In a vacuum environment, heat transfer behaves differently compared to conventional environments due to the absence of air or other gases. In a vacuum, heat cannot be transferred via convection or conduction, as these mechanisms rely on the presence of a medium (like air or liquid). Instead, heat transfer in a vacuum occurs primarily through radiation. This principle is critical in applications like vacuum furnaces, where maintaining precise temperature control is essential. The heat generated in a vacuum furnace, such as a vacuum muffle furnace, is managed through radiative heat transfer and efficient insulation in the hot zone. The vacuum system ensures minimal heat loss to the surroundings, making it ideal for processes requiring high temperatures and controlled atmospheres.
Key Points Explained:
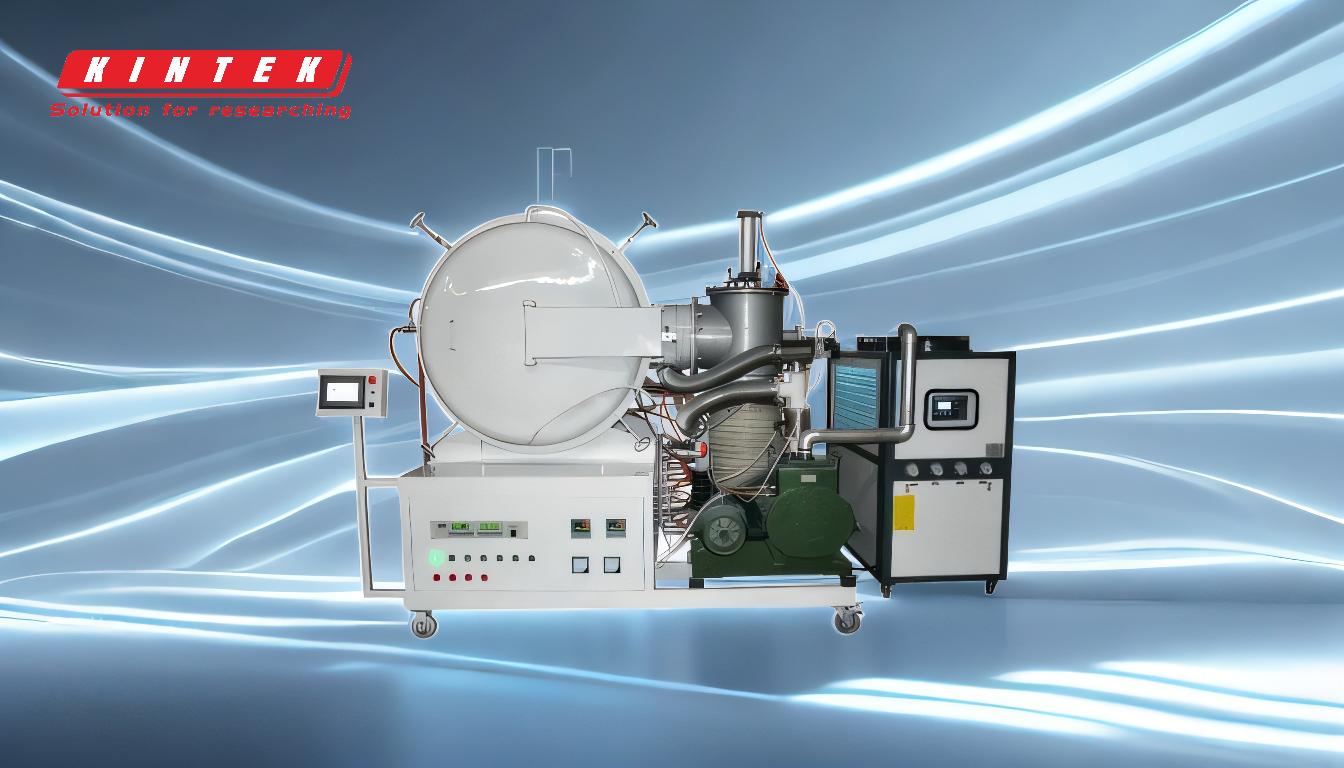
-
Heat Transfer Mechanisms in a Vacuum
- In a vacuum, heat transfer occurs primarily through radiation. Unlike convection or conduction, which require a medium (like air or liquid), radiation involves the emission of electromagnetic waves that can travel through a vacuum.
- This is particularly important in vacuum furnaces, where the absence of air prevents heat loss through convection, making the system more efficient for high-temperature applications.
-
Role of the Hot Zone in Vacuum Furnaces
- The hot zone is the area where heat is generated in a vacuum furnace. Engineers focus on improving the insulating characteristics of the hot zone to maximize heat retention and ensure uniform temperature distribution.
- Effective insulation reduces energy consumption and enhances the furnace's performance, making it suitable for processes like annealing, brazing, and sintering.
-
Importance of the Vacuum System
- The vacuum system, which includes components like vacuum valves, mechanical pumps, and diffusion pumps, is crucial for maintaining the necessary vacuum levels.
- A reliable vacuum system ensures that the furnace operates efficiently by preventing atmospheric contamination and minimizing heat loss. The highest achievable vacuum degree in such systems is typically around 7 × 10^-3 Pa.
-
Sealing and Gas Tightness
- Proper sealing is essential to maintain the vacuum and prevent atmospheric leakage. Issues like loose hinges, deformed buckles, or damaged seals can compromise the system's integrity.
- Regular maintenance and inspection of the sealing components are necessary to ensure the furnace operates at optimal efficiency.
-
Cold Traps and Gas Condensation
- Cold traps are used in vacuum systems to condense gases onto a cold surface, preventing them from reaching sensitive areas of the furnace.
- This process helps maintain the vacuum and protects the system from contamination, ensuring consistent performance.
-
Comparison with Other Furnace Types
- In contrast to vacuum furnaces, salt bath furnaces rely on convection for heat transfer, where molten salt comes into direct contact with the charge. This method allows for rapid heating due to the high heat capacity of molten salts.
- However, vacuum furnaces offer advantages in terms of precision and control, especially for processes requiring contamination-free environments.
By understanding these key points, equipment and consumable purchasers can make informed decisions about the suitability of vacuum furnaces for their specific applications. The unique heat transfer mechanisms and the importance of maintaining a reliable vacuum system make vacuum furnaces, including vacuum muffle furnaces, indispensable for high-temperature, controlled-environment processes.
Summary Table:
Key Aspect | Description |
---|---|
Heat Transfer Mechanism | Heat in a vacuum is transferred via radiation, as convection and conduction are absent. |
Hot Zone Role | The hot zone ensures heat retention and uniform temperature distribution. |
Vacuum System Importance | Maintains vacuum levels, prevents contamination, and minimizes heat loss. |
Sealing & Gas Tightness | Proper sealing prevents atmospheric leakage and ensures system integrity. |
Cold Traps | Condense gases to maintain vacuum and protect the system from contamination. |
Comparison with Other Furnaces | Vacuum furnaces offer precision and control, unlike salt bath furnaces. |
Ready to optimize your high-temperature processes? Contact us today to learn more about vacuum furnaces!