Sintering is a critical process in ceramic manufacturing that transforms powdered ceramic materials into dense, strong, and functional polycrystalline structures. By subjecting the ceramic powder to high temperatures, sintering facilitates material migration, grain boundary movement, and densification, resulting in reduced porosity, enhanced mechanical properties, and improved microstructural uniformity. This process enables the creation of intricate shapes, combines desirable material properties, and allows for cost-effective mass production of ceramics with tailored characteristics such as hardness, toughness, and thermal or electrical conductivity. The sintering process is essential for achieving the final strength, integrity, and performance of ceramic products.
Key Points Explained:
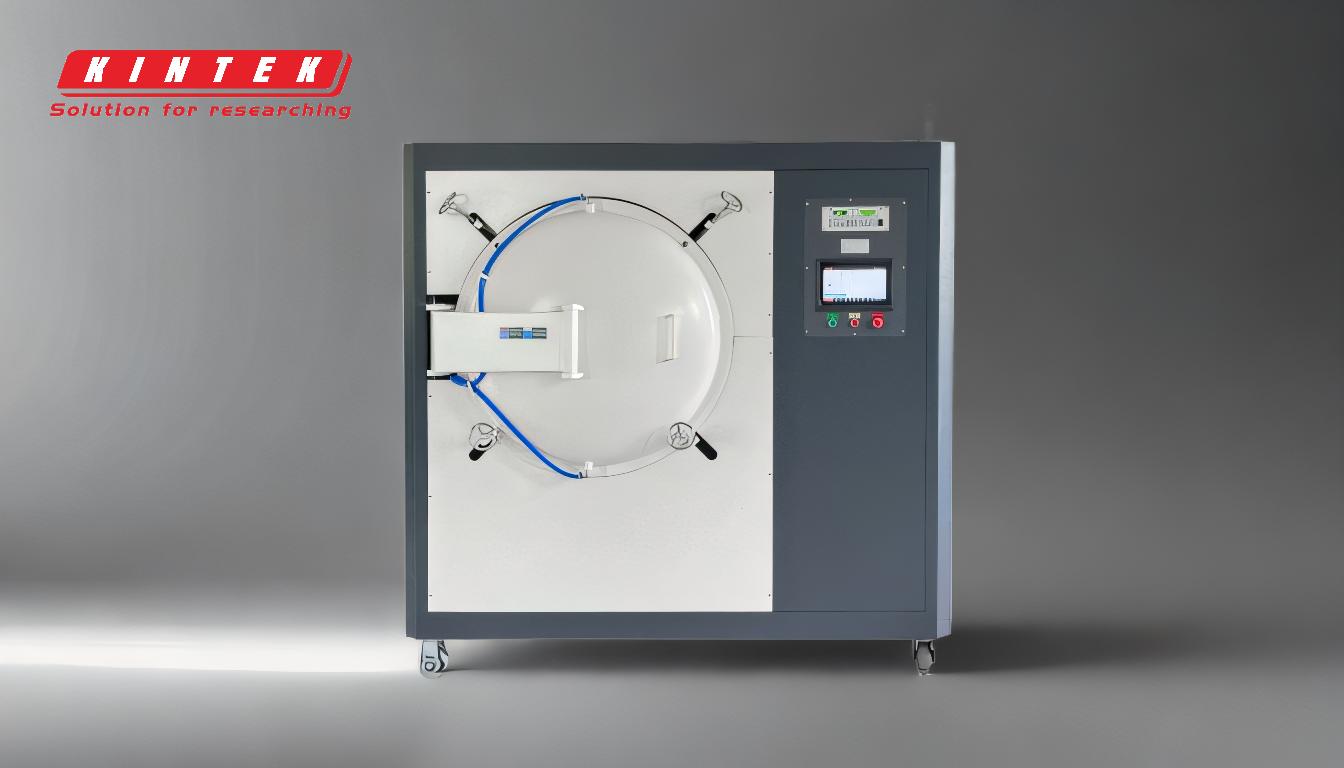
-
Transformation of Ceramic Powder into Dense Structures:
- Sintering converts loose ceramic powder into a solid, dense polycrystalline material.
- High temperatures cause powder particles to bond through diffusion and mass transfer, reducing porosity and increasing density.
- This results in a uniform microstructure with improved mechanical and physical properties.
-
Enhancement of Material Properties:
- Sintering improves key properties such as hardness, toughness, and abrasion resistance.
- It enhances electrical conductivity, thermal conductivity, and translucency, depending on the material and sintering conditions.
- The process allows for the combination of multiple material properties, such as toughness and wear resistance, in a single component.
-
Microstructural Changes:
- During sintering, grain boundaries move, and grains grow, leading to a reduction in voids and porosity.
- The process directly influences grain size, pore size, and grain boundary distribution, which in turn affect the material's strength and durability.
- A well-optimized sintering process ensures a controlled microstructure, which is critical for achieving desired material performance.
-
Creation of Complex Shapes and Geometries:
- Sintering enables the production of intricate shapes and geometries that are difficult to achieve with traditional manufacturing methods.
- It allows for the use of lower-cost tooling and supports rapid mass production while maintaining precision and repeatability.
-
Cost-Effective and Scalable Manufacturing:
- Sintering is a cost-effective method for producing ceramic components, especially for complex parts.
- It does not require the material to melt, making it suitable for materials with high melting points.
- The process is scalable and supports high-volume production without compromising quality.
-
Importance of Process Optimization:
- An optimized sintering process is crucial for achieving the desired physical and mechanical properties of ceramic products.
- Factors such as temperature, time, and atmosphere must be carefully controlled to ensure consistent results.
- Proper optimization minimizes defects and ensures the reliability and performance of the final product.
-
Applications in Advanced Ceramics:
- Sintering is widely used in the production of advanced ceramics for applications in electronics, aerospace, medical devices, and industrial tools.
- It is essential for creating components that require high strength, precision, and resistance to harsh environments.
By understanding the role of sintering in ceramic manufacturing, purchasers of equipment and consumables can make informed decisions about the materials and processes needed to achieve specific performance requirements in their applications.
Summary Table:
Key Aspect | Description |
---|---|
Transformation of Powder | Converts loose ceramic powder into dense, polycrystalline structures. |
Enhanced Material Properties | Improves hardness, toughness, thermal/electrical conductivity, and translucency. |
Microstructural Changes | Reduces porosity, optimizes grain size, and ensures uniform microstructure. |
Complex Shapes & Geometries | Enables intricate designs and cost-effective mass production. |
Scalable Manufacturing | Supports high-volume production without compromising quality. |
Process Optimization | Critical for achieving desired properties and minimizing defects. |
Applications | Used in electronics, aerospace, medical devices, and industrial tools. |
Ready to optimize your ceramic manufacturing process? Contact our experts today for tailored solutions!