Nitrogen plays a critical role in furnace operations, particularly in heat treatment processes. It is used to create inert or reactive atmospheres, depending on the specific requirements of the material being processed. Nitrogen helps prevent oxidation and decarburization of metals, especially in high-temperature environments. It is commonly employed in annealing low-carbon steels and as a protective atmosphere for high-carbon steels. The gas is introduced into the furnace through flowmeters and expelled via exhaust systems, often monitored electronically to maintain precise composition levels. This ensures optimal conditions for material integrity and desired metallurgical properties.
Key Points Explained:
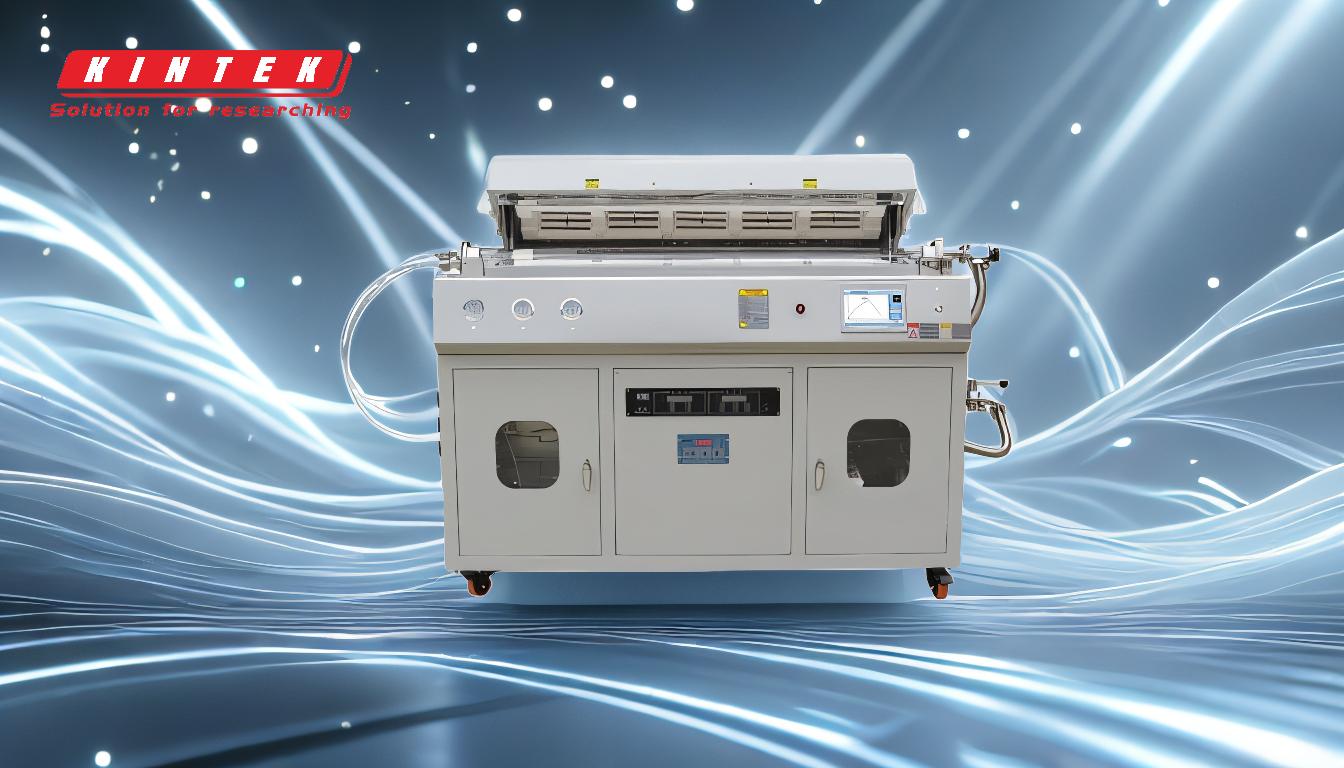
-
Role of Nitrogen in Furnace Atmospheres:
- Nitrogen is used to create inert or reactive atmospheres in furnaces, depending on the process requirements.
- Inert atmospheres prevent unwanted chemical reactions, such as oxidation, while reactive atmospheres can facilitate specific metallurgical transformations.
- This adaptability makes nitrogen suitable for a wide range of heat treatment processes.
-
Prevention of Oxidation:
- Nitrogen acts as a reducing gas in high-temperature furnaces, preventing the oxidation of materials.
- Oxidation can degrade the quality of metals, leading to surface defects and reduced mechanical properties.
- By blanketing the furnace chamber with nitrogen, the material is shielded from oxygen, ensuring a clean and oxidation-free surface.
-
Applications in Steel Processing:
- Nitrogen is particularly useful in annealing low-carbon steels, where it helps maintain the material's ductility and softness.
- For high-carbon steels, nitrogen serves as a protective atmosphere during heat treatment, preventing surface decarburization and maintaining the steel's hardness and strength.
-
Equipment and Monitoring:
- Nitrogen is introduced into the furnace through specialized equipment like nitrogen flowmeters, which regulate the gas flow.
- An exhaust system, often connected to a fume hood or external manifold piping, expels spent gas from the chamber.
- Electronic monitoring systems are frequently used to maintain precise nitrogen composition levels, ensuring consistent and optimal furnace conditions.
-
Benefits of Nitrogen Blanketing:
- Nitrogen blanketing prevents the oxidation of ferrous metals, preserving their structural integrity.
- It also helps decarburize the surface of steel products, which is essential for achieving specific mechanical properties.
- This process is critical in industries where material quality and consistency are paramount, such as automotive and aerospace manufacturing.
By understanding these key points, purchasers of furnace equipment and consumables can make informed decisions about the use of nitrogen in their processes, ensuring optimal results and material quality.
Summary Table:
Key Role of Nitrogen | Details |
---|---|
Atmosphere Creation | Creates inert or reactive atmospheres for heat treatment processes. |
Oxidation Prevention | Shields materials from oxygen, preventing surface defects and degradation. |
Steel Processing | Used in annealing low-carbon steels and protecting high-carbon steels. |
Equipment & Monitoring | Introduced via flowmeters, expelled via exhaust systems, and monitored electronically. |
Benefits | Preserves material integrity, decarburizes surfaces, and ensures consistent quality. |
Optimize your furnace processes with nitrogen—contact our experts today to learn more!