The term "VAR" in steel refers to Vacuum Arc Remelting, a specialized production process used to refine and improve the quality of steel. This method involves remelting steel under a vacuum atmosphere, which helps remove impurities, gases, and inclusions, resulting in a material with enhanced purity, homogeneity, and mechanical properties. VAR is particularly important for industries requiring high-performance steels, such as aerospace, medical, and energy sectors. The process ensures that the steel meets stringent quality standards, making it suitable for critical applications where reliability and durability are paramount.
Key Points Explained:
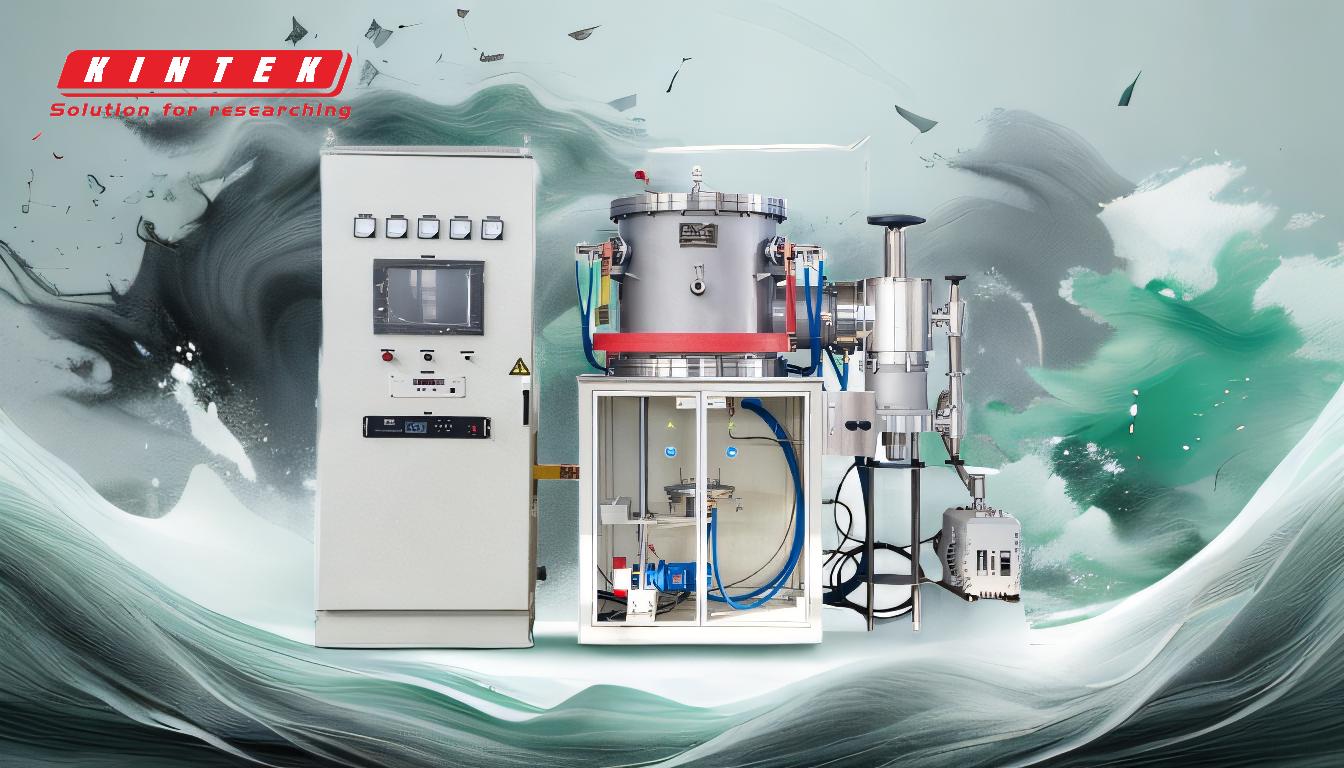
-
Definition of VAR (Vacuum Arc Remelting):
- VAR is a secondary melting process used to refine steel and other alloys.
- It involves remelting a consumable electrode under a vacuum environment.
- The vacuum atmosphere helps eliminate impurities, gases, and non-metallic inclusions.
-
Purpose of VAR:
- Improved Purity: The vacuum environment removes dissolved gases like hydrogen, oxygen, and nitrogen, which can weaken the steel.
- Enhanced Homogeneity: The process ensures a uniform distribution of alloying elements, reducing segregation and improving consistency.
- Superior Mechanical Properties: VAR-processed steels exhibit better strength, toughness, and fatigue resistance, making them ideal for demanding applications.
-
How the VAR Process Works:
- A consumable electrode made of the steel to be refined is placed in a vacuum chamber.
- An electric arc is struck between the electrode and a water-cooled copper mold, melting the electrode.
- The molten metal solidifies in the mold, forming a refined ingot with improved properties.
- The vacuum environment prevents contamination and ensures a clean remelting process.
-
Applications of VAR Steel:
- Aerospace: Used in turbine blades, engine components, and structural parts due to its high strength and reliability.
- Medical: Ideal for surgical instruments and implants because of its biocompatibility and corrosion resistance.
- Energy: Employed in nuclear reactors and power generation equipment for its ability to withstand extreme conditions.
-
Advantages of VAR Steel:
- High Purity: The absence of impurities ensures superior performance in critical applications.
- Consistency: The uniform microstructure reduces variability in mechanical properties.
- Durability: Enhanced resistance to fatigue, creep, and stress corrosion cracking.
-
Comparison with Other Remelting Processes:
- Electroslag Remelting (ESR): While ESR also improves steel quality, it does not use a vacuum, making it less effective at removing certain gases.
- Vacuum Induction Melting (VIM): VIM is another vacuum-based process, but it is typically used for smaller batches and different alloy types compared to VAR.
-
Considerations for Purchasers:
- Cost: VAR processing adds to the cost of steel due to the specialized equipment and energy requirements.
- Lead Time: The process is time-consuming, which may affect production schedules.
- Certification: Ensure the steel meets industry-specific standards and certifications for quality assurance.
By understanding the VAR process and its benefits, purchasers can make informed decisions when selecting materials for high-performance applications, ensuring they meet the required quality and reliability standards.
Summary Table:
Key Aspect | Details |
---|---|
Definition | Secondary melting process refining steel under a vacuum atmosphere. |
Purpose | Improves purity, homogeneity, and mechanical properties of steel. |
Process | Melts a consumable electrode in a vacuum chamber, producing refined ingots. |
Applications | Aerospace, medical, and energy sectors. |
Advantages | High purity, consistency, and durability. |
Comparison with ESR/VIM | More effective at removing gases than ESR; differs in scale from VIM. |
Considerations | Higher cost, longer lead time, and need for certifications. |
Ready to explore how VAR steel can meet your high-performance needs? Contact our experts today for more information!