A crucible furnace is a specialized type of furnace used primarily in metallurgy and glass manufacturing for melting and casting materials. It is particularly suited for small-scale production and for processing materials with specific properties, such as low-melting-point metals (e.g., brass, bronze, aluminum) or specialty glasses (e.g., borosilicate glass). The furnace operates by heating a crucible, which contains the material, until it reaches its melting point. The molten material is then poured into molds to create the desired shape. Crucible furnaces are known for their simplicity, versatility, and ability to handle precise temperature control, making them a staple in industries requiring controlled melting processes.
Key Points Explained:
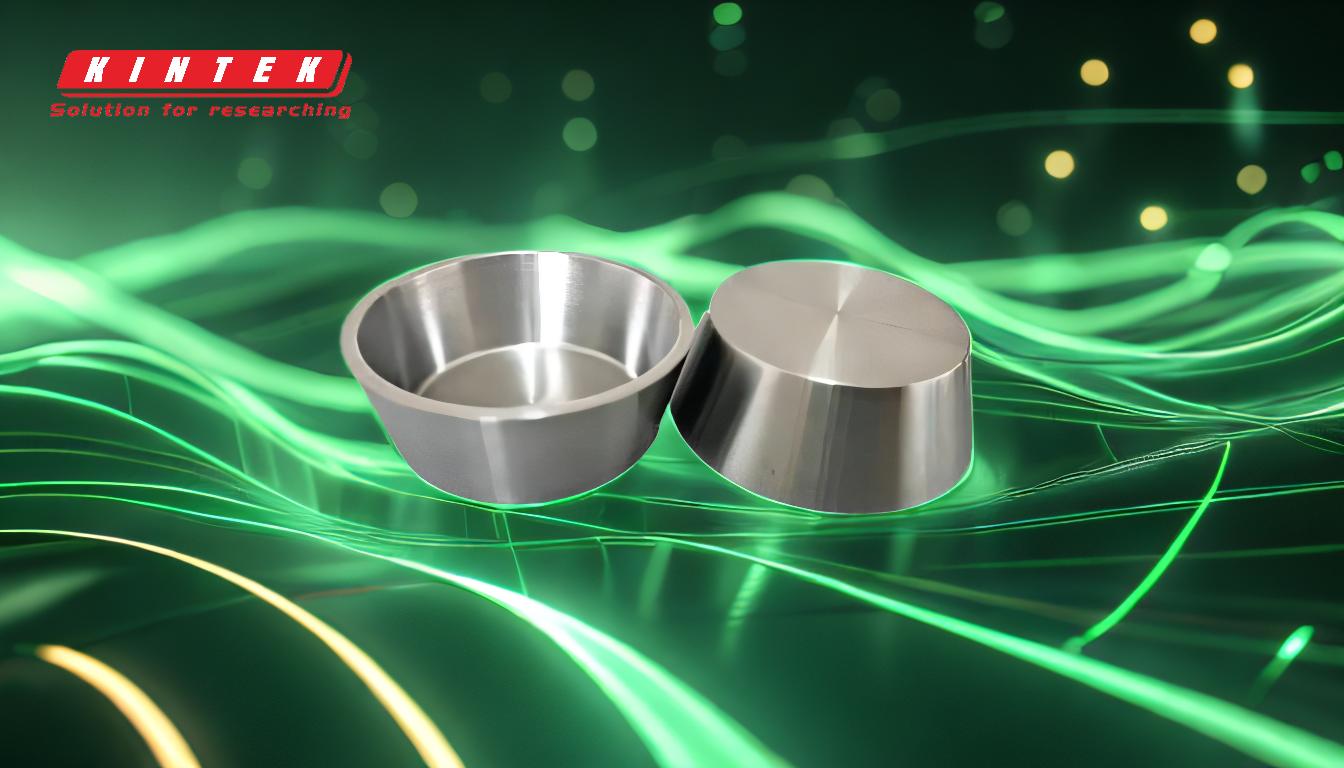
-
Definition and Purpose of a Crucible Furnace:
- A crucible furnace is a type of foundry furnace designed for melting and casting metals and alloys, particularly those with low melting points like brass, bronze, and aluminum.
- It is also used in glass manufacturing, especially for small-scale production and specialty glasses such as borosilicate glass.
- The primary purpose of the furnace is to melt the material, which is a critical step in casting processes.
-
How a Crucible Furnace Works:
- The furnace operates by heating the material placed inside a crucible.
- A heating element generates heat, which is transferred to the crucible, causing the material to heat up and eventually melt.
- Once molten, the material is poured into molds or containers to achieve the desired shape.
- The process can be controlled by adjusting the heat or using a temperature control system, ensuring precise melting conditions.
-
Applications of Crucible Furnaces:
- Metallurgy: Crucible furnaces are widely used in metallurgy for melting and casting metals and alloys. They are particularly useful for small-scale production and for creating alloys with specific properties.
- Glass Manufacturing: These furnaces are also employed in the production of specialty glasses, such as borosilicate glass, where controlled melting is essential.
-
Advantages of Crucible Furnaces:
- Versatility: Suitable for a wide range of materials, including metals and glasses.
- Precision: Allows for controlled melting processes, which is crucial for producing high-quality materials.
- Simplicity: The design is straightforward, making it easy to operate and maintain.
- Small-Scale Production: Ideal for small-scale or specialized production runs where large industrial furnaces are not necessary.
-
Design and Operation Considerations:
- The size and design of the furnace can impact the melting time and efficiency.
- Temperature control systems are often integrated to ensure consistent and accurate melting conditions.
- Crucibles are typically made from materials that can withstand high temperatures and resist chemical reactions with the molten material.
-
Historical Significance:
- Crucible furnaces are one of the oldest types of melting ovens, with a long history of use in metalworking and glassmaking.
- Their enduring popularity is a testament to their effectiveness and adaptability in various industrial applications.
By understanding these key points, one can appreciate the role of crucible furnaces in the casting process and their importance in industries requiring precise and controlled melting of materials.
Summary Table:
Aspect | Details |
---|---|
Purpose | Melting and casting metals, alloys, and specialty glasses. |
Key Applications | Metallurgy (brass, bronze, aluminum) and glass manufacturing (borosilicate). |
Advantages | Versatility, precision, simplicity, and suitability for small-scale production. |
Operation | Heats material in a crucible; molten material is poured into molds. |
Design Considerations | Size, temperature control, and crucible material durability. |
Historical Significance | One of the oldest types of melting ovens, widely used in metalworking and glassmaking. |
Discover how a crucible furnace can enhance your production process—contact us today!