During pyrolysis, the feedstock undergoes a thermochemical decomposition process when heated to high temperatures (typically 300-900°C) in the absence of oxygen. This process breaks down the organic material into three primary products: gases (syngas), liquids (bio-oil), and solids (bio-char). The composition of these products depends on the type of feedstock and the specific conditions of the pyrolysis process, such as temperature and heating rate. Pyrolysis is widely used to convert biomass, plastics, and tires into valuable outputs like fuels, chemicals, and carbon-rich materials, contributing to waste reduction and resource recovery. The process is energy-intensive and requires precise control to optimize product yields and quality.
Key Points Explained:
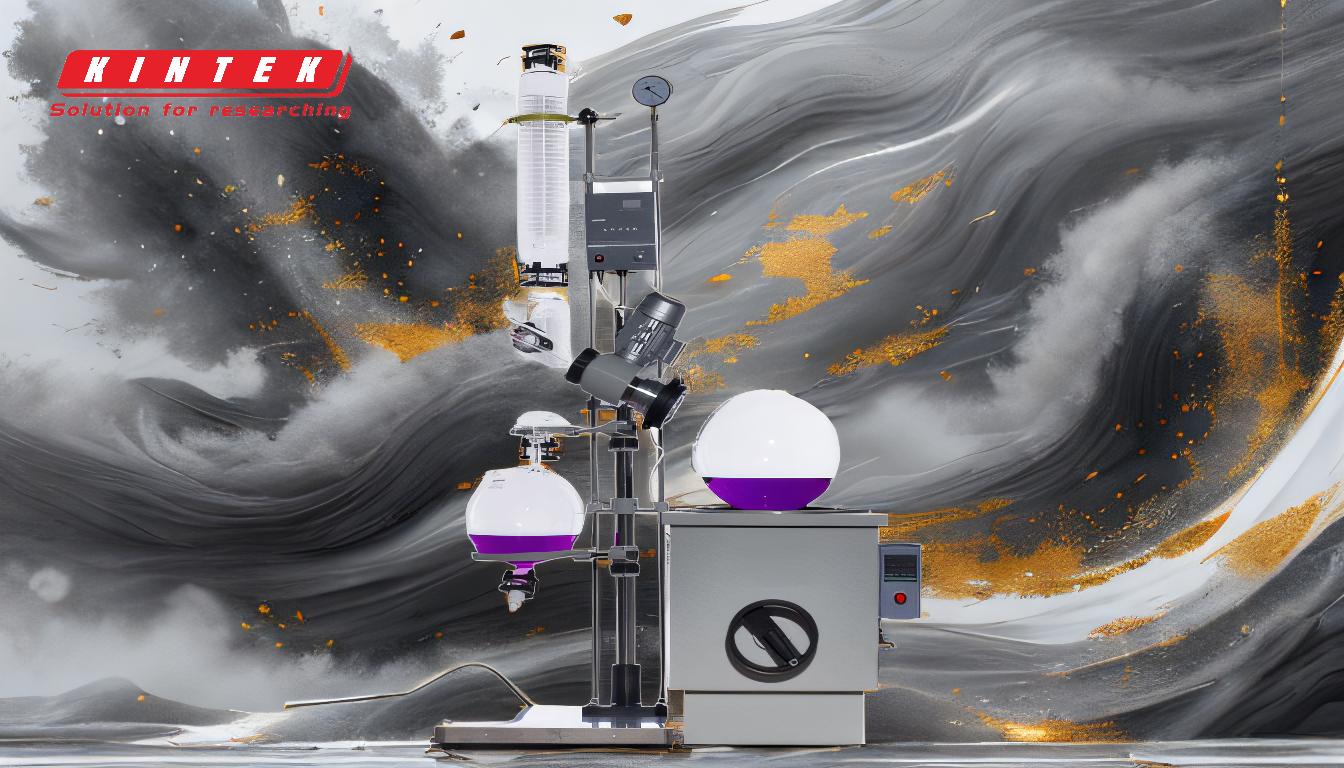
-
Thermochemical Decomposition in the Absence of Oxygen:
- Pyrolysis is a process where organic materials are heated to high temperatures (300-900°C) in an oxygen-free environment.
- The absence of oxygen prevents combustion, allowing the material to decompose into smaller molecules rather than burning completely.
- This decomposition is driven by the breaking of chemical bonds in the feedstock due to thermal energy.
-
Primary Products of Pyrolysis:
-
Gases (Syngas):
- The gaseous products include hydrogen (H₂), carbon monoxide (CO), methane (CH₄), and other light hydrocarbons.
- These gases are collectively referred to as syngas and can be used as a fuel or as a feedstock for chemical synthesis.
-
Liquids (Bio-oil):
- Bio-oil is a complex mixture of water and volatile organic compounds, including alcohols, acids, and phenols.
- It has potential applications as a renewable fuel or as a source of chemicals.
-
Solids (Bio-char):
- Bio-char is a carbon-rich solid residue that remains after pyrolysis.
- It can be used as a soil amendment, for carbon sequestration, or as a precursor for activated carbon production.
-
Gases (Syngas):
-
Dependence on Feedstock and Process Conditions:
- The type of feedstock (e.g., biomass, plastics, tires) significantly influences the composition and yield of pyrolysis products.
- Process conditions, such as temperature, heating rate, and residence time, also play a crucial role in determining the distribution of gases, liquids, and solids.
- For example, higher temperatures tend to favor gas production, while lower temperatures may yield more bio-oil.
-
Applications of Pyrolysis Products:
- Syngas: Can be used for electricity generation, heating, or as a raw material for producing synthetic fuels and chemicals.
- Bio-oil: Can be refined into transportation fuels or used directly in industrial boilers.
- Bio-char: Used in agriculture to improve soil health, as a carbon sink to mitigate climate change, or in filtration systems.
-
Energy Intensity and Process Control:
- Pyrolysis is an energy-intensive process, requiring significant heat input to achieve the necessary temperatures.
- Precise control of process parameters is essential to optimize product yields and ensure the quality of the outputs.
- Advanced techniques, such as microwave-assisted pyrolysis, offer more efficient heating and better control over the process.
-
Microwave-Assisted Pyrolysis:
- In this method, the feedstock is heated using microwaves, which provides uniform and rapid heating.
- The process involves purging the reactor with inert gas to prevent oxygen from entering, ensuring an oxygen-free environment.
- The volatile components are separated into gases and liquids through condensation, enhancing the efficiency of product recovery.
By understanding these key points, purchasers of pyrolysis equipment and consumables can make informed decisions about the types of feedstock and process conditions that will yield the desired products for their specific applications.
Summary Table:
Key Aspect | Details |
---|---|
Process | Thermochemical decomposition at 300-900°C in the absence of oxygen |
Primary Products | Gases (syngas), liquids (bio-oil), solids (bio-char) |
Feedstock Influence | Biomass, plastics, tires affect product composition and yield |
Process Conditions | Temperature, heating rate, and residence time determine product distribution |
Applications | Syngas for energy, bio-oil for fuels, bio-char for soil and filtration |
Energy Intensity | High heat input required; precise control optimizes yields and quality |
Advanced Techniques | Microwave-assisted pyrolysis for efficient and uniform heating |
Ready to optimize your pyrolysis process? Contact our experts today for tailored solutions!