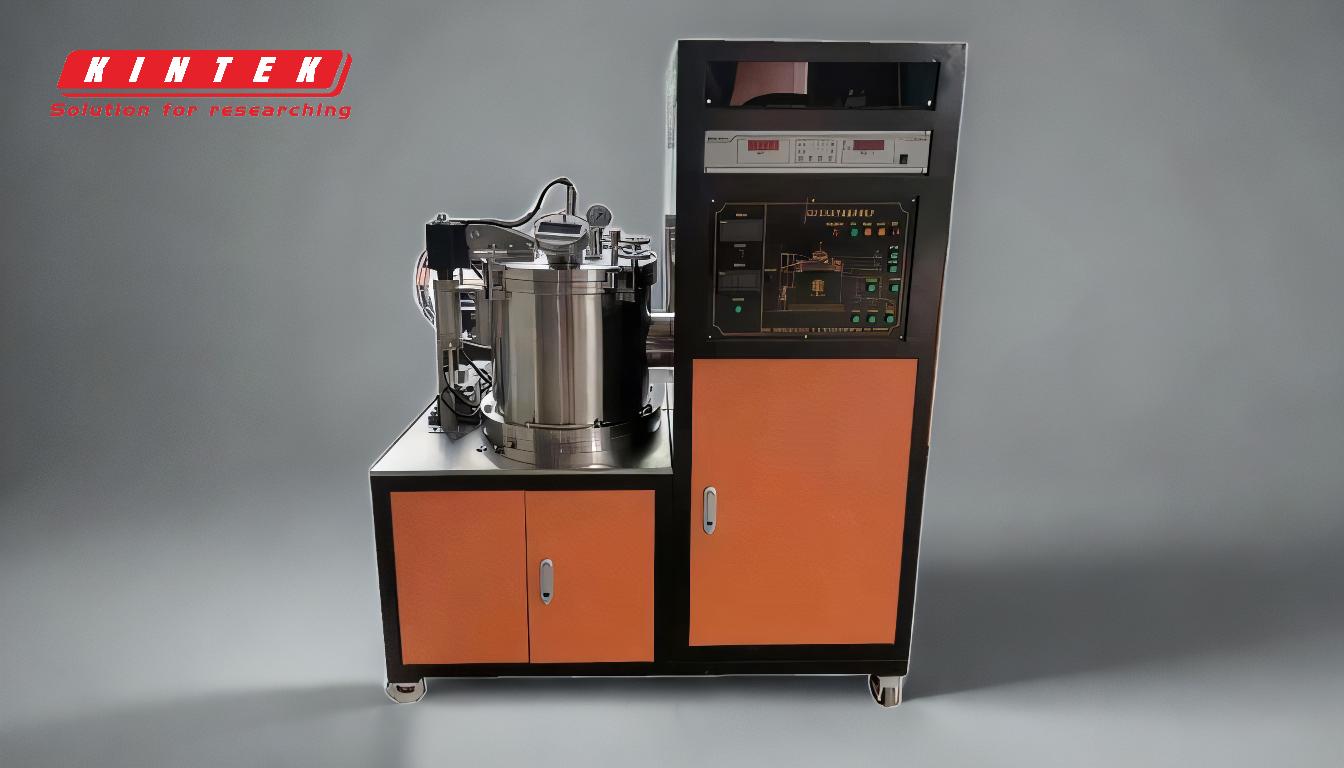
-
Basic Working Principle of an Induction Coil:
- An induction coil operates based on electromagnetic induction and self-induction.
- When an electrical current flows through the coil, it generates a magnetic field around it.
- This magnetic field induces eddy currents in any nearby conductive material, such as metal, causing it to heat up due to electrical resistance.
-
Key Components of an Induction Coil System:
- Conductive Coil: Typically made of copper, the coil carries the electrical current and generates the magnetic field.
- Crucible: In applications like induction furnaces, the crucible holds the material to be heated or melted. It is often lined with refractory material to withstand high temperatures.
- Power Supply: Provides the electrical current necessary to energize the coil and create the magnetic field.
-
Applications of Induction Coils:
- Metal Melting and Heating: Induction coils are used in induction furnaces to melt metals efficiently. The eddy currents generated by the coil heat the metal to its melting point without requiring direct contact.
- Surface Heating and Soldering: Induction heating is used for targeted heating applications, such as surface hardening, soldering, and brazing.
- Semiconductor Industry: Induction coils are used to heat silicon and other materials in semiconductor manufacturing processes.
- Automotive Ignition Systems: In gasoline engines, induction coils generate high-voltage sparks to ignite the fuel-air mixture in the combustion chamber.
- Plastic Injection Molding: Induction heating improves energy efficiency in plastic molding machines by providing precise and rapid heating.
- Tamper-Resistant Sealing: Induction coils are used to seal caps on bottles and pharmaceutical containers, ensuring tamper resistance.
-
Advantages of Induction Heating:
- Precision: Induction heating allows for precise control over the heating process, making it ideal for applications requiring specific temperatures.
- Efficiency: The process is highly efficient, as energy is directly transferred to the material being heated, minimizing heat loss.
- Cleanliness: Since there is no direct contact between the coil and the material, induction heating is a clean process, reducing contamination risks.
- Speed: Induction heating is rapid, enabling quick heating and cooling cycles, which is beneficial in industrial processes.
-
Factors Affecting Induction Coil Performance:
- Coil Design: The shape, size, and number of turns in the coil influence the strength and distribution of the magnetic field.
- Current Flow: The amount of electrical current passing through the coil determines the intensity of the magnetic field and the resulting heating effect.
- Material Properties: The conductivity and magnetic permeability of the material being heated affect how efficiently it absorbs energy from the magnetic field.
-
Specialized Uses of Induction Coils:
- Vacuum Furnaces: Induction coils are used in vacuum furnaces to produce specialized steel and alloys under controlled atmospheric conditions.
- Welding: Induction heating is employed for welding metals and sometimes plastics doped with ferromagnetic ceramics.
- Brazing: Induction coils are used to braze carbide tips to tool shafts, ensuring strong and durable bonds.
-
Induction Coils in Everyday Life:
- Induction Stoves: Induction cooktops use induction coils to heat cookware directly, offering faster and more energy-efficient cooking compared to traditional stoves.
- Cap Sealing: Induction coils are used in the food and pharmaceutical industries to create tamper-evident seals on containers.
In summary, an induction coil is a versatile and efficient tool that leverages electromagnetic induction to generate heat in conductive materials. Its applications span a wide range of industries, from metallurgy and manufacturing to automotive and household appliances. The design and operation of induction coils are tailored to meet specific heating requirements, making them indispensable in modern technology and industrial processes.
Summary Table:
Aspect | Details |
---|---|
Working Principle | Uses electromagnetic induction to generate heat in conductive materials. |
Key Components | Conductive coil, crucible, power supply. |
Applications | Metal melting, surface heating, automotive ignition, semiconductor heating. |
Advantages | Precision, efficiency, cleanliness, speed. |
Performance Factors | Coil design, current flow, material properties. |
Specialized Uses | Vacuum furnaces, welding, brazing, tamper-resistant sealing. |
Discover how induction coils can revolutionize your processes—contact us today for expert guidance!