A CVD (Chemical Vapor Deposition) reactor is a specialized equipment used to deposit thin films of materials onto a substrate through chemical reactions involving gaseous precursors. This process is widely used in industries such as semiconductors, optics, and biomedical devices to create high-quality, uniform films with specific properties. The reactor operates by introducing gaseous reactants into a chamber, where they react and deposit a thin film on the substrate. CVD reactors can operate under various conditions, including low pressure (LPCVD) and atmospheric pressure, depending on the application. High-pressure reactors, on the other hand, are designed to handle chemical reactions under extreme pressures and are used in research and industrial processes like hydrogenation, polymerization, and catalytic reactions. Both types of reactors play critical roles in advancing material science and chemical engineering.
Key Points Explained:
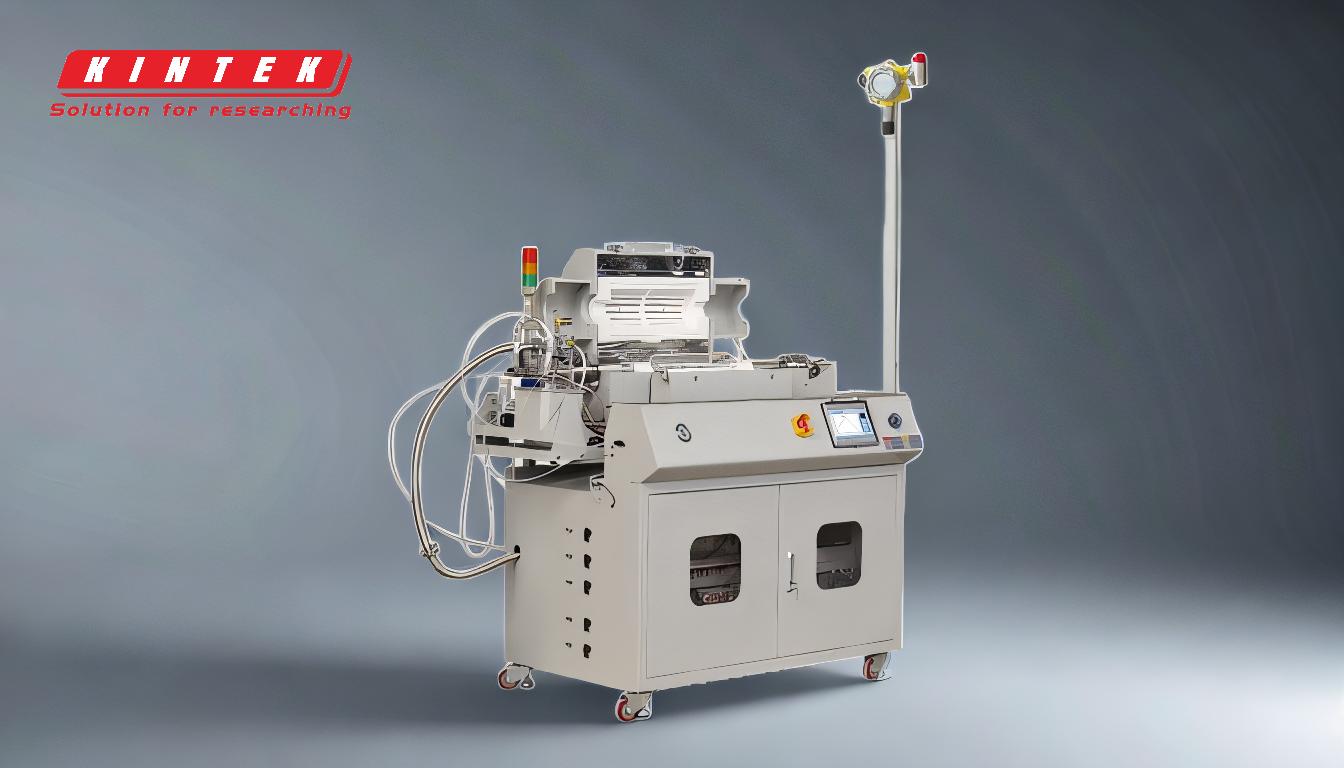
-
What is a CVD Reactor?
