A carbon regeneration kiln is a specialized industrial furnace designed to restore the adsorption capacity of spent activated carbon by heating it to high temperatures, typically around 700°C. This process removes organic and inorganic contaminants that have accumulated on the carbon's surface, effectively "recharging" it for reuse. The kiln operates indirectly, meaning the heat source is separate from the carbon being treated, ensuring precise temperature control and preventing contamination. Energy efficiency is enhanced through features like recycle ducts, which recapture and reuse heat. Carbon regeneration kilns are crucial in industries like water treatment, air purification, and chemical processing, where activated carbon is extensively used for filtration and purification.
Key Points Explained:
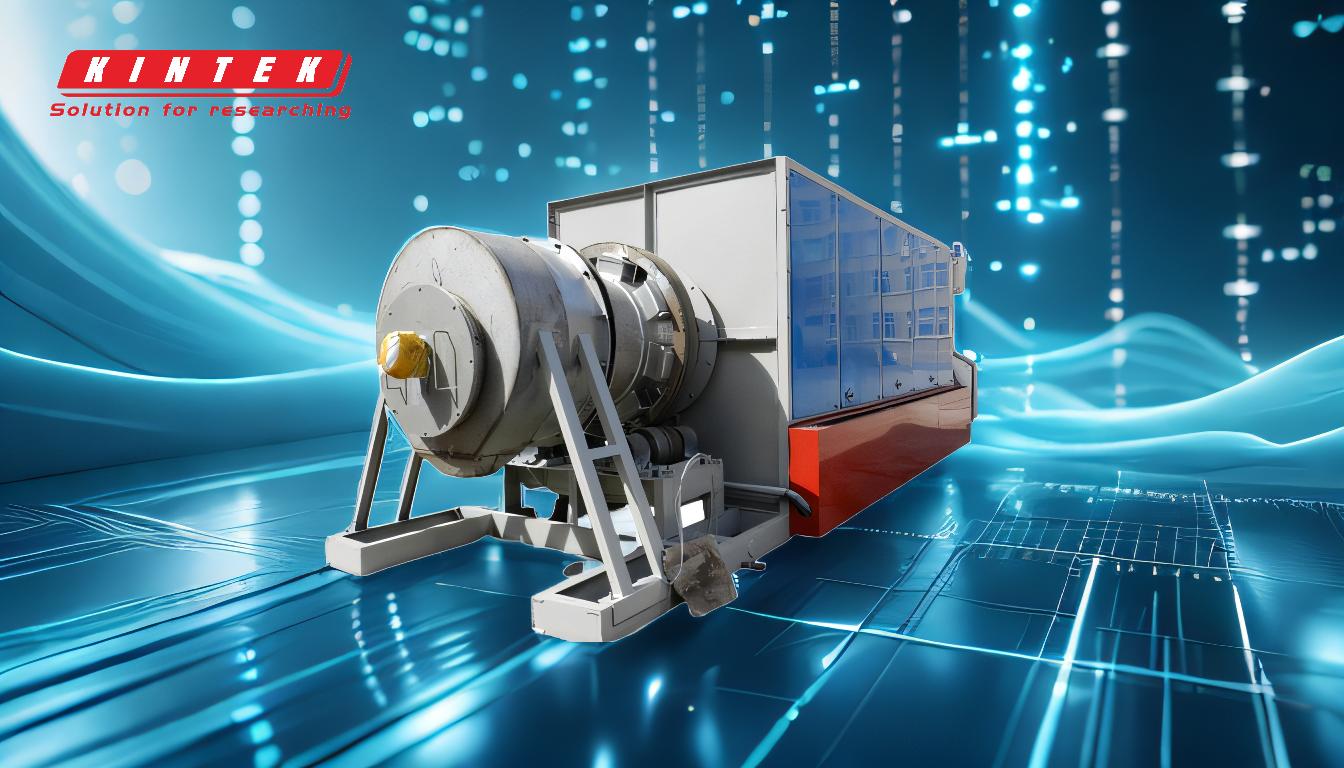
-
Purpose of a Carbon Regeneration Kiln:
- A carbon regeneration kiln is used to restore the adsorption capacity of spent activated carbon.
- It removes accumulated organic and inorganic contaminants by heating the carbon to high temperatures (around 700°C).
- This process allows the carbon to be reused, reducing waste and operational costs.
-
Indirect Heating Mechanism:
- The kiln operates using indirect heating, meaning the heat source is separate from the carbon being treated.
- This design ensures precise temperature control and prevents contamination of the carbon.
- Indirect heating is essential for maintaining the integrity and performance of the regenerated carbon.
-
High-Temperature Chamber:
- The kiln is constructed from refractory materials that can withstand extreme temperatures without melting.
- These materials help contain and build up heat, enabling the carbon to reach the necessary temperatures for regeneration.
- The chamber design also protects the carbon during the heating and cooling processes.
-
Energy Efficiency Features:
- Carbon regeneration kilns often include systems like recycle ducts to improve energy efficiency.
- Recycle ducts capture and reuse heat, reducing the overall energy consumption of the process.
- This makes the regeneration process more sustainable and cost-effective.
-
Applications in Industry:
- Carbon regeneration kilns are essential in industries that rely heavily on activated carbon for filtration and purification.
- Common applications include water treatment, air purification, and chemical processing.
- By regenerating spent carbon, these industries can reduce their environmental impact and operational expenses.
-
Benefits of Carbon Regeneration:
- Reduces the need for new activated carbon, lowering material costs.
- Minimizes waste by reusing carbon, contributing to sustainability efforts.
- Ensures consistent performance of filtration systems by maintaining high-quality carbon.
By understanding these key points, equipment and consumable purchasers can make informed decisions about investing in carbon regeneration kilns, ensuring they meet their operational and sustainability goals.
Summary Table:
Key Features | Benefits |
---|---|
Purpose | Restores adsorption capacity of spent activated carbon, enabling reuse. |
Indirect Heating Mechanism | Ensures precise temperature control and prevents contamination. |
High-Temperature Chamber | Withstands extreme temperatures, protecting carbon during regeneration. |
Energy Efficiency Features | Recycle ducts capture and reuse heat, reducing energy consumption. |
Applications | Water treatment, air purification, chemical processing. |
Benefits | Reduces costs, minimizes waste, and ensures consistent filtration performance. |
Ready to optimize your filtration process with a carbon regeneration kiln? Contact us today to learn more!