Sintering is a critical process in materials science and manufacturing, where powdery materials are transformed into dense, solid bodies through the application of heat and pressure, typically below the material's melting point. This process involves a series of physical and chemical changes, including the removal of water, organic matter, and adsorbed gases, as well as stress relief, reduction of surface oxides, material migration, recrystallization, and grain growth. The diffusion of atoms across particle boundaries leads to the formation of neck connections between particles, eventually resulting in the elimination of small pores and the creation of a solid mass. Sintering is widely used in powder metallurgy, ceramic manufacturing, and other industries to produce hard, strong, and durable materials.
Key Points Explained:
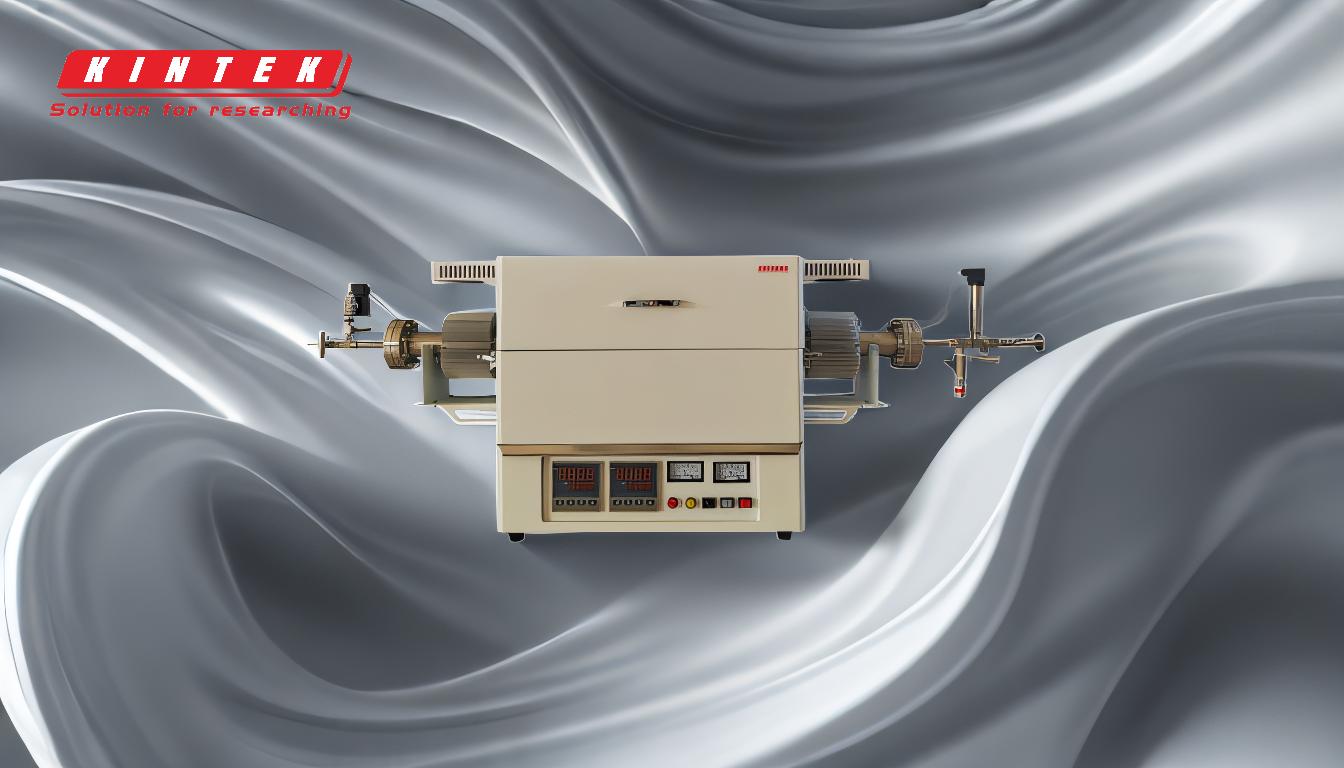
-
Removal of Volatile Components
- During sintering, water, organic matter, and adsorbed gases are evaporated or removed from the powdery material.
- This step is crucial for ensuring the purity and structural integrity of the final product.
- Example: In ceramic sintering, organic binders used during shaping are burned off.
-
Stress Relief and Reduction of Surface Oxides
- Internal stresses within the powder particles are relieved during sintering.
- Surface oxides on the particles are reduced, which enhances the bonding between particles.
- This step improves the mechanical properties of the sintered material.
-
Material Migration and Diffusion
- Atoms diffuse across the boundaries of the particles, driven by thermal energy.
- This diffusion leads to the formation of neck connections between adjacent particles.
- Over time, these necks grow, reducing porosity and increasing density.
-
Recrystallization and Grain Growth
- Recrystallization occurs as new, strain-free grains form within the material.
- Grain growth follows, where larger grains grow at the expense of smaller ones.
- These processes contribute to the material's final microstructure and mechanical properties.
-
Stages of Sintering
- Initial Stage: Formation of neck connections between particles.
- Intermediate Stage: Growth of necks and reduction of pore size.
- Final Stage: Elimination of small pores and densification of the material.
-
Applications and Materials
- Sintering is used for metals (e.g., tungsten, molybdenum), ceramics, and plastics.
- It is a key process in powder metallurgy for producing components like gears, bearings, and filters.
- In ceramics, sintering is used to create tiles, bricks, and advanced materials like alumina and zirconia.
-
Benefits of Sintering
- Produces materials with high strength, hardness, and durability.
- Enables the creation of complex shapes and near-net-shape components.
- Suitable for materials with high melting points that are difficult to process by other methods.
By understanding these key points, equipment and consumable purchasers can make informed decisions about the materials and processes required for their specific applications. Sintering offers a versatile and efficient method for transforming powders into high-performance materials, making it indispensable in modern manufacturing.
Summary Table:
Key Aspect | Description |
---|---|
Removal of Volatile Components | Water, organic matter, and gases are removed to ensure purity and integrity. |
Stress Relief & Oxide Reduction | Internal stresses are relieved, and surface oxides are reduced for better bonding. |
Material Migration & Diffusion | Atoms diffuse, forming neck connections between particles, reducing porosity. |
Recrystallization & Grain Growth | New grains form and grow, enhancing the material's microstructure. |
Stages of Sintering | Initial neck formation → Intermediate neck growth → Final densification. |
Applications | Used in powder metallurgy, ceramics, and plastics for gears, tiles, and more. |
Benefits | High strength, durability, and the ability to create complex shapes. |
Ready to optimize your sintering process? Contact our experts today for tailored solutions!