Injection molding is a versatile manufacturing process widely used across multiple industries due to its ability to produce high-volume, precision plastic parts efficiently. Industries such as construction, food and beverage, consumer goods, and aerospace heavily rely on injection molding for creating durable, complex, and cost-effective components. This method is particularly valued for its scalability, consistency, and ability to meet stringent industry standards, making it a cornerstone of modern manufacturing.
Key Points Explained:
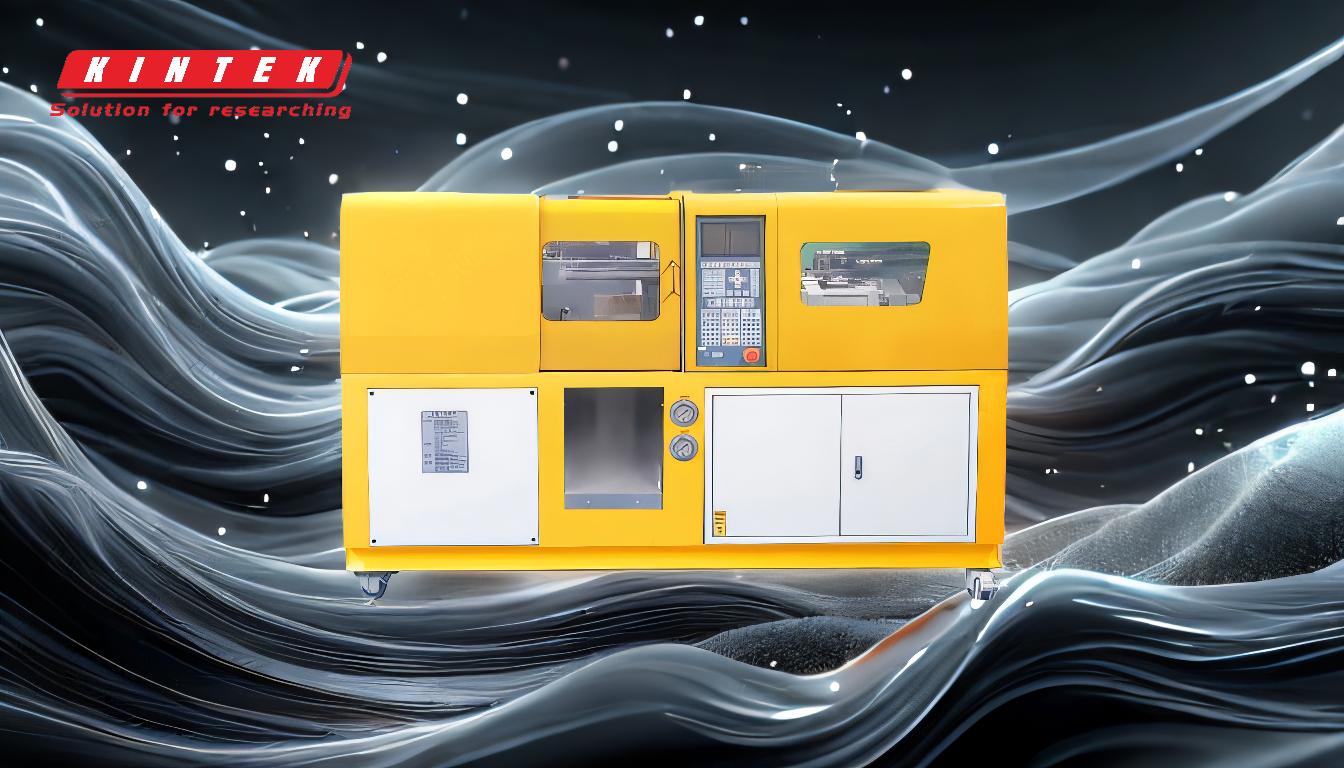
-
Construction Industry:
- Injection molding is used to produce a wide range of components, including pipes, fittings, insulation materials, and structural elements.
- The process allows for the creation of durable and weather-resistant parts, which are essential for construction applications.
- Examples include PVC pipes, window frames, and connectors for plumbing systems.
-
Food and Beverage Industry:
- Injection molding is critical for manufacturing food-safe containers, packaging, and utensils.
- The process ensures compliance with health and safety regulations, producing items like bottle caps, trays, and disposable cutlery.
- Materials used are often FDA-approved plastics that resist contamination and are easy to clean.
-
Consumer Goods:
- Injection molding is widely used to produce everyday items such as toys, household appliances, and electronics casings.
- The process enables mass production of intricate designs with consistent quality, making it ideal for consumer products.
- Examples include smartphone cases, kitchen utensils, and children's toys.
-
Aerospace Industry:
- Injection molding is employed to create lightweight, high-strength components for aircraft and spacecraft.
- The process meets the stringent requirements for precision, durability, and performance in aerospace applications.
- Examples include interior panels, brackets, and housings for electronic systems.
-
Advantages of Injection Molding Across Industries:
- Scalability: Suitable for both small and large production runs.
- Precision: Capable of producing complex geometries with tight tolerances.
- Cost-Effectiveness: Reduces per-unit costs for high-volume production.
- Material Versatility: Compatible with a wide range of thermoplastics and composite materials.
-
Emerging Applications:
- Injection molding is increasingly being used in the medical industry for producing sterile, disposable devices and components.
- The automotive industry leverages it for lightweight parts that improve fuel efficiency.
- Renewable energy sectors use injection-molded components for wind turbines and solar panels.
By understanding the diverse applications of injection molding, purchasers can better evaluate its suitability for their specific industry needs, ensuring optimal material selection, design, and production efficiency.
Summary Table:
Industry | Applications | Examples |
---|---|---|
Construction | Pipes, fittings, insulation, structural elements | PVC pipes, window frames, plumbing parts |
Food and Beverage | Food-safe containers, packaging, utensils | Bottle caps, trays, disposable cutlery |
Consumer Goods | Toys, household appliances, electronics casings | Smartphone cases, kitchen utensils, toys |
Aerospace | Lightweight, high-strength components for aircraft and spacecraft | Interior panels, brackets, electronic housings |
Advantages | Scalability, precision, cost-effectiveness, material versatility | |
Emerging Applications | Medical devices, automotive parts, renewable energy components | Sterile devices, lightweight car parts, wind turbine components |
Ready to leverage injection molding for your industry? Contact us today to learn more!