A 4 high rolling mill is a specialized type of rolling mill used in metalworking to achieve tighter tolerances and produce extremely thin materials. It consists of two smaller work rolls supported by two larger backup rolls. This configuration allows for precise control over the rolling process, enabling the production of high-quality, thin sheets or plates with consistent thickness and surface finish. The backup rolls provide the necessary support to the work rolls, preventing deflection and ensuring uniform pressure distribution across the material being rolled. This makes 4 high rolling mills ideal for applications requiring high precision and fine material reduction.
Key Points Explained:
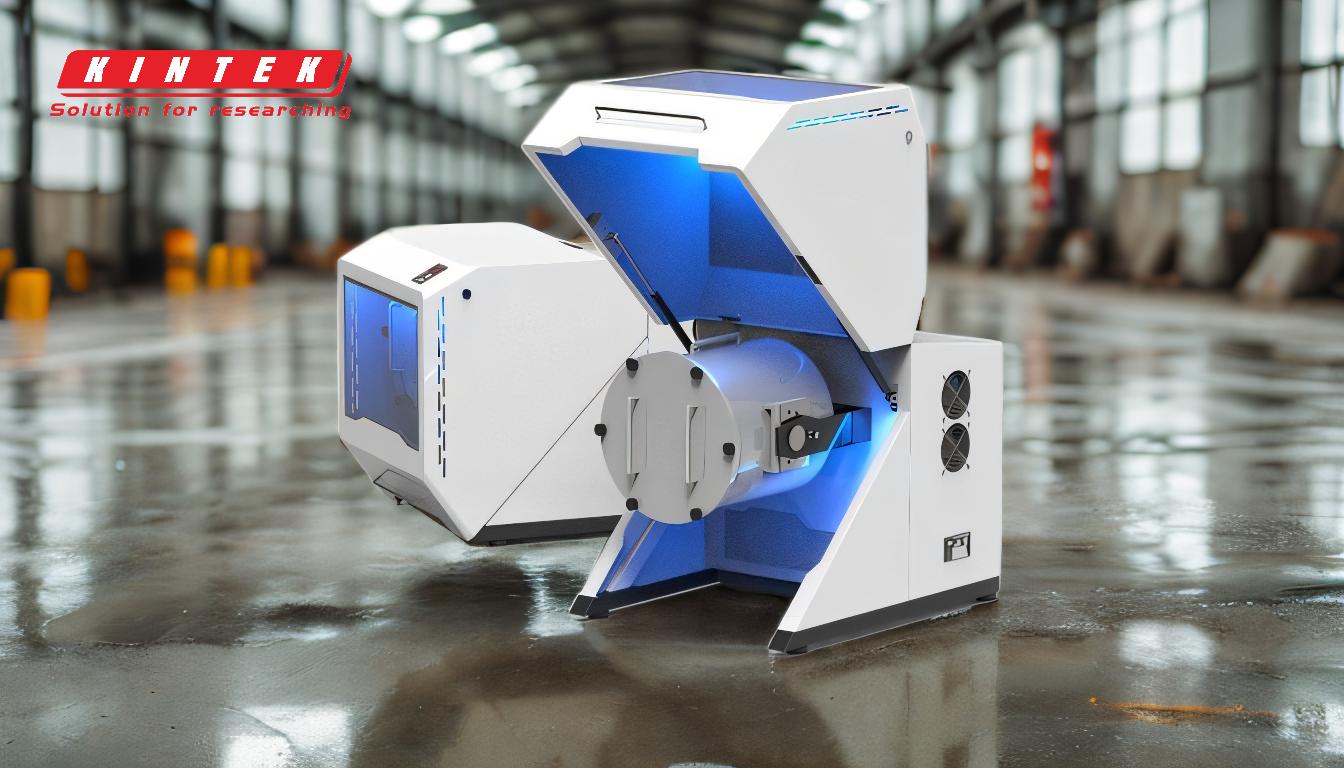
-
Definition of a 4 High Rolling Mill:
- A 4 high rolling mill is a type of rolling mill that uses four rolls: two smaller work rolls and two larger backup rolls.
- The work rolls are in direct contact with the material being rolled, while the backup rolls support the work rolls to maintain stability and precision.
-
Purpose and Applications:
- Tighter Tolerances: The 4 high configuration allows for more precise control over the rolling process, resulting in materials with tighter dimensional tolerances.
- Thin Material Production: It is particularly effective in reducing material to extremely small thicknesses, making it suitable for producing thin sheets or plates.
- High-Quality Output: The mill is capable of producing materials with consistent thickness and superior surface finish, which is essential in industries like automotive, aerospace, and electronics.
-
Advantages of the 4 High Rolling Mill:
- Reduced Roll Deflection: The backup rolls prevent the work rolls from deflecting under pressure, ensuring uniform thickness across the material.
- Enhanced Precision: The smaller work rolls allow for finer adjustments and greater control over the rolling process.
- Versatility: It can handle a wide range of materials, including metals like steel, aluminum, and copper, making it versatile for various industrial applications.
-
Comparison with Other Rolling Mills:
- 2 High Rolling Mills: These mills have only two rolls and are simpler in design but lack the precision and support provided by backup rolls. They are typically used for heavier reductions and less precise applications.
- Cluster Mills: These mills have multiple rolls arranged in a cluster, offering even greater support and precision than 4 high mills but are more complex and expensive.
-
Operational Considerations:
- Roll Alignment: Proper alignment of the work and backup rolls is crucial to ensure uniform material thickness and prevent defects.
- Lubrication and Cooling: Adequate lubrication and cooling are necessary to maintain the performance and longevity of the rolls, especially when rolling at high speeds or with hard materials.
- Maintenance: Regular maintenance is required to keep the mill in optimal condition, including roll inspection, replacement, and alignment checks.
-
Industries and Use Cases:
- Automotive: Used for producing thin, high-strength steel sheets for car bodies and components.
- Aerospace: Essential for manufacturing lightweight, high-precision aluminum and titanium sheets.
- Electronics: Ideal for producing ultra-thin foils and sheets used in electronic devices and components.
- Construction: Used for creating durable, precise metal sheets for building materials and structural components.
In summary, a 4 high rolling mill is a sophisticated piece of equipment designed for precision metalworking. Its unique configuration of work and backup rolls allows for the production of high-quality, thin materials with tight tolerances, making it indispensable in industries that demand precision and consistency.
Summary Table:
Aspect | Details |
---|---|
Definition | A rolling mill with 4 rolls: 2 smaller work rolls and 2 larger backup rolls. |
Purpose | Produces thin materials with tight tolerances and superior surface finish. |
Advantages | Reduced roll deflection, enhanced precision, and material versatility. |
Key Applications | Automotive, aerospace, electronics, and construction industries. |
Operational Needs | Roll alignment, lubrication, cooling, and regular maintenance required. |
Learn how a 4 high rolling mill can elevate your metalworking precision—contact us today!