Sintering in powder metallurgy is a critical heat treatment process that transforms compressed metal powders into strong, cohesive components. It involves heating the compacted powder to a temperature just below its melting point, allowing the particles to bond through diffusion and grain growth. This process enhances the material's strength, density, and structural integrity while maintaining its shape and properties. Sintering is widely used in industries like automotive and tool manufacturing to produce complex, high-performance parts such as gears, camshafts, and cutting tools.
Key Points Explained:
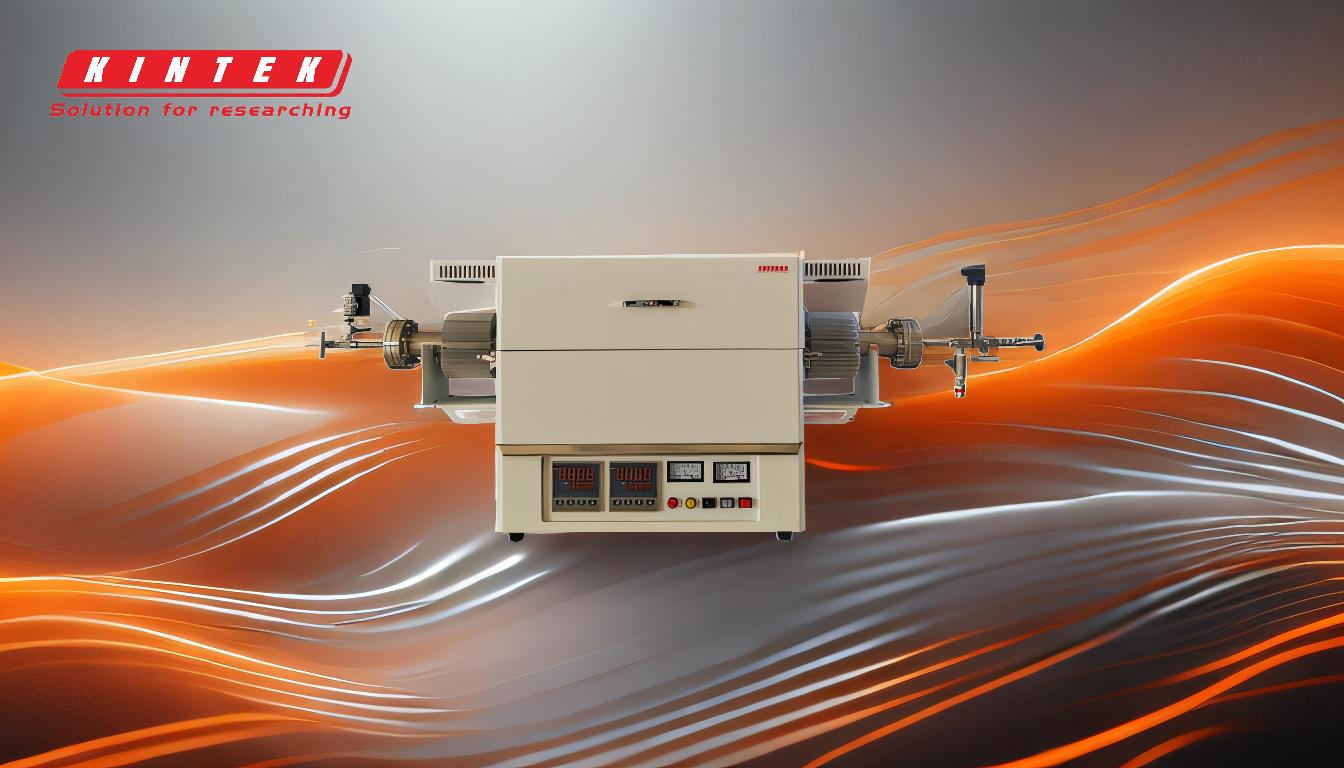
-
Definition and Purpose of Sintering:
- Sintering is a heat treatment process in powder metallurgy where compressed metal powders are heated to a temperature below their melting point.
- The primary goal is to bond the metal particles, creating a strong, cohesive structure while retaining the desired shape and properties of the material.
-
Temperature Control:
- The sintering temperature is carefully controlled to remain below the melting point of the primary metal or alloy.
- This prevents melting, ensuring the particles bond through solid-state diffusion rather than liquid-phase fusion.
-
Mechanism of Bonding:
- During sintering, metal particles undergo diffusion, where atoms migrate across particle boundaries.
- Grain growth occurs as smaller particles merge into larger ones, reducing porosity and increasing density.
- This bonding mechanism strengthens the material and improves its mechanical properties.
-
Stages of Sintering:
- Initial Stage: Particles begin to bond at contact points, forming necks between them.
- Intermediate Stage: Porosity decreases as the necks grow, and the material densifies.
- Final Stage: Grain growth dominates, and the material achieves its final density and strength.
-
Benefits of Sintering:
- Enhanced Strength and Hardness: The bonding of particles significantly improves the material's mechanical properties.
- Complex Shapes: Sintering allows for the production of intricate and precise components that are difficult to achieve with other methods.
- Material Efficiency: It minimizes waste by using metal powders efficiently.
-
Applications in Industry:
- Automotive: Used to manufacture gears, camshafts, valve seats, and other critical components.
- Tool Manufacturing: Produces cutting tools, drill bits, and other wear-resistant parts.
- Filters and Bearings: Creates porous structures for filters and self-lubricating bearings.
-
Comparison to Other Processes:
- Unlike melting, sintering preserves the material's original properties, such as grain structure and alloy composition.
- It is more cost-effective and energy-efficient than traditional casting or machining for producing complex parts.
-
Factors Influencing Sintering:
- Temperature and Time: Higher temperatures and longer sintering times generally improve bonding but must be balanced to avoid excessive grain growth.
- Powder Characteristics: Particle size, shape, and distribution affect the sintering process and final properties.
- Atmosphere: Controlled atmospheres (e.g., hydrogen, nitrogen, or vacuum) prevent oxidation and ensure consistent results.
-
Post-Sintering Processes:
- After sintering, parts may undergo additional treatments such as heat treatment, machining, or surface finishing to achieve the desired properties and tolerances.
-
Advantages for Manufacturers:
- Cost-Effective: Reduces material waste and energy consumption compared to traditional manufacturing methods.
- Versatility: Compatible with a wide range of metals and alloys, including iron, copper, titanium, and nickel-based alloys.
- Scalability: Suitable for both small-scale prototyping and large-scale production.
By understanding the sintering process, manufacturers can optimize their production methods to create high-quality, durable components tailored to specific applications. This process is a cornerstone of modern powder metallurgy, enabling the production of complex parts with superior performance and efficiency.
Summary Table:
Aspect | Details |
---|---|
Definition | Heat treatment process bonding metal powders below melting point. |
Key Mechanism | Solid-state diffusion and grain growth. |
Stages | Initial (neck formation), Intermediate (densification), Final (grain growth). |
Benefits | Enhanced strength, complex shapes, material efficiency. |
Applications | Automotive parts, cutting tools, filters, bearings. |
Factors Influencing | Temperature, time, powder characteristics, controlled atmosphere. |
Advantages | Cost-effective, versatile, scalable. |
Optimize your production with sintering—contact our experts today to learn more!