A controlled atmosphere furnace is a specialized heating system designed for heat treatment processes that require precise temperature control and a tightly sealed environment to prevent oxidation, decarburization, or contamination. It is widely used in industries and laboratories for processes like annealing, brazing, carburizing, and sintering. The furnace creates a protective or reactive atmosphere, such as inert gases or hydrogen, to ensure optimal material properties during heating and cooling. Key advantages include energy efficiency, thermal homogeneity, accurate controls, and the ability to handle parts of all shapes and sizes. This technology is essential for achieving consistent, high-quality results in material processing.
Key Points Explained:
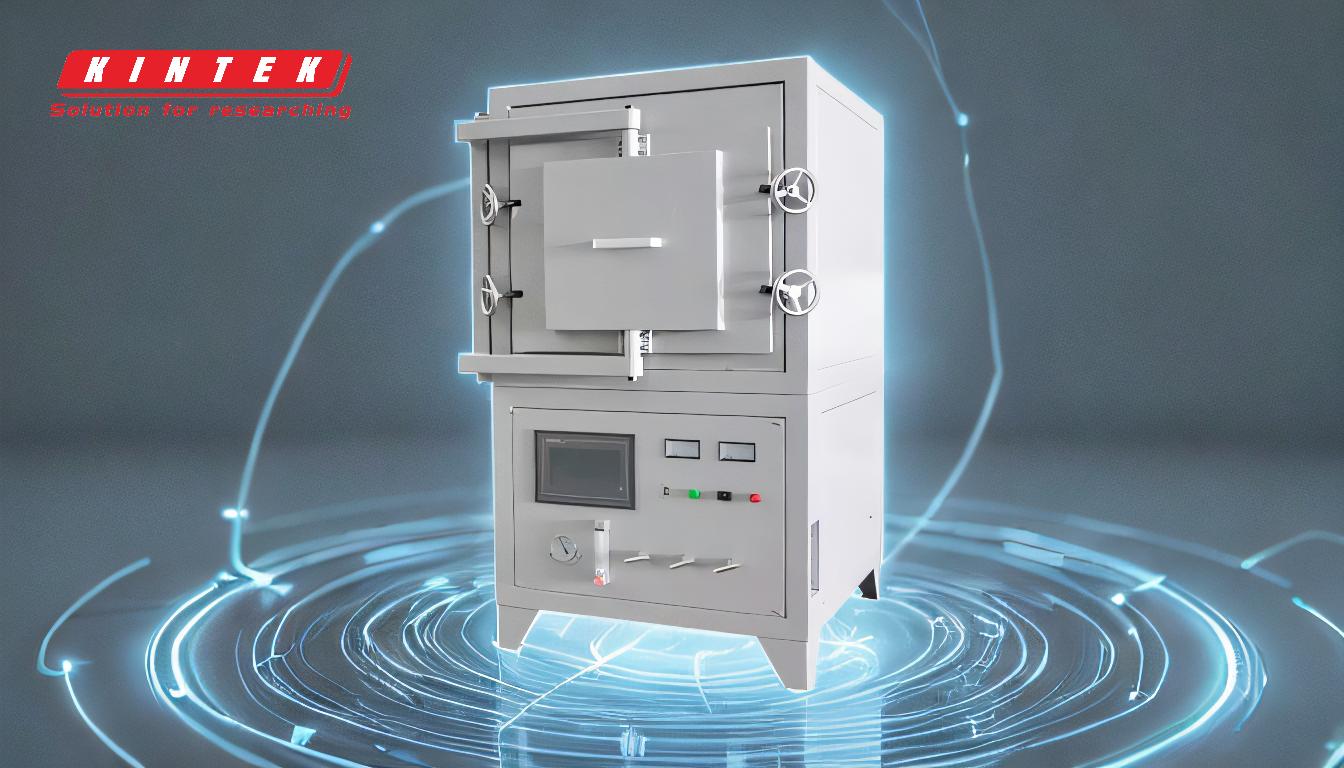
-
Definition and Purpose of a Controlled Atmosphere Furnace
A controlled atmosphere furnace is a heating system that provides a tightly sealed environment with precise temperature and atmospheric control. Its primary purpose is to prevent oxidation, decarburization, and contamination during heat treatment processes. This ensures the retention of desired material properties, such as strength and ductility, while improving product quality and consistency. -
Key Applications in Heat Treatment
- Annealing: Softens materials to improve machinability and reduce internal stresses.
- Brazing: Joins metals using a filler material without melting the base metals.
- Carburizing: Increases surface hardness by introducing carbon into the material.
- Sintering: Bonds powdered materials into a solid structure through heat and pressure.
- Bright Annealing: Prevents oxidation to maintain a bright, clean surface finish.
- Neutral Hardening: Avoids surface reactions to maintain material integrity.
-
Advantages of Using a Controlled Atmosphere Furnace
- Energy Efficiency: Low energy consumption and reduced operating costs.
- High Performance: Ensures thermal homogeneity and precise temperature control.
- Versatility: Suitable for parts of all shapes and sizes.
- Safety: Equipped with advanced safety devices to prevent accidents.
- Differentiated Finish: Achieves high-quality surface finishes without oxidation or contamination.
-
How a Controlled Atmosphere Improves Heat Treatment
- Prevents Oxidation and Decarburization: By controlling the levels of O2, CO, and water vapor, the furnace ensures the workpiece remains free from surface reactions.
- Enhances Material Properties: Maintains the alloy's desired properties, such as strength and ductility.
- Increases Production Efficiency: Reduces waste and rework by ensuring consistent results.
-
Critical Features of a Controlled Atmosphere Furnace
- Tightly Sealed Environment: Prevents external air from entering and disrupting the process.
- Precise Temperature Control: Ensures uniform heating and cooling for optimal results.
- Customizable Atmospheres: Allows the use of inert gases (e.g., nitrogen, argon) or reactive gases (e.g., hydrogen) depending on the application.
-
Industrial and Laboratory Applications
- Industrial Use: Ensures consistency in heating industrial parts, meeting quality standards, and preventing reactions with air.
- Laboratory Use: Provides a controlled environment for material processing, enabling precise experiments and research.
In summary, a controlled atmosphere furnace is a critical tool for heat treatment processes, offering precision, efficiency, and consistency. Its ability to create a controlled environment ensures high-quality outcomes, making it indispensable in industries ranging from aerospace to automotive and in advanced material research laboratories.
Summary Table:
Key Features | Applications | Advantages |
---|---|---|
Tightly sealed environment | Annealing, brazing, sintering | Energy efficiency |
Precise temperature control | Carburizing, bright annealing | Thermal homogeneity |
Customizable atmospheres | Neutral hardening | Versatility for all shapes and sizes |
Discover how a controlled atmosphere furnace can enhance your heat treatment processes—contact our experts today!