Sintering is a critical process for zirconia, transforming it into a dense, strong, and durable material. During sintering, zirconia undergoes significant physical and chemical changes, including the removal of porosity, evaporation of binders, and grain growth, which collectively enhance its mechanical properties. The process typically involves heating zirconia to high temperatures, allowing particles to bond and densify, followed by controlled cooling to achieve the desired microstructure. This results in a material with reduced porosity, increased density, and improved hardness, making it suitable for demanding applications such as dental crowns, industrial components, and advanced ceramics.
Key Points Explained:
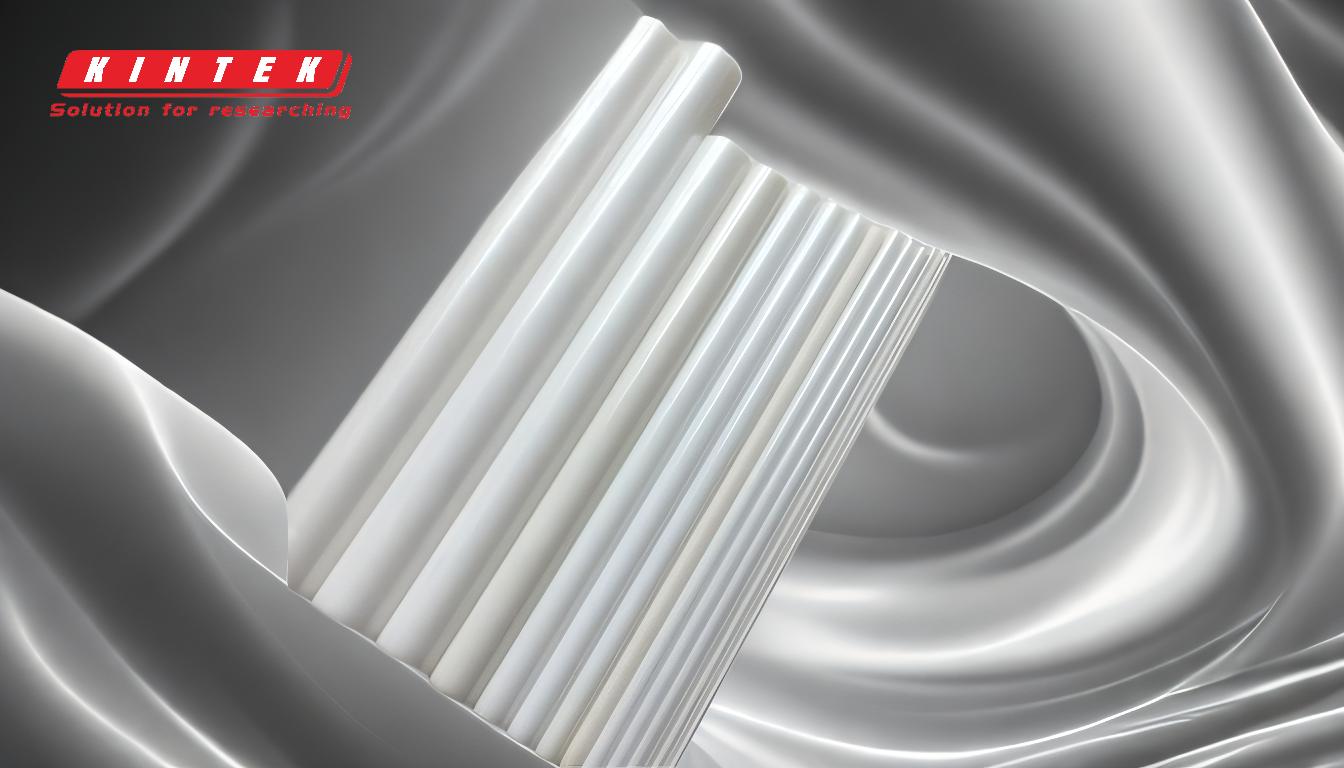
-
Reduction of Porosity and Increase in Density:
- Sintering significantly reduces the porosity of zirconia by eliminating voids between particles. This is achieved through the application of heat, which causes particles to bond and densify.
- The removal of porosity leads to a more homogeneous and dense material, which enhances its mechanical strength and durability.
-
Physical and Chemical Changes:
- During sintering, zirconia undergoes complex transformations, including the evaporation of water or organic binders, removal of adsorbed gases, and reduction of surface oxides.
- These changes facilitate material migration, recrystallization, and grain growth, which are essential for achieving the desired microstructure and properties.
-
Shrinkage and Dimensional Changes:
- Zirconia experiences significant shrinkage during sintering, often ranging from 20% to 30%. This shrinkage is a result of particle bonding and densification.
- Proper control of the sintering process is necessary to manage dimensional changes and ensure the final product meets precise specifications.
-
Heating, Sintering, and Cooling Phases:
- The sintering process typically involves three phases: heating, sintering, and cooling.
- Heating Phase: Heat is transferred to the surface of the zirconia and conducted to its core, preparing the material for sintering.
- Sintering Phase: At high temperatures, particles bond and densify, reducing porosity and increasing density.
- Cooling Phase: Controlled cooling ensures the material retains its desired microstructure and mechanical properties.
- The sintering process typically involves three phases: heating, sintering, and cooling.
-
Enhanced Mechanical Properties:
- Sintering improves zirconia's hardness, strength, and wear resistance, making it suitable for high-performance applications.
- The process also enhances the material's thermal and chemical stability, allowing it to withstand harsh environments.
-
Applications of Sintered Zirconia:
- Sintered zirconia is widely used in dental restorations, such as crowns and bridges, due to its biocompatibility and strength.
- It is also utilized in industrial applications, including cutting tools, bearings, and wear-resistant components, where durability and precision are critical.
By understanding the sintering process and its effects on zirconia, manufacturers and purchasers can make informed decisions about material selection and processing parameters to achieve optimal performance in their applications.
Summary Table:
Key Effects of Sintering on Zirconia | Details |
---|---|
Porosity Reduction | Eliminates voids, increasing density and strength. |
Physical & Chemical Changes | Removes binders, gases, and oxides; enables grain growth. |
Shrinkage | 20-30% shrinkage due to particle bonding and densification. |
Heating, Sintering, Cooling Phases | Controlled phases ensure optimal microstructure. |
Enhanced Properties | Improves hardness, strength, wear resistance, and stability. |
Applications | Used in dental crowns, industrial tools, and wear-resistant components. |
Learn how sintering can optimize zirconia for your applications—contact our experts today!