Sintering under uniaxial pressure is a specialized processing technique where powdered materials are heated and simultaneously compressed along a single axis. This method, often referred to as Hot Pressing (HP), combines heat and mechanical pressure to enhance particle bonding, reduce porosity, and improve material density. Unlike conventional sintering, which relies solely on heat, uniaxial pressure accelerates atomic diffusion and particle rearrangement, resulting in faster densification and superior mechanical properties. This technique is particularly useful for producing high-performance ceramics, composites, and advanced materials with tailored microstructures.
Key Points Explained:
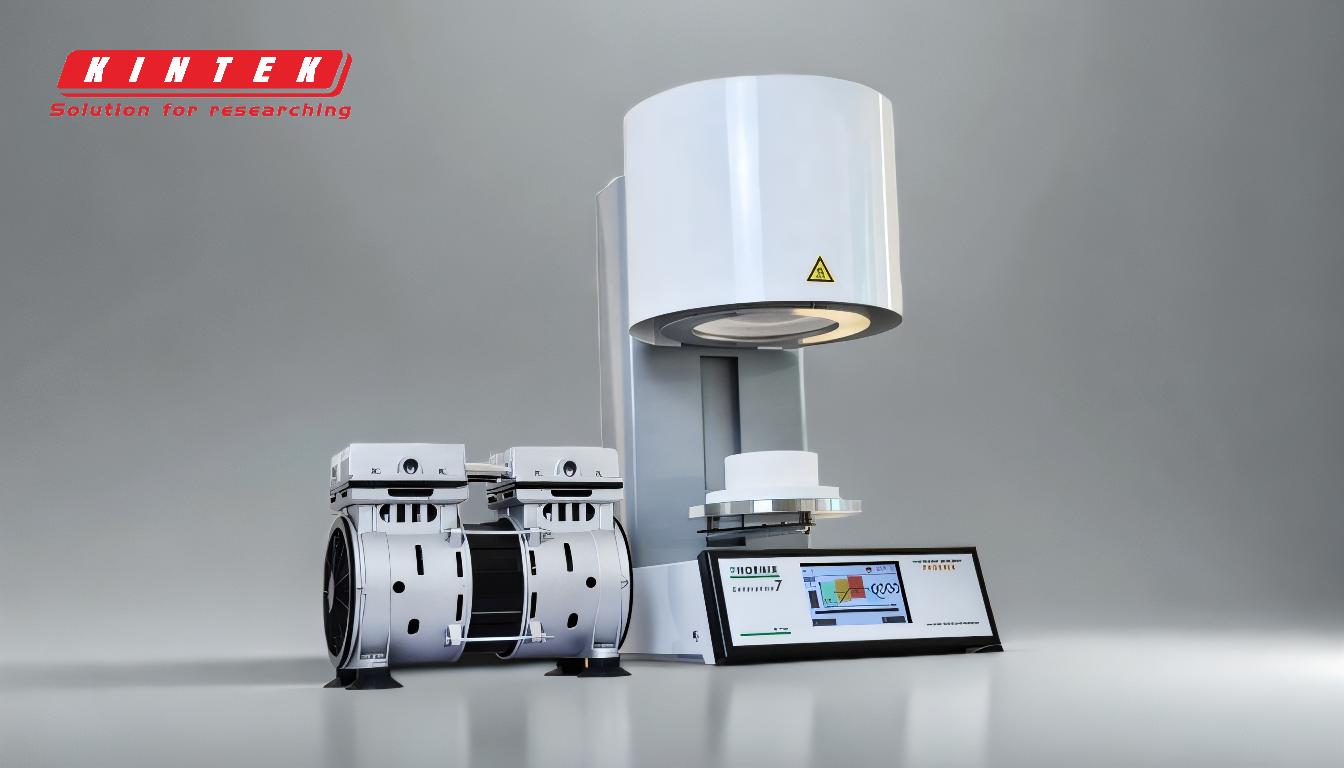
-
Definition of Sintering Under Uniaxial Pressure:
- Sintering under uniaxial pressure, commonly known as Hot Pressing (HP), involves applying heat and mechanical pressure along a single axis to a powdered material. This dual application of heat and pressure facilitates faster densification and improved material properties compared to traditional sintering methods.
