A 1800 degrees Celsius furnace is a specialized high-temperature furnace designed to operate at extreme temperatures, making it suitable for advanced industrial and laboratory applications. These furnaces are used in processes such as sintering, annealing, heat treatment, and material synthesis, particularly for materials like ceramics, metals, and advanced composites. They are equipped with features like advanced insulation, precise temperature control, and durable heating elements (e.g., SiC rods) to ensure uniform heating and efficient operation. Such furnaces are essential in industries like ceramics, metallurgy, electronics, and research institutions, where high-temperature processing is critical for material development and testing.
Key Points Explained:
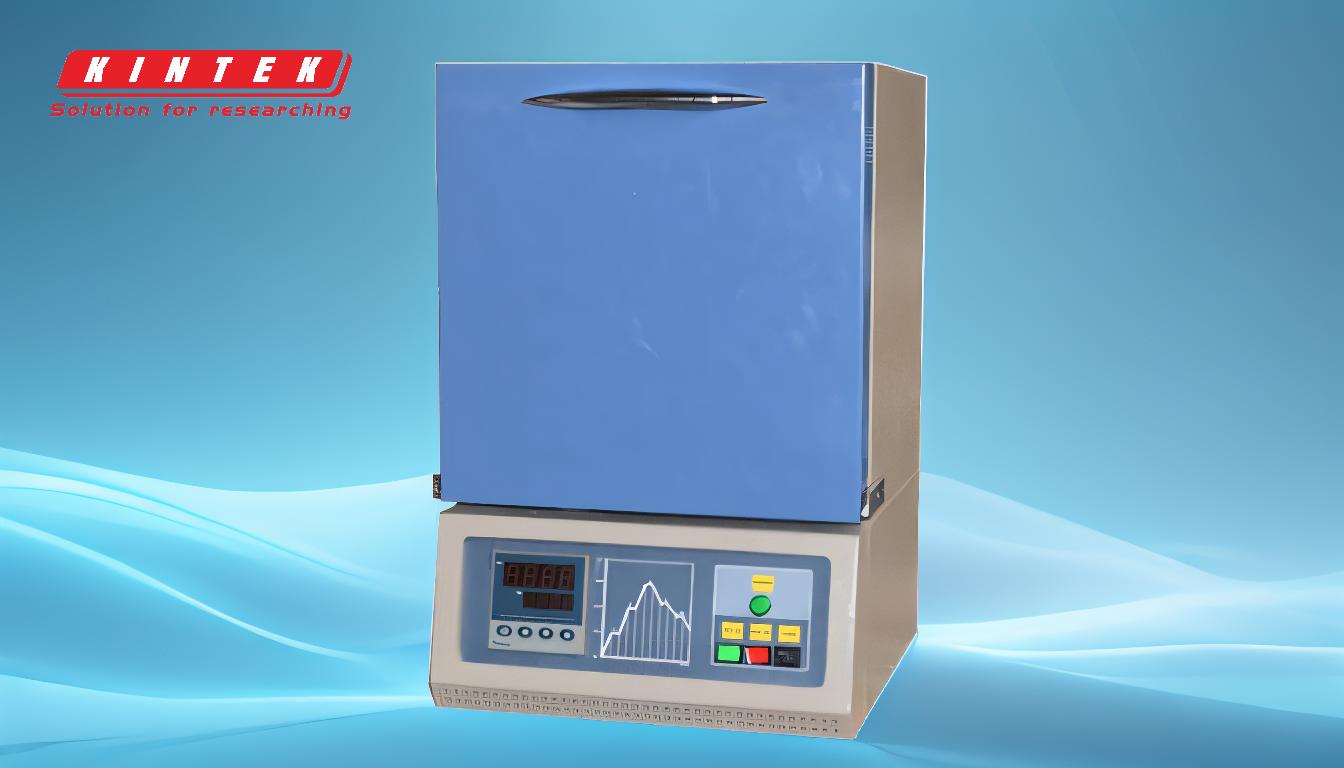
-
Definition and Purpose of a 1800°C Furnace:
- A 1800°C furnace is a high-temperature furnace capable of reaching and maintaining temperatures up to 1800 degrees Celsius. It is designed for applications that require extreme heat, such as sintering, annealing, and heat treatment of advanced materials like ceramics, metals, and composites.
-
Key Design Features:
- Heating Elements: Vertically mounted SiC (silicon carbide) rods are commonly used for uniform heating. These rods are durable and capable of withstanding extreme temperatures.
- Insulation: Multi-layered insulation and lightweight refractory brick lining ensure minimal heat loss and energy efficiency.
- Ventilation: Dual-shell housing and motor-driven exhaust systems provide better ventilation and temperature control.
- Door Design: Swing doors with hinges allow for easy access and loading of materials.
-
Applications:
- Industrial Uses: These furnaces are used in industries such as ceramics, metallurgy, electronics, and glass manufacturing for processes like powder roasting, sintering, and high-temperature experiments.
- Research and Development: Universities and research institutes use these furnaces for material synthesis, high-temperature testing, and advanced material processing.
- Specialized Processes: They are also used for diamond cutting blade heating, organic curing sintering, and flue gas treatment.
-
Operational Requirements:
- Temperature Control: Precise temperature control is critical for maintaining the desired thermal environment. Programmable controllers are often used to automate and monitor the heating process.
- Atmosphere Control: For processes requiring specific atmospheres (e.g., hydrogen or vacuum), specialized furnaces like cold wall furnaces are used to prevent contamination and ensure safety.
-
Advantages:
- High-Temperature Capability: The ability to reach 1800°C makes these furnaces suitable for advanced material processing.
- Uniform Heating: Advanced heating elements and insulation ensure consistent temperature distribution.
- Versatility: These furnaces can handle a wide range of materials and processes, making them indispensable in both industrial and research settings.
-
Challenges:
- Material Durability: Components like heating elements and insulation must withstand extreme temperatures, requiring high-quality materials and regular maintenance.
- Energy Consumption: Operating at such high temperatures can be energy-intensive, necessitating efficient design and insulation.
-
Special Considerations for 1800°C Operations:
- Cold Wall Furnaces: For processes requiring hydrogen or other reactive gases at temperatures above 1800°C, cold wall furnaces are preferred to prevent contamination and ensure safety.
- Safety Measures: Proper ventilation, gas handling, and temperature monitoring are essential to prevent accidents and ensure consistent performance.
In summary, a 1800°C furnace is a highly specialized piece of equipment designed for extreme high-temperature applications. Its advanced design, precise control systems, and versatility make it a critical tool in industries and research fields where material processing at extreme temperatures is required.
Summary Table:
Aspect | Details |
---|---|
Temperature Range | Up to 1800°C, ideal for extreme heat applications. |
Heating Elements | SiC rods for uniform heating and durability. |
Insulation | Multi-layered with lightweight refractory bricks for energy efficiency. |
Applications | Sintering, annealing, heat treatment, material synthesis, and more. |
Industries | Ceramics, metallurgy, electronics, research institutions. |
Key Features | Precise temperature control, uniform heating, and versatile applications. |
Challenges | High energy consumption and material durability requirements. |
Ready to elevate your high-temperature processes? Contact us today to find the perfect 1800°C furnace for your needs!