Sintering is a critical process in metallurgy that transforms powdered metals into solid, durable components without melting them. By applying heat and pressure below the metal's melting point, sintering bonds metal particles, reduces porosity, and enhances the material's strength and structural integrity. This process is widely used in industries to produce high-performance parts like gears, bearings, and electrical contacts. Sintering is energy-efficient, environmentally friendly, and offers greater control over material properties compared to traditional manufacturing methods like casting or forging. It involves steps such as lubricant removal, oxide reduction, particle bonding, and controlled cooling, resulting in consistent and reliable end-use parts.
Key Points Explained:
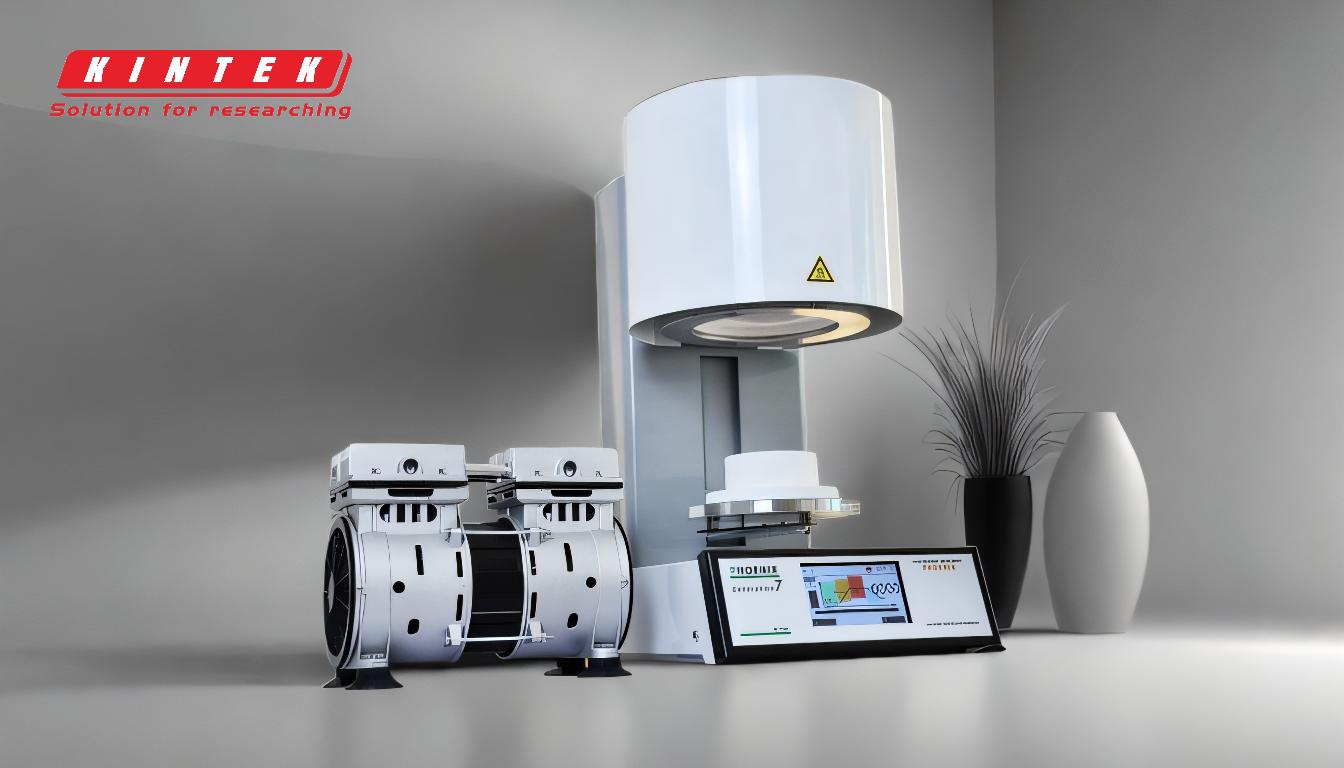
-
Definition and Purpose of Sintering:
- Sintering is a heat treatment process that compacts and bonds metal powders into a solid mass without reaching the metal's melting point.
- The primary purpose is to transform powdered materials into dense, strong, and durable components with improved mechanical properties.
-
Steps Involved in Sintering:
- Lubricant Removal: Lubricants used during powder compaction are removed to prevent contamination.
- Oxide Reduction: Oxide layers on metal particles are reduced to facilitate better bonding.
- Particle Bonding: Metal particles are bonded together through diffusion and grain growth under heat and pressure.
- Cooling: The sintered part is cooled in a controlled manner to achieve the desired mechanical properties and final dimensions.
-
Benefits of Sintering:
- Enhanced Strength and Durability: Sintering minimizes porosity, resulting in stronger and more durable components.
- Energy Efficiency: It requires less energy than melting metals, making it a cost-effective and environmentally friendly option.
- Greater Control: Sintering allows precise control over material properties, ensuring consistent and high-quality products.
- Versatility: It is suitable for producing complex shapes and components that are difficult to manufacture using traditional methods.
-
Applications of Sintering:
- Sintering is used to manufacture a wide range of industrial components, including gears, bearings, pulleys, rotors, sprockets, electrical contacts, cams, and armatures.
- Its flexibility and efficiency make it a preferred method in industries like automotive, aerospace, and electronics.
-
Comparison with Traditional Manufacturing Methods:
- Unlike casting, forging, or extrusion, sintering does not involve solid-liquid phase changes, which reduces energy consumption and material waste.
- It offers greater design flexibility and the ability to produce near-net-shape parts with minimal post-processing.
-
Environmental and Economic Advantages:
- Sintering is an eco-friendly process due to its lower energy requirements and reduced material waste.
- It is cost-effective for large-scale production, as it minimizes machining and finishing operations.
-
Controlled Atmosphere and Temperature:
- Sintering is performed in controlled atmosphere furnaces to prevent oxidation and ensure proper bonding.
- The temperature is maintained slightly below the metal's melting point to avoid liquefaction while achieving optimal particle bonding.
-
Final Properties of Sintered Parts:
- Sintered parts exhibit improved mechanical properties, such as increased hardness, wear resistance, and fatigue strength.
- The process allows for minor shrinkage, which is accounted for during the initial compaction stage, ensuring precise final dimensions.
By understanding these key points, equipment and consumable purchasers can appreciate the value of sintering in producing high-quality, cost-effective, and environmentally sustainable metal components.
Summary Table:
Aspect | Details |
---|---|
Definition | Heat treatment process bonding metal powders without melting. |
Steps | Lubricant removal, oxide reduction, particle bonding, controlled cooling. |
Benefits | Enhanced strength, energy efficiency, precise control, versatility. |
Applications | Gears, bearings, electrical contacts, automotive, aerospace, electronics. |
Advantages | Eco-friendly, cost-effective, minimal post-processing, near-net-shape parts. |
Final Properties | Increased hardness, wear resistance, fatigue strength, precise dimensions. |
Discover how sintering can revolutionize your manufacturing process—contact us today for expert guidance!