- A CVD reactor is a device used to deposit thin films on a substrate through chemical reactions involving gaseous precursors.
- The process involves introducing gaseous reactants into a chamber, where they react and form a solid film on the substrate.
- CVD reactors are widely used in industries such as semiconductors, optics, and biomedical devices to create high-quality, uniform films with specific properties.
-
Types of CVD Reactors
- Low-Pressure CVD (LPCVD): Operates under reduced pressure and is used for creating high-quality, uniform films. It is commonly used in semiconductor manufacturing and the production of biomedical devices like biosensors.
- Atmospheric Pressure CVD (APCVD): Operates at atmospheric pressure and is often used for simpler, cost-effective applications.
- Plasma-Enhanced CVD (PECVD): Uses plasma to enhance the chemical reaction, allowing for lower temperature deposition, which is useful for temperature-sensitive substrates.
-
Applications of CVD Reactors
- Semiconductor Industry: Used to deposit thin films of materials like silicon dioxide, silicon nitride, and polysilicon on wafers.
- Biomedical Devices: Used in the production of biosensors, cell phone sensors, and other medical devices.
- Optics and Coatings: Used to create anti-reflective coatings, protective layers, and optical films.
- Nanostructures: Used to develop complex nanostructures and high-quality polymers.
-
High-Pressure Reactors
- A high pressure reactor is a specialized vessel designed to conduct chemical reactions under high pressure.
- These reactors are used in processes like hydrogenation, polymerization, catalytic reactions, and petrochemical studies.
- They are built to withstand extreme pressures and provide an inert inner surface to prevent corrosion or contamination.
-
Key Components of a High-Pressure Reactor
- Pressure Vessel: The primary container that holds the reaction mixture and withstands high internal pressures.
- Closure System: A secure lid or cover designed to seal the reactor and maintain pressure.
- Temperature Control System: Regulates the temperature inside the reactor to ensure optimal reaction conditions.
- Pressure Control System: Includes valves, safety devices, and monitoring equipment to maintain and control pressure.
- Stirring Mechanism: Ensures uniform mixing of reactants for consistent reactions.
- Ports and Connections: Allow for the introduction of reactants, sampling, monitoring, and removal of products.
-
Advantages of CVD Reactors
- High-Quality Films: Produces uniform, high-quality films with precise control over thickness and composition.
- Versatility: Can deposit a wide range of materials, including metals, ceramics, and polymers.
- Scalability: Suitable for both small-scale research and large-scale industrial production.
-
Challenges and Considerations
- Material Compatibility: The choice of materials for the reactor and substrate must be compatible with the reactants and reaction conditions.
- Corrosion Resistance: High-pressure reactors, especially those made of metal, must be designed to resist corrosion.
- Safety: Both CVD and high-pressure reactors require strict safety protocols to handle high temperatures, pressures, and reactive gases.
-
Comparison Between CVD Reactors and High-Pressure Reactors
- Purpose: CVD reactors are primarily used for thin film deposition, while high-pressure reactors are used for conducting chemical reactions under extreme conditions.
- Operating Conditions: CVD reactors typically operate at lower pressures, whereas high-pressure reactors are designed to handle much higher pressures.
- Applications: CVD reactors are used in industries like semiconductors and optics, while high-pressure reactors are used in chemical synthesis, catalysis, and petrochemical processes.
By understanding the principles, components, and applications of CVD and high-pressure reactors, researchers and engineers can select the appropriate equipment for their specific needs, ensuring efficient and safe chemical processes.
Summary Table:
Aspect | Details |
---|---|
Definition | A CVD reactor deposits thin films on substrates using gaseous precursors. |
Types | LPCVD, APCVD, PECVD |
Applications | Semiconductors, biomedical devices, optics, nanostructures |
Advantages | High-quality films, versatility, scalability |
Challenges | Material compatibility, corrosion resistance, safety protocols |
Ready to enhance your thin film deposition process? Contact our experts today for a tailored solution!