Hydraulic systems and components are critical in various industries, and their failure can lead to significant downtime and costly repairs. A major cause of hydraulic system and component failures is contamination. Contaminants such as dirt, water, and metal particles can enter the system through various means, including poor maintenance practices, inadequate filtration, and environmental factors. These contaminants can cause wear and tear on components, leading to reduced efficiency, increased friction, and ultimately, system failure. Proper maintenance, including regular fluid analysis and filtration, is essential to prevent contamination and ensure the longevity of hydraulic systems.
Key Points Explained:
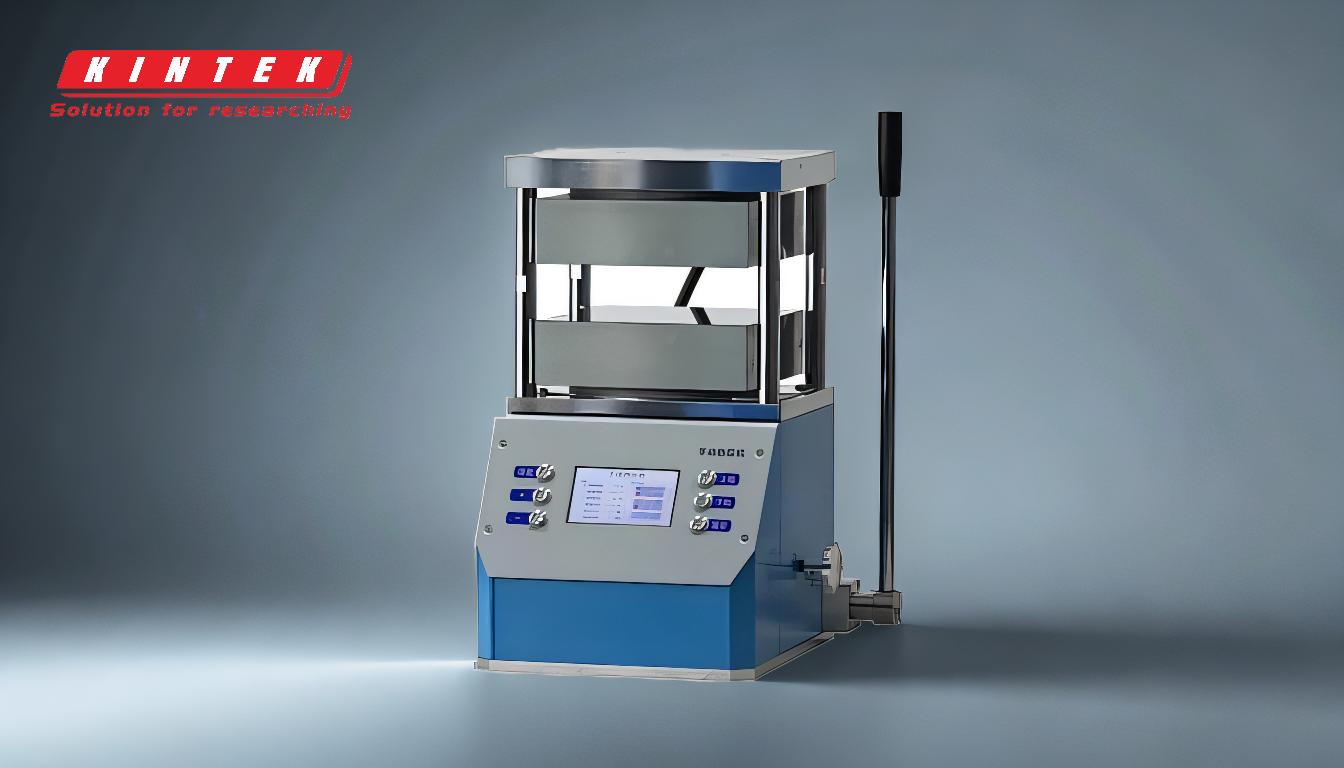
-
Contamination as a Primary Cause:
- Contamination is one of the leading causes of hydraulic system failures. Contaminants can be solid particles, water, or air, and they can enter the system through various pathways, such as during maintenance, through seals, or from the environment.
- Solid particles, such as dirt and metal shavings, can cause abrasive wear on components like pumps, valves, and cylinders. This wear leads to increased clearances, reduced efficiency, and eventual failure.
- Water contamination can lead to corrosion of metal components and degradation of hydraulic fluid, reducing its lubricating properties and leading to increased friction and wear.
- Air contamination can cause cavitation, where air bubbles collapse in the hydraulic fluid, leading to pitting and erosion of component surfaces.
-
Sources of Contamination:
- External Sources: Contaminants can enter the system from the external environment, especially in harsh operating conditions. For example, in construction or mining equipment, dirt and dust can easily infiltrate the system.
- Internal Sources: Wear and tear of internal components can generate metal particles that circulate within the system, exacerbating the contamination problem.
- Maintenance Practices: Improper maintenance, such as using dirty tools or failing to clean components during servicing, can introduce contaminants into the system.
-
Impact of Contamination on System Performance:
- Component Wear: Contaminants cause abrasive wear on moving parts, leading to increased clearances and reduced efficiency. Over time, this wear can cause components to fail.
- Fluid Degradation: Contaminants can degrade the hydraulic fluid, reducing its ability to lubricate and cool the system. This degradation can lead to increased operating temperatures and accelerated wear.
- System Blockages: Particulate contamination can block small passages and orifices in valves and other components, leading to restricted fluid flow and reduced system performance.
-
Preventive Measures:
- Filtration: Implementing high-quality filtration systems is crucial to removing contaminants from the hydraulic fluid. Regular replacement of filters and monitoring of filter condition can help maintain system cleanliness.
- Fluid Analysis: Regular fluid analysis can detect contamination early, allowing for corrective action before significant damage occurs. This analysis can identify the presence of water, particulate matter, and other contaminants.
- Proper Maintenance Practices: Ensuring that maintenance procedures are followed correctly can prevent contamination. This includes using clean tools, sealing open ports during servicing, and replacing worn components promptly.
- Environmental Controls: In environments where contamination is likely, additional measures such as protective covers and seals can help prevent contaminants from entering the system.
-
Economic and Operational Impact:
- Downtime: Hydraulic system failures due to contamination can lead to significant downtime, affecting productivity and leading to financial losses.
- Repair Costs: The cost of repairing or replacing failed components can be substantial, especially if the failure leads to secondary damage in the system.
- Energy Efficiency: Contaminated systems operate less efficiently, leading to increased energy consumption and higher operating costs.
In conclusion, contamination is a major cause of hydraulic system and component failures. By understanding the sources and impacts of contamination, and implementing effective preventive measures, operators can significantly reduce the risk of failure, ensuring the reliability and longevity of their hydraulic systems.
Summary Table:
Key Aspect | Details |
---|---|
Primary Cause | Contamination (dirt, water, metal particles) |
Sources of Contamination | External (environment), Internal (wear), Poor Maintenance Practices |
Impact on Performance | Component wear, fluid degradation, system blockages, reduced efficiency |
Preventive Measures | Filtration, fluid analysis, proper maintenance, environmental controls |
Economic Impact | Downtime, high repair costs, increased energy consumption |
Protect your hydraulic systems from contamination—contact our experts today for tailored solutions!