Graphite rods play a crucial role in smelting and high-temperature industrial processes due to their exceptional thermal stability, resistance to oxidation, and dimensional integrity at extreme temperatures. In smelting, graphite rods are primarily used in degassing, fluxing, and as heating elements in high-temperature furnaces. Their ability to withstand temperatures up to 5000°F makes them ideal for applications requiring consistent heat distribution and durability. Additionally, graphite rods are utilized in various industries, including semiconductor manufacturing, glass production, and mechanical engineering, due to their conductivity and thermal properties. Their versatility extends to recreational products, but their industrial applications are far more significant, particularly in smelting and metal processing.
Key Points Explained:
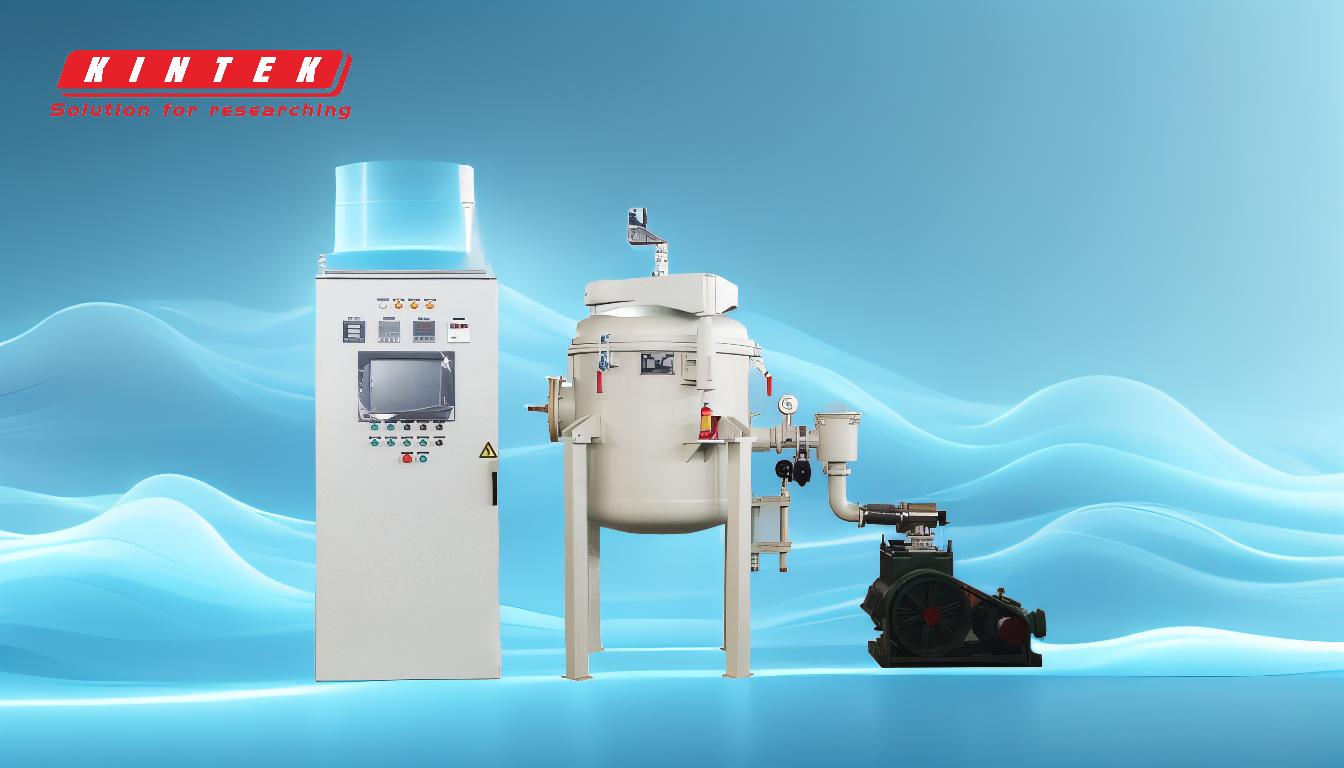
-
Thermal Stability and High-Temperature Applications
- Graphite rods are highly valued in smelting for their ability to maintain structural integrity at extremely high temperatures, up to 5000°F.
- This makes them suitable for use in high-temperature vacuum furnaces, where they serve as electric heaters.
- Their thermal stability ensures consistent performance, even under prolonged exposure to intense heat, which is critical for smelting processes.
-
Degassing and Fluxing in Smelting
- Graphite rods are commonly used in degassing shafts and impellers to remove unwanted gases from molten metals.
- They are also employed in fluxing, where they help purify metals by facilitating the removal of impurities.
- The rods' resistance to oxidation ensures that they do not degrade during these processes, maintaining the quality of the molten metal.
-
Heating Elements in Furnaces
- In high-temperature vacuum furnaces, graphite rods act as heating elements, providing uniform heat distribution.
- Their ability to facilitate oxidation at high temperatures simplifies the production of high-quality products in smelting and other industrial processes.
- This application is particularly important in industries like semiconductor manufacturing and metal processing.
-
Versatility Across Industries
- Beyond smelting, graphite rods are used in the semiconductor, glass, refractory, photovoltaic, and chemical industries.
- Their conductivity and thermal properties make them ideal for applications such as EDM (Electrical Discharge Machining) and mechanical engineering.
- This versatility underscores their importance in modern industrial processes.
-
Durability and Cost-Effectiveness
- Graphite rods are durable and resistant to wear, reducing the need for frequent replacements.
- Their cost-effectiveness, combined with their performance in high-temperature environments, makes them a preferred choice for smelting and other industrial applications.
-
Recreational Uses vs. Industrial Significance
- While graphite rods are used in recreational products like fishing rods and tent frames, their industrial applications are far more impactful.
- The focus on smelting and high-temperature processes highlights their critical role in manufacturing and material processing.
In summary, graphite rods are indispensable in smelting due to their thermal stability, durability, and versatility. Their use in degassing, fluxing, and as heating elements in high-temperature furnaces ensures efficient and high-quality metal processing. Their widespread industrial applications further demonstrate their importance in modern manufacturing and material science.
Summary Table:
Key Feature | Application in Smelting | Benefits |
---|---|---|
Thermal Stability | Maintains structural integrity at temperatures up to 5000°F. | Ensures consistent performance in high-temperature environments. |
Degassing and Fluxing | Removes unwanted gases and impurities from molten metals. | Improves metal quality and purity. |
Heating Elements | Provides uniform heat distribution in high-temperature vacuum furnaces. | Simplifies production of high-quality products. |
Versatility | Used in semiconductor, glass, refractory, and chemical industries. | Ideal for EDM, mechanical engineering, and other industrial processes. |
Durability | Resistant to wear and oxidation, reducing replacement frequency. | Cost-effective and reliable for long-term use. |
Want to learn more about how graphite rods can optimize your smelting processes? Contact our experts today!