An inductance induction furnace, particularly a medium frequency induction furnace, operates by transforming electrical energy into heat through electromagnetic induction. This process involves converting three-phase power frequency alternating current into direct current, which is then adjusted and passed through a capacitor and an induction coil. The resulting high-density magnetic lines of force interact with the metal material within the coil, generating eddy currents. These eddy currents produce heat due to the resistance of the metal, effectively melting or heating the material. The use of an IGBT induction furnace enhances this process by providing precise control over the current and frequency, leading to efficient and controlled heating.
Key Points Explained:
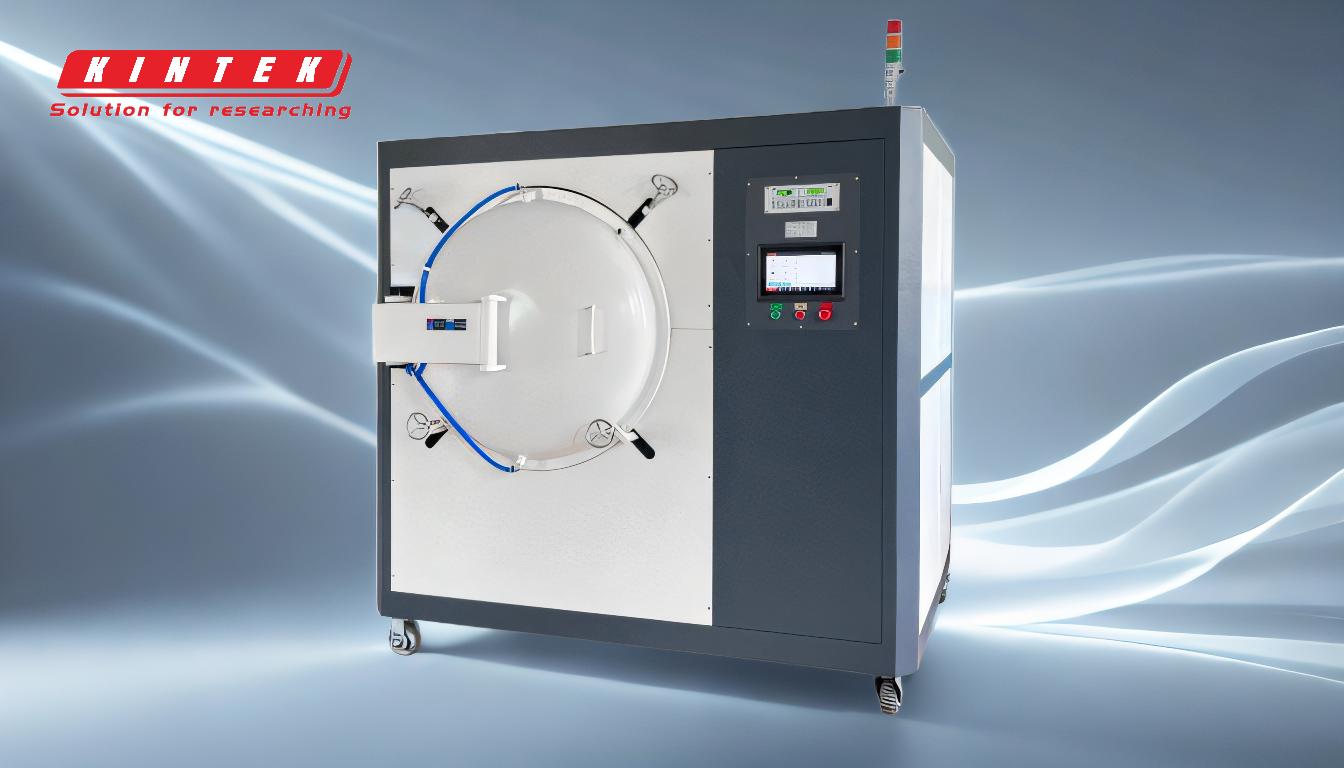
-
Conversion of Power Frequency Alternating Current to Direct Current:
- The initial step in the operation of an inductance induction furnace involves converting three-phase power frequency alternating current (AC) into direct current (DC). This conversion is crucial for creating a stable and adjustable current that can be finely controlled during the heating process.
-
Transformation into Adjustable Current:
- Once the AC is converted to DC, it is then transformed into an adjustable current. This adjustability is key to controlling the intensity of the magnetic field and, consequently, the amount of heat generated within the furnace.
-
Flow Through Capacitor and Induction Coil:
- The adjustable current flows through a capacitor and an induction coil. The capacitor helps in maintaining the stability of the current, while the induction coil is responsible for generating the magnetic field necessary for induction heating.
-
Generation of High-Density Magnetic Lines of Force:
- As the current passes through the induction coil, it generates high-density magnetic lines of force. These magnetic lines are essential for the induction heating process as they interact with the metal material placed within the coil.
-
Interaction with Metal Material:
- The high-density magnetic lines cut through the metal material inside the induction coil. This interaction induces eddy currents within the metal, which are loops of electrical current that flow in response to the changing magnetic field.
-
Production of Eddy Currents and Heat Generation:
- The eddy currents generated within the metal have properties similar to medium frequency current. As these currents flow through the metal, they encounter resistance, which results in the generation of heat. This heat is what ultimately melts or heats the metal material.
-
Role of IGBT Induction Furnace:
- The use of an IGBT induction furnace in this process is significant. IGBT (Insulated Gate Bipolar Transistor) technology allows for precise control over the current and frequency, leading to more efficient and controlled heating. This precision is particularly important in applications requiring specific temperature profiles or in processes where energy efficiency is critical.
In summary, an inductance induction furnace leverages the principles of electromagnetic induction to convert electrical energy into heat. The process involves several key steps, including the conversion of AC to DC, the generation of a magnetic field, and the induction of eddy currents in the metal material. The integration of IGBT technology enhances the efficiency and control of this process, making it a valuable tool in various industrial applications.
Summary Table:
Key Component | Function |
---|---|
Three-phase AC to DC Conversion | Converts power frequency AC into stable DC for adjustable current control. |
Capacitor and Induction Coil | Maintains current stability and generates a magnetic field for heating. |
High-Density Magnetic Lines | Interacts with metal to induce eddy currents, producing heat. |
IGBT Induction Furnace | Provides precise control over current and frequency for efficient heating. |
Want to optimize your heating process with advanced induction furnaces? Contact us today to learn more!