After calcination, the primary outcome is the removal of impurities from a metal ore, leaving behind a purified material that is often more chemically stable. This process involves heating the material to high temperatures in the absence or limited supply of air or oxygen, which drives off volatile substances such as water, carbon dioxide, or other gases. The resulting material is typically in a powdered or granular form and is ready for further processing, such as sintering, where small particles are fused together to form a solid structure. Calcination is a crucial step in metallurgy and materials science, as it prepares the raw material for subsequent treatments that enhance its physical and chemical properties.
Key Points Explained:
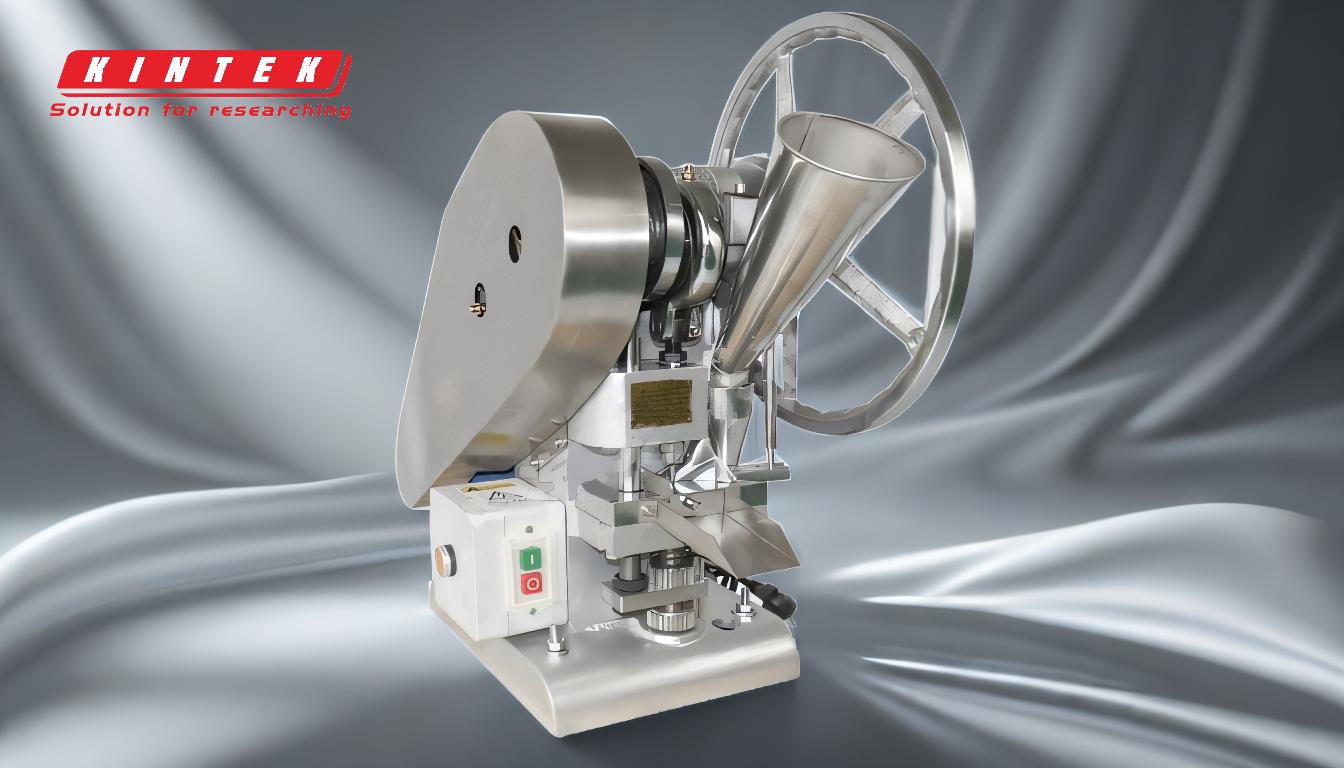
-
Definition and Purpose of Calcination:
- Calcination is a thermal treatment process applied to ores and other solid materials to bring about thermal decomposition, phase transition, or the removal of a volatile fraction.
- The primary purpose is to purify the material by driving off impurities such as water, carbon dioxide, or other gases, resulting in a more chemically stable product.
-
Process of Calcination:
- The material is heated to temperatures typically between 800°C to 1300°C, depending on the specific material and desired outcome.
- The process is usually carried out in the absence or limited supply of air or oxygen to prevent combustion or oxidation of the material.
- Common examples include the calcination of limestone (CaCO₃) to produce lime (CaO) and carbon dioxide (CO₂), or the calcination of bauxite to remove water and other impurities before aluminum extraction.
-
Outcome of Calcination:
- The removal of volatile substances results in a purified material, often in a powdered or granular form.
- The material becomes more chemically stable and is ready for further processing, such as sintering, where the particles are fused together to form a solid structure.
- Calcination can also lead to phase changes or the formation of new compounds, depending on the material and the conditions of the process.
-
Applications of Calcination:
- Metallurgy: Calcination is used to prepare metal ores for smelting by removing impurities and making the ore more reactive.
- Ceramics and Refractories: The process is used to produce materials like lime, magnesia, and alumina, which are essential in the production of ceramics and refractory materials.
- Chemical Industry: Calcination is employed to produce various chemicals, such as cement, where limestone is calcined to produce lime, a key ingredient in cement production.
-
Post-Calcination Processes:
- Sintering: After calcination, the purified material is often subjected to sintering, where the small particles are heated to a temperature below their melting point, causing them to bond together and form a solid mass. This process enhances the material's mechanical strength and density.
- Reduction: In some cases, the calcined material may undergo reduction, where it is further treated to remove oxygen and produce a pure metal. This is common in the production of metals like iron, where the calcined ore is reduced in a blast furnace.
-
Environmental and Economic Considerations:
- Calcination is an energy-intensive process, requiring significant amounts of heat, which can have environmental impacts if the energy source is not sustainable.
- The process can also generate by-products like carbon dioxide, which may need to be managed to minimize environmental impact.
- Economically, calcination is a critical step in the production of many materials, and optimizing the process can lead to cost savings and improved product quality.
In summary, calcination is a vital process in materials science and metallurgy, serving to purify and stabilize materials for further processing. The outcomes of calcination, such as the removal of impurities and the preparation of materials for sintering or reduction, are essential for the production of a wide range of industrial materials and products.
Summary Table:
Aspect | Details |
---|---|
Definition | Thermal treatment to remove volatile impurities and stabilize materials. |
Temperature Range | 800°C to 1300°C, depending on material and desired outcome. |
Outcome | Purified, powdered/granular material ready for sintering or reduction. |
Applications | Metallurgy, ceramics, refractories, and chemical production. |
Post-Processes | Sintering (particle bonding) and reduction (oxygen removal). |
Environmental Impact | Energy-intensive; may produce CO₂, requiring sustainable practices. |
Discover how calcination can optimize your material processing—contact us today for expert guidance!