The term "CIP" in the context of "Crip" is often misunderstood or misrepresented. It does not stand for "Crip" but is a separate acronym with its own meaning. CIP commonly refers to "Clean-in-Place," a method used in industrial and manufacturing settings to clean equipment without disassembling it. This process is crucial for maintaining hygiene and efficiency in industries like food processing, pharmaceuticals, and biotechnology. It is important to clarify that CIP is unrelated to the slang term "Crip," which refers to a well-known street gang. This distinction is vital to avoid confusion and ensure accurate communication.
Key Points Explained:
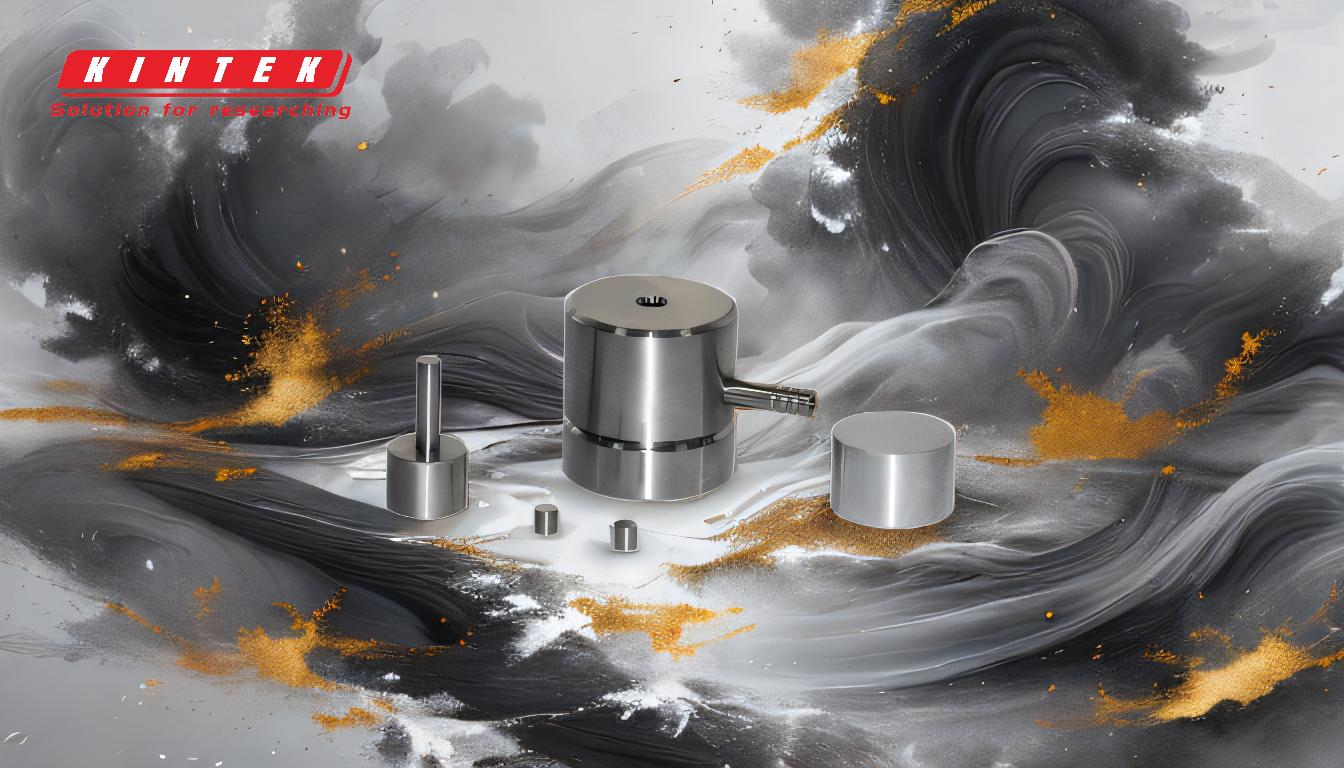
-
CIP Meaning and Context:
- CIP stands for "Clean-in-Place," a process used in industries to clean equipment internally without disassembly. This method is essential for maintaining hygiene, especially in food, pharmaceutical, and biotech industries.
- It involves circulating cleaning solutions through the equipment to remove residues, contaminants, and bacteria, ensuring compliance with health and safety standards.
-
CIP vs. Crip:
- CIP (Clean-in-Place) is a technical term used in industrial settings, while "Crip" refers to a street gang originating in Los Angeles. These two terms are entirely unrelated.
- Misunderstanding or conflating these terms can lead to confusion, especially in professional or technical discussions.
-
Importance of CIP in Industry:
- CIP systems are critical for maintaining operational efficiency and ensuring product quality. They reduce downtime by allowing equipment to be cleaned without disassembly, saving time and labor costs.
- They also help industries comply with strict regulatory standards for cleanliness and safety, particularly in sectors like food and pharmaceuticals.
-
How CIP Works:
- The CIP process typically involves several stages: pre-rinsing, cleaning with detergents or chemicals, rinsing, and sanitizing.
- Automated CIP systems are often used to ensure consistency and effectiveness, with parameters like temperature, flow rate, and chemical concentration carefully controlled.
-
Applications of CIP:
- CIP is widely used in industries such as dairy, brewing, beverage production, and pharmaceutical manufacturing.
- It is particularly important in industries where cross-contamination or bacterial growth could have severe consequences for product safety and consumer health.
-
Common Misconceptions:
- Due to the similarity in spelling, some people mistakenly associate CIP with "Crip." This confusion is more likely in casual or non-technical contexts.
- It is essential to clarify the distinction to avoid miscommunication, especially in professional or technical environments.
By understanding the correct meaning and applications of CIP, professionals can effectively implement and communicate about this critical cleaning process, ensuring both operational efficiency and compliance with industry standards.
Summary Table:
Aspect | Details |
---|---|
CIP Meaning | Clean-in-Place: A method to clean equipment without disassembly. |
Key Industries | Food processing, pharmaceuticals, biotechnology, and beverage production. |
Importance | Ensures hygiene, efficiency, and compliance with safety standards. |
Process Stages | Pre-rinsing, cleaning, rinsing, and sanitizing. |
Common Misconception | CIP is unrelated to the street gang 'Crip.' |
Need a CIP solution for your industry? Contact our experts today to learn more!