-
How It Works:
- Heat Application: The powdered material is heated to a temperature just below its melting point, allowing atomic diffusion to occur and particles to bond.
- Uniaxial Pressure: Simultaneously, mechanical pressure is applied in one direction, compressing the powder and reducing voids or porosity. This pressure accelerates particle rearrangement and enhances bonding.
-
Advantages of Hot Pressing:
- Reduced Sintering Time: The application of pressure significantly shortens the sintering process by promoting faster particle bonding and densification.
- Lower Porosity: The combined effect of heat and pressure minimizes porosity, resulting in materials with higher density and better mechanical properties.
- Improved Microstructure: Hot pressing allows for precise control over the material's microstructure, leading to enhanced strength, hardness, and wear resistance.
-
Applications of Hot Pressing:
- Ceramics: Hot pressing is widely used in the production of advanced ceramics, such as silicon carbide (SiC) and alumina (Al₂O₃), which require high density and mechanical strength.
- Composites: This technique is ideal for manufacturing composite materials, where the combination of different phases (e.g., metal-ceramic composites) requires uniform densification.
- Advanced Materials: Hot pressing is employed in the development of specialized materials, including superalloys, refractory metals, and nanomaterials, where precise control over properties is critical.
-
Comparison with Other Sintering Techniques:
- Conventional Sintering: Unlike hot pressing, conventional sintering relies solely on heat, resulting in longer processing times and higher porosity.
- Spark Plasma Sintering (SPS): While SPS also uses pressure, it employs electric currents to generate heat, making it faster than hot pressing but requiring specialized equipment.
- Hot Isostatic Pressing (HIP): HIP applies pressure uniformly from all directions, making it suitable for complex shapes but often requiring additional post-processing steps.
-
Key Considerations for Hot Pressing:
- Equipment: Hot pressing requires specialized equipment capable of withstanding high temperatures and pressures, such as hydraulic presses and graphite dies.
- Material Selection: The choice of powder material and its properties (e.g., particle size, shape, and composition) significantly influence the outcome of the sintering process.
- Process Parameters: Temperature, pressure, and holding time must be carefully controlled to achieve optimal densification and material properties.
-
Challenges and Limitations:
- Cost: The equipment and energy requirements for hot pressing can be expensive, making it less suitable for large-scale production.
- Shape Limitations: Uniaxial pressure limits the complexity of shapes that can be produced, as the pressure is applied in a single direction.
- Material Compatibility: Not all materials are suitable for hot pressing, as some may degrade or react under high temperatures and pressures.
In summary, sintering under uniaxial pressure, or hot pressing, is a highly effective technique for producing dense, high-performance materials with superior mechanical properties. While it offers significant advantages in terms of reduced sintering time and improved microstructure, it also presents challenges related to cost and shape complexity. For equipment and consumable purchasers, understanding these trade-offs is essential for selecting the appropriate sintering method for specific applications.
Summary Table:
Key Aspect | Details |
---|---|
Definition | Sintering under uniaxial pressure, or Hot Pressing (HP), combines heat and mechanical pressure along a single axis. |
How It Works | Heat is applied below the melting point, while uniaxial pressure compresses the powder, reducing porosity. |
Advantages | Faster sintering, lower porosity, and improved microstructure. |
Applications | Ceramics, composites, and advanced materials like superalloys and nanomaterials. |
Comparison with Others | Faster than conventional sintering, less complex than HIP, but more limited in shape. |
Challenges | High cost, shape limitations, and material compatibility issues. |
Ready to enhance your material processing? Contact our experts today to learn more about hot pressing solutions!