Sintering is a critical process in materials science and manufacturing, where powdery materials are transformed into dense, solid bodies through the application of heat and pressure, typically below the material's melting point. This process is widely used in industries such as powder metallurgy, ceramics, and plastics to produce components with enhanced strength, durability, and microstructure. During sintering, particles bond together as their density increases, leading to changes in grain size, pore size, and grain boundary distribution, which ultimately influence the material's mechanical and physical properties. The process can involve transient or permanent liquid phases, depending on the materials used, and is essential for creating high-performance materials with specific characteristics.
Key Points Explained:
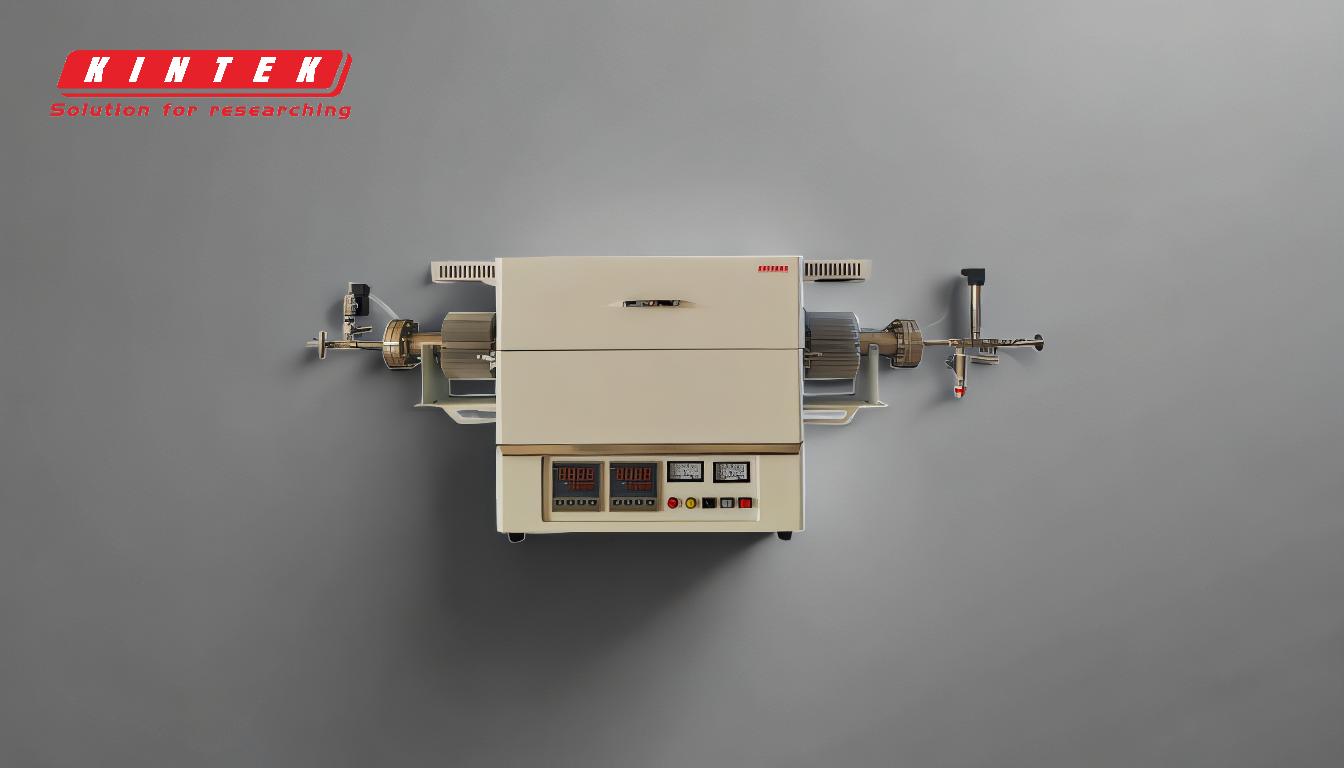
-
Definition and Purpose of Sintering:
- Sintering is a process that transforms powdery materials into dense, solid bodies by applying heat and pressure below the material's melting point.
- It is used to create materials with improved mechanical properties, such as strength, durability, and microstructure.
- Common applications include powder metallurgy, ceramic manufacturing, and the production of components from metals, ceramics, and plastics.
-
Mechanism of Sintering:
- During sintering, particles bond together through diffusion, where atoms migrate across particle boundaries, fusing them into a solid mass.
- The process involves the gradual increase in density as particles fuse, reducing porosity and improving material integrity.
- Sintering can occur through solid-state diffusion or involve a liquid phase, depending on the materials and desired outcomes.
-
Types of Sintering:
- Solid-State Sintering: Particles bond without melting, relying on atomic diffusion to fuse together. This is common in materials with high melting points, such as tungsten and molybdenum.
- Transient Liquid Phase Sintering: A temporary liquid phase forms, such as when copper powder melts and fuses with iron powder, enhancing particle bonding.
- Permanent Liquid Phase Sintering: A liquid phase persists throughout the process, flowing into pores and fissures to further bond the materials.
-
Microstructural Changes During Sintering:
- Sintering directly affects the material's microstructure, including grain size, pore size, and grain boundary distribution.
- These changes influence the material's mechanical properties, such as strength, hardness, and durability.
- For example, smaller grain sizes and reduced porosity typically result in stronger and more durable materials.
-
Applications of Sintering:
- Powder Metallurgy: Used to produce metal components with complex shapes and high precision, such as gears, bearings, and automotive parts.
- Ceramics: Sintering is essential for creating ceramic materials with high strength and thermal stability, used in applications like cutting tools and electronic components.
- Plastics and Composites: Sintering is used to produce high-performance plastic parts and composite materials with tailored properties.
-
Advantages of Sintering:
- Enables the production of complex shapes and near-net-shape components, reducing the need for additional machining.
- Improves material properties, such as strength, wear resistance, and thermal stability.
- Suitable for materials with extremely high melting points that cannot be processed using traditional melting techniques.
-
Challenges and Considerations:
- Controlling the sintering process is critical to achieving the desired material properties, as variations in temperature, pressure, and time can significantly impact the outcome.
- The choice of sintering method (solid-state, transient liquid phase, or permanent liquid phase) depends on the material and application requirements.
- Post-sintering treatments, such as heat treatment or surface finishing, may be necessary to achieve the final desired properties.
By understanding these key points, equipment and consumable purchasers can make informed decisions about the materials and processes required for their specific applications, ensuring optimal performance and cost-effectiveness.
Summary Table:
Aspect | Details |
---|---|
Definition | Process of transforming powdery materials into dense solids using heat and pressure. |
Mechanism | Particles bond through diffusion, increasing density and reducing porosity. |
Types | Solid-state, transient liquid phase, and permanent liquid phase sintering. |
Applications | Powder metallurgy, ceramics, plastics, and composite materials. |
Advantages | Produces complex shapes, improves strength, and handles high-melting materials. |
Challenges | Requires precise control of temperature, pressure, and time for optimal results. |
Discover how sintering can enhance your material performance—contact our experts today!