PVD stands for Physical Vapor Deposition, a process used to deposit thin-film coatings on surfaces in a vacuum environment. It involves vaporizing a solid material (the target) and depositing it onto a substrate, creating durable and resistant coatings. This technology is widely used in industries requiring high-performance coatings, such as electronics, optics, and automotive. The process includes stages like evaporation, transportation, reaction, and deposition, making it a precise and efficient method for creating thin films with strong covalent bonds.
Key Points Explained:
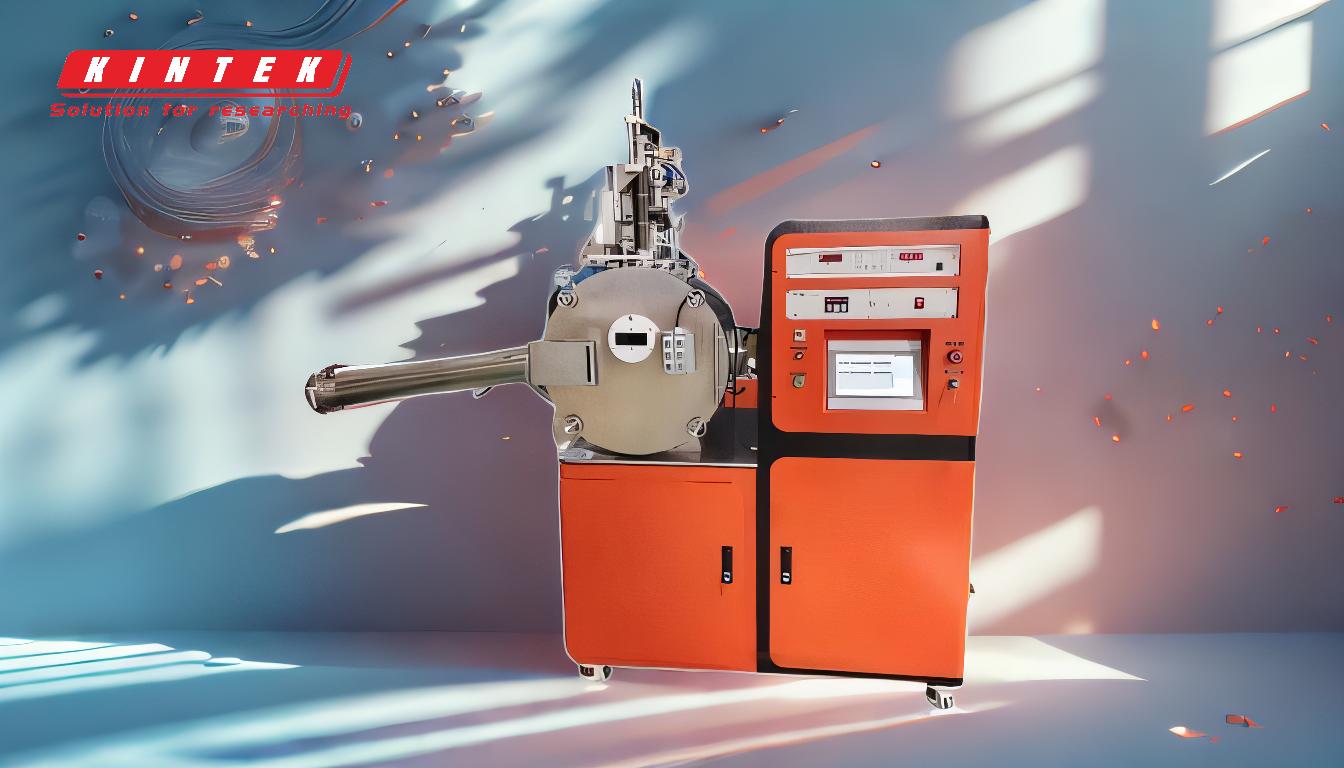
-
Definition of PVD:
- PVD stands for Physical Vapor Deposition. It is a thin-film coating process where a solid material is vaporized in a vacuum environment and then deposited onto a substrate to form a thin, durable coating.
-
Process Overview:
- The PVD process involves four main stages:
- Evaporation: The target material is vaporized using techniques like sputtering or thermal evaporation.
- Transportation: The vaporized material is transported through the vacuum chamber to the substrate.
- Reaction: In some cases, the vaporized material reacts with gases in the chamber to form compounds.
- Deposition: The material condenses on the substrate, forming a thin film.
- The PVD process involves four main stages:
-
Applications of PVD:
- PVD is used in various industries to create coatings with specific properties, such as:
- Electronics: For creating conductive and insulating layers.
- Optics: For anti-reflective and protective coatings on lenses.
- Automotive: For wear-resistant coatings on engine components.
- Medical Devices: For biocompatible coatings on implants.
- PVD is used in various industries to create coatings with specific properties, such as:
-
Advantages of PVD:
- Durability: PVD coatings are highly durable and resistant to wear, corrosion, and high temperatures.
- Precision: The process allows for precise control over the thickness and composition of the coatings.
- Versatility: PVD can deposit a wide range of materials, including metals, alloys, and ceramics.
- Environmental Friendliness: PVD is a clean process with minimal waste and no harmful chemicals.
-
Comparison to Other Coating Methods:
- PVD is often compared to electroplating, but it offers several advantages:
- Thinner Coatings: PVD can produce much thinner and more uniform coatings.
- Better Adhesion: PVD coatings generally have better adhesion to the substrate.
- Higher Purity: The vacuum environment ensures high-purity coatings.
- PVD is often compared to electroplating, but it offers several advantages:
-
Materials Used in PVD:
- Common materials used in PVD include:
- Metals: Such as titanium, chromium, and aluminum.
- Alloys: Such as titanium nitride (TiN) and chromium nitride (CrN).
- Ceramics: Such as aluminum oxide (Al2O3) and silicon carbide (SiC).
- Common materials used in PVD include:
-
Equipment and Consumables:
- PVD requires specialized equipment, including:
- Vacuum Chambers: To maintain the necessary vacuum environment.
- Targets: The source material to be vaporized.
- Substrates: The objects to be coated.
- Power Supplies: For generating the energy needed to vaporize the target material.
- Consumables include the target materials and any reactive gases used in the process.
- PVD requires specialized equipment, including:
-
Future Trends in PVD:
- The PVD industry is evolving with advancements in:
- Nanotechnology: For creating ultra-thin and highly functional coatings.
- Hybrid Processes: Combining PVD with other techniques like Chemical Vapor Deposition (CVD) for enhanced properties.
- Automation: Increasing the efficiency and consistency of the PVD process.
- The PVD industry is evolving with advancements in:
In summary, PVD is a versatile and precise method for depositing thin-film coatings with excellent durability and resistance. Its applications span multiple industries, and ongoing advancements continue to expand its capabilities and efficiency.
Summary Table:
Aspect | Details |
---|---|
Definition | PVD (Physical Vapor Deposition) deposits thin-film coatings in a vacuum. |
Process Stages | Evaporation, Transportation, Reaction, Deposition. |
Applications | Electronics, Optics, Automotive, Medical Devices. |
Advantages | Durability, Precision, Versatility, Environmental Friendliness. |
Materials Used | Metals (e.g., Titanium), Alloys (e.g., TiN), Ceramics (e.g., Al2O3). |
Future Trends | Nanotechnology, Hybrid Processes, Automation. |
Ready to explore how PVD can elevate your projects? Contact us today for expert guidance!