Sintering is a process that involves heating powdered materials to a temperature below their melting point, causing particles to bond and densify. This process decreases porosity, reduces grain size, and alters the distribution and shape of grain boundaries in the material's microstructure. These changes lead to enhanced mechanical properties such as strength, hardness, and durability, while also improving thermal and electrical conductivity. Sintering is a key step in manufacturing dense, high-performance components with consistent properties.
Key Points Explained:
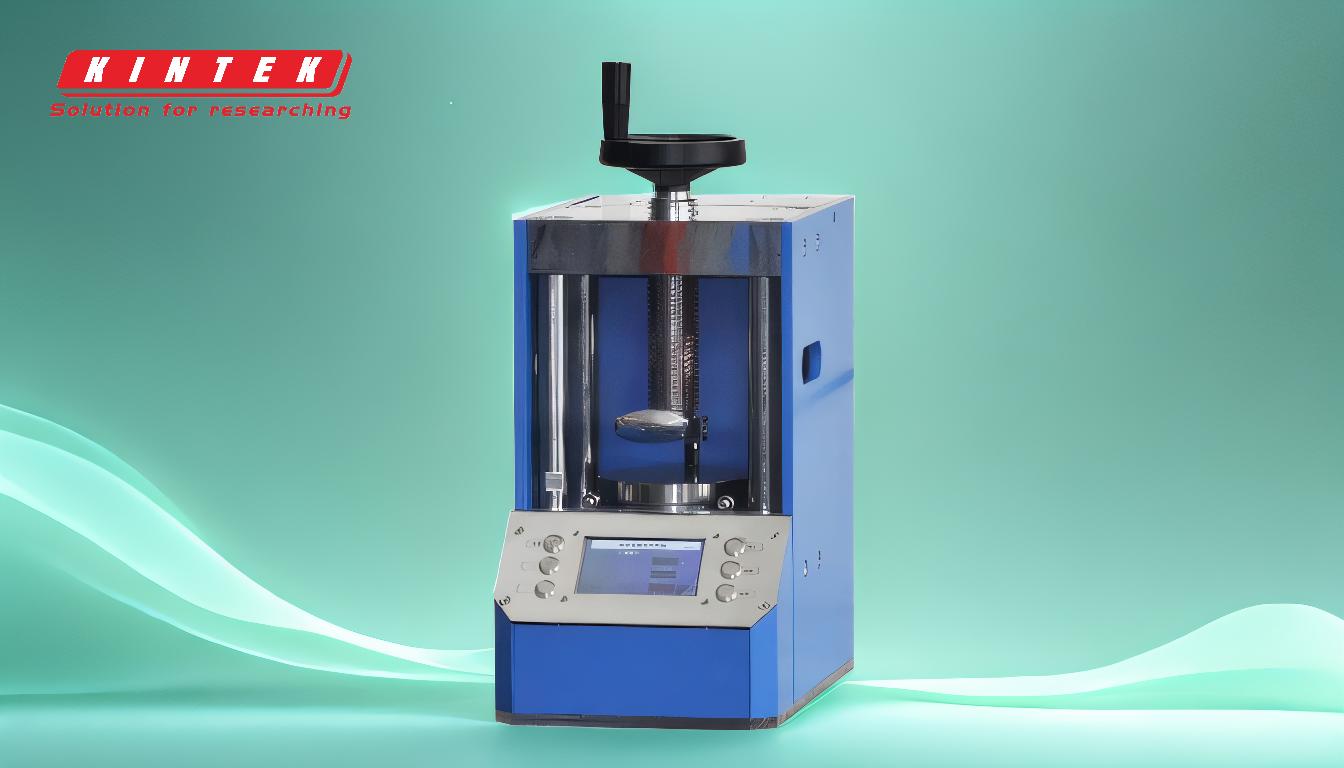
-
Decrease in Porosity:
- Sintering reduces the porosity of a material by causing particles to bond and densify. This minimizes the number and size of voids or pores within the material.
- Reduced porosity enhances the material's strength, durability, and resistance to wear and corrosion, as there are fewer weak points or defects in the structure.
- For example, in metal sintering, the process creates a denser surface, which is critical for applications requiring high mechanical integrity, such as bearings or heat pipes.
-
Reduction in Grain Size:
- During sintering, the controlled heating and diffusion mechanisms lead to a reduction in grain size within the material's microstructure.
- Smaller grain sizes generally improve mechanical properties, such as hardness and strength, because smaller grains create more grain boundaries, which act as barriers to dislocation movement.
- This is particularly important in ceramics and metals, where fine-grained structures are often desired for their superior performance characteristics.
-
Changes in Grain Boundary Shape and Distribution:
- Sintering alters the shape and distribution of grain boundaries, making them more uniform and cohesive.
- This contributes to the development of a dense and well-integrated microstructure, which enhances the material's overall mechanical integrity.
- For instance, in ceramic materials, uniform grain boundaries are critical for achieving high translucency and strength.
-
Impact on Material Properties:
- The changes in porosity, grain size, and grain boundaries during sintering directly influence the material's properties.
- Enhanced properties include improved thermal and electrical conductivity, increased material strength, and better wear resistance.
- These improvements make sintered materials suitable for a wide range of applications, from industrial components like bearings to consumer products like jewellery and shotgun shells.
-
Environmental and Manufacturing Benefits:
- Sintering requires less energy compared to melting the same material, making it an environmentally friendly manufacturing option.
- It also allows for greater control over the manufacturing process, resulting in more consistent and high-quality products.
- This is particularly advantageous for industries that require precise material properties, such as aerospace or medical device manufacturing.
By understanding these key points, purchasers of equipment and consumables can better appreciate the role of sintering in creating high-performance materials and components. The process not only improves material properties but also offers cost-effective and sustainable manufacturing solutions.
Summary Table:
Key Aspect | Impact |
---|---|
Decrease in Porosity | Enhances strength, durability, and resistance to wear and corrosion. |
Reduction in Grain Size | Improves hardness and strength by creating more grain boundaries. |
Grain Boundary Changes | Creates a dense, uniform microstructure for better mechanical integrity. |
Material Property Enhancements | Boosts thermal/electrical conductivity, strength, and wear resistance. |
Environmental Benefits | Energy-efficient process, ideal for sustainable and precise manufacturing. |
Ready to enhance your materials with sintering? Contact our experts today to learn more!