A continuous furnace is a type of industrial furnace designed for the uninterrupted processing of materials at high temperatures. Unlike batch furnaces, which process materials in discrete batches, continuous furnaces allow for a steady flow of materials through the heating chamber, making them highly efficient for large-scale production. These furnaces are widely used in industries such as ceramics, metallurgy, electronics, and chemical processing for tasks like sintering, annealing, and material treatment. The continuous operation ensures consistent quality and reduces downtime, making it ideal for applications requiring high throughput and precise temperature control.
Key Points Explained:
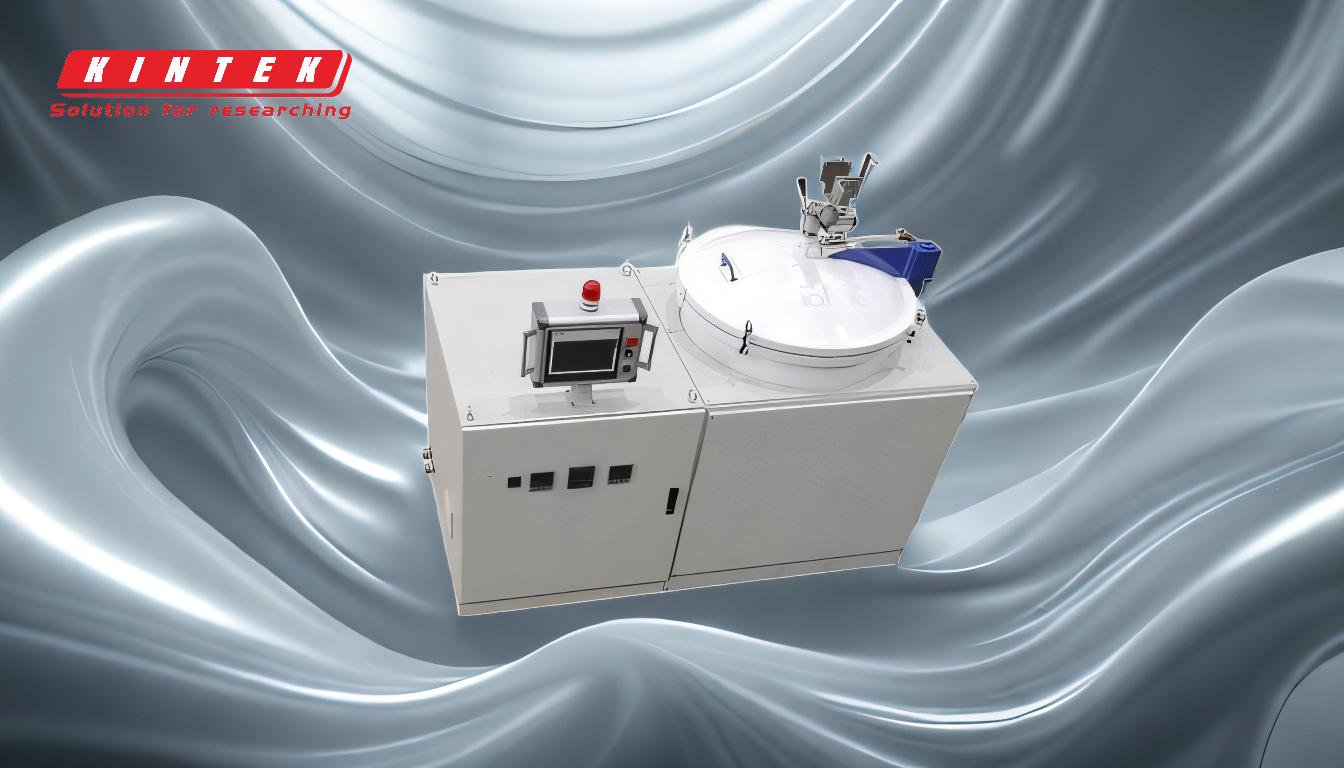
-
Definition and Functionality of a Continuous Furnace:
- A continuous furnace is designed to process materials in a continuous flow rather than in batches. This allows for uninterrupted production, which is crucial for industries requiring high-volume output.
- The furnace maintains a consistent temperature throughout the heating chamber, ensuring uniform treatment of materials as they move through the system.
-
Applications in Various Industries:
- Ceramics: Used for sintering ceramic materials and discharging ceramic glues.
- Metallurgy: Employed for annealing and sintering metal components.
- Electronics: Utilized in the production of electronic components that require precise thermal treatment.
- Chemical Industry: Applied in processes like powder roasting and high-temperature atmosphere sintering.
- Research and Development: Commonly found in universities and scientific research institutes for high-temperature experiments and material testing.
-
Advantages Over Batch Furnaces:
- Efficiency: Continuous furnaces reduce downtime between batches, leading to higher productivity.
- Consistency: The steady flow of materials ensures uniform heating and treatment, resulting in consistent product quality.
- Scalability: Ideal for large-scale production due to their ability to handle continuous material flow.
-
Key Components and Design Features:
- Heating Chamber: Designed to maintain a stable high-temperature environment.
- Conveyor System: Transports materials through the furnace at a controlled speed.
- Temperature Control System: Ensures precise regulation of the furnace temperature.
- Atmosphere Control: Some continuous furnaces are equipped with systems to control the atmosphere within the heating chamber, which is crucial for processes like sintering and annealing.
-
Comparison with Rotating Furnaces:
- While continuous furnaces are designed for large-scale, uninterrupted production, rotating furnaces are specialized for creating optical components like lenses and primary mirrors for telescopes. The rotating mechanism allows for uniform heating and shaping of these components, which is not a feature of continuous furnaces.
-
Operational Considerations:
- Maintenance: Regular maintenance is required to ensure the furnace operates efficiently and safely.
- Energy Consumption: Continuous furnaces can be energy-intensive, so optimizing energy use is crucial for cost-effectiveness.
- Safety: Proper safety measures must be in place to handle high temperatures and potentially hazardous materials.
In summary, a continuous furnace is a versatile and efficient tool for high-temperature processing across various industries. Its ability to handle continuous material flow makes it indispensable for large-scale production, ensuring consistent quality and high throughput.
Summary Table:
Aspect | Details |
---|---|
Definition | Processes materials in a continuous flow, ideal for large-scale production. |
Applications | Ceramics, metallurgy, electronics, chemical processing, and R&D. |
Advantages | High efficiency, consistent quality, and scalability. |
Key Components | Heating chamber, conveyor system, temperature control, and atmosphere control. |
Operational Considerations | Requires regular maintenance, energy optimization, and safety measures. |
Ready to enhance your production process with a continuous furnace? Contact us today for expert guidance!