A muffle furnace is a versatile high-temperature heating device used across various industries and applications. It is primarily designed to isolate the material being heated from combustion byproducts, ensuring a clean and controlled environment for processes like ashing, heat treatment, and material analysis. Common uses include determining non-combustible content in samples, analyzing chemical properties of materials at high temperatures, and performing tasks like annealing, sintering, and calcination. It is widely employed in industries such as ceramics, glass, pharmaceuticals, and metallurgy, as well as in laboratories for research, quality control, and environmental analysis.
Key Points Explained:
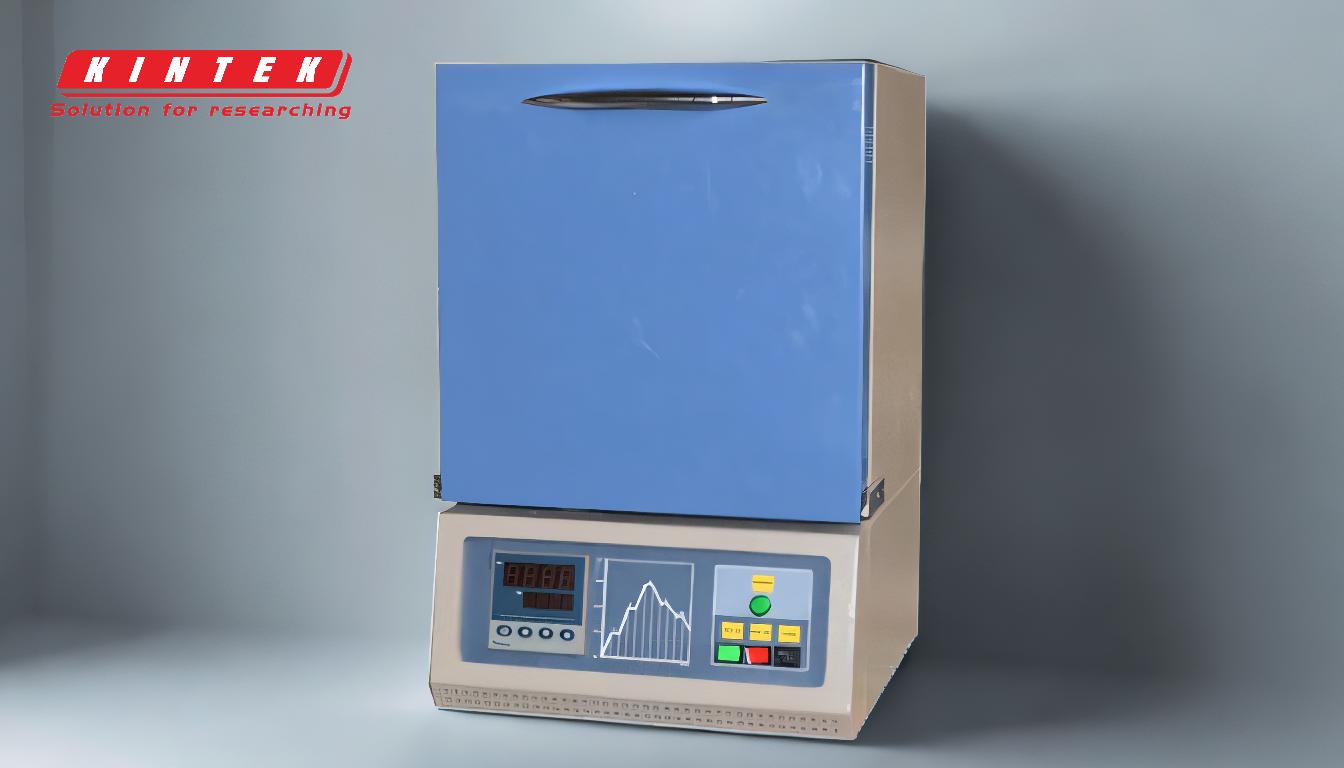
-
Primary Applications of a Muffle Furnace:
- Ashing and Combustible Content Analysis: Used to determine the non-combustible and non-volatile content in samples, such as ash content in materials.
- Heat Treatment: Processes like annealing, tempering, quenching, and normalizing are performed to improve the mechanical properties of metals and ceramics.
- Material Analysis: Used for loss on ignition analysis, thermogravimetric analysis, and identifying chemical properties of materials at high temperatures.
-
Industrial Uses:
- Metallurgy: Heating raw materials, blanks, and mechanical parts for processes like forging, rolling, and sintering.
- Ceramics and Glass: High-temperature firing, dissolution, and analysis of ceramics and glass materials.
- Pharmaceuticals: Drug inspections, medical sample pretreatment, and quality control in drug manufacturing.
-
Laboratory and Research Applications:
- Element Analysis: Used in laboratories for determining the composition of materials.
- Environmental Analysis: Used for water quality analysis, moisture determination, and ash melting point analysis.
- Materials Research: Applied in nuclear fuel disposal, materials testing, and high-temperature experiments.
-
Versatility Across Industries:
- Food Processing: Used for ashing and analyzing food samples.
- Scientific Research: Supports high-temperature experiments in fields like chemistry, physics, and materials science.
- Quality Control: Ensures consistency and reliability in manufacturing processes.
-
Key Processes Enabled by Muffle Furnaces:
- Annealing and Tempering: Softening or hardening materials to achieve desired properties.
- Sintering: Bonding particles together at high temperatures to form solid materials.
- Calcination: Heating materials to high temperatures to cause decomposition or phase transitions.
-
Advantages of Using a Muffle Furnace:
- Clean Heating Environment: The muffle design isolates samples from combustion gases, ensuring contamination-free results.
- Precise Temperature Control: Allows for accurate and consistent heating, essential for sensitive processes.
- Durability and Reliability: Designed to withstand extreme temperatures, making them suitable for long-term use in demanding applications.
In summary, a muffle furnace is an indispensable tool for high-temperature processes across industries, offering precision, versatility, and reliability for applications ranging from material analysis to industrial manufacturing.
Summary Table:
Application | Description |
---|---|
Ashing | Determines non-combustible content in samples (e.g., ash content). |
Heat Treatment | Processes like annealing, tempering, and quenching to improve material properties. |
Material Analysis | Identifies chemical properties and performs thermogravimetric analysis. |
Industrial Uses | Metallurgy, ceramics, glass, and pharmaceuticals for high-temperature processes. |
Laboratory Research | Element analysis, environmental testing, and materials research. |
Key Processes | Annealing, sintering, and calcination for material transformation. |
Advantages | Clean heating, precise temperature control, and durability. |
Learn how a muffle furnace can optimize your processes—contact us today for expert advice!