The physical vapor deposition (PVD) process is a widely used technique to apply very thin functional coatings on substrates. It involves the transfer of material from a target source to a substrate, typically in a vacuum environment, to form a thin film. This process is highly versatile, allowing for the deposition of coatings with precise thicknesses ranging from nanometers to micrometers. PVD is utilized in various industries, including automotive, aerospace, and electronics, to enhance the properties of materials, such as wear resistance, hardness, and oxidation resistance. The process is governed by key parameters like target material, deposition technology, chamber pressure, and substrate temperature, which influence the quality and properties of the deposited film.
Key Points Explained:
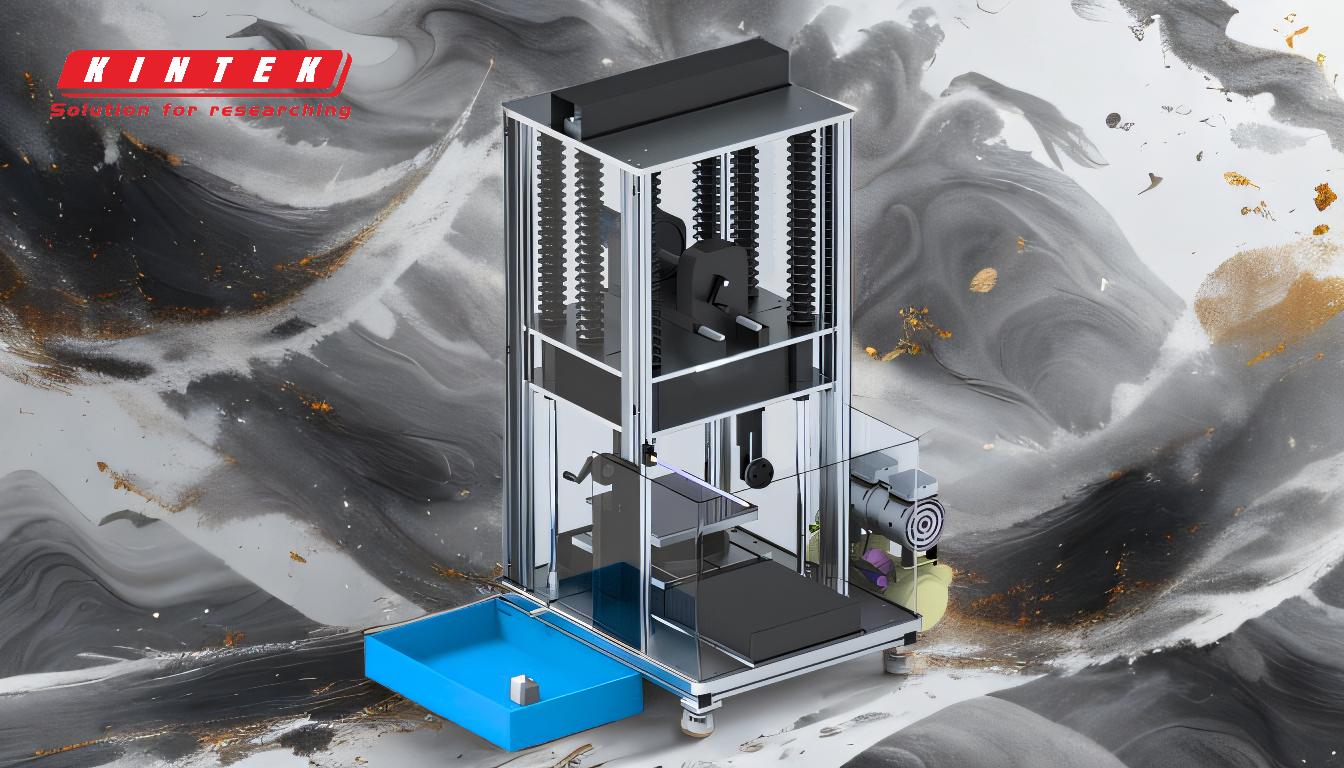
-
Definition and Purpose of PVD:
- Physical vapor deposition (PVD) is a process used to deposit thin, functional coatings on substrates. It is particularly valued for its ability to produce coatings with precise thicknesses and tailored properties, such as wear resistance, hardness, and oxidation resistance.
-
Stages of the PVD Process:
- Target Material Selection: The process begins with selecting a pure material source, known as the target. This material is chosen based on the desired properties of the final coating.
- Material Transport: The target material is transported to the substrate, typically through a vacuum or fluid medium. This step ensures that the material reaches the substrate in a controlled manner.
- Deposition: The target material is deposited onto the substrate, forming a thin film. This step is crucial as it determines the thickness and uniformity of the coating.
- Post-Deposition Treatment: Optionally, the deposited film may undergo annealing or heat treatment to improve its properties, such as adhesion and durability.
- Analysis and Optimization: The properties of the deposited film are analyzed, and the deposition process may be modified to achieve the desired results.
-
Key Parameters in PVD:
- Target Materials: The choice of target material (e.g., metals, semiconductors) significantly impacts the properties of the deposited film.
- Deposition Technology: Various technologies, such as electron beam lithography (EBL), atomic layer deposition (ALD), and plasma-enhanced chemical vapor deposition (PECVD), are used to achieve different deposition outcomes.
- Chamber Pressure and Substrate Temperature: These parameters influence the type and rate of material deposition, affecting the quality and properties of the thin film.
-
Applications of PVD:
- Decorative and Tribological Coatings: PVD is widely used in the automotive and tooling industries to apply decorative and wear-resistant coatings.
- Thermo-Optical Coatings: PVD is used to coat glass surfaces to enhance their thermo-optical properties, making them suitable for applications in energy-efficient windows and solar panels.
- Innovative Projects: PVD is increasingly being used in new markets, such as electronics and medical devices, where thin, functional coatings are essential.
-
Thin Film Growth Mechanisms:
- The deposition process involves several phases, including adsorption, surface diffusion, and nucleation. These phases are influenced by the material and substrate properties, as well as the deposition method and parameters. The interactions between the adsorbates and the substrate surface determine the growth mode and structure of the resulting thin film.
-
Advantages of PVD:
- Precision and Control: PVD allows for precise control over the thickness and composition of the deposited film, making it suitable for applications requiring high accuracy.
- Versatility: PVD can be used to deposit a wide range of materials, including metals, ceramics, and polymers, making it a versatile technique for various industries.
- Environmental Friendliness: PVD is a relatively clean process, as it typically involves minimal chemical waste and emissions.
In conclusion, the physical vapor deposition process is a sophisticated and versatile technique used to apply thin, functional coatings on substrates. Its ability to produce coatings with precise thicknesses and tailored properties makes it indispensable in various industries. By understanding the key parameters and stages involved in the PVD process, manufacturers can optimize their deposition techniques to achieve the desired film properties for specific applications.
Summary Table:
Aspect | Details |
---|---|
Definition | PVD is a technique to deposit thin, functional coatings on substrates. |
Key Stages | Target selection, material transport, deposition, post-treatment, analysis. |
Key Parameters | Target material, deposition technology, chamber pressure, substrate temp. |
Applications | Automotive, aerospace, electronics, decorative coatings, thermo-optical. |
Advantages | Precision, versatility, environmental friendliness. |
Discover how PVD can enhance your materials—contact our experts today for tailored solutions!