Physical Vapor Deposition (PVD) is a vacuum-based coating process used to deposit thin films of material onto a substrate. It involves the vaporization of a solid material, transportation of the vaporized atoms or molecules through a vacuum or low-pressure environment, and their subsequent condensation onto a substrate to form a thin, uniform layer. The process is widely used in industries such as semiconductors, optics, and tool manufacturing due to its ability to produce high-quality, durable coatings with precise control over thickness and composition. PVD typically operates under high vacuum conditions and relatively low temperatures, making it suitable for a variety of materials and substrates.
Key Points Explained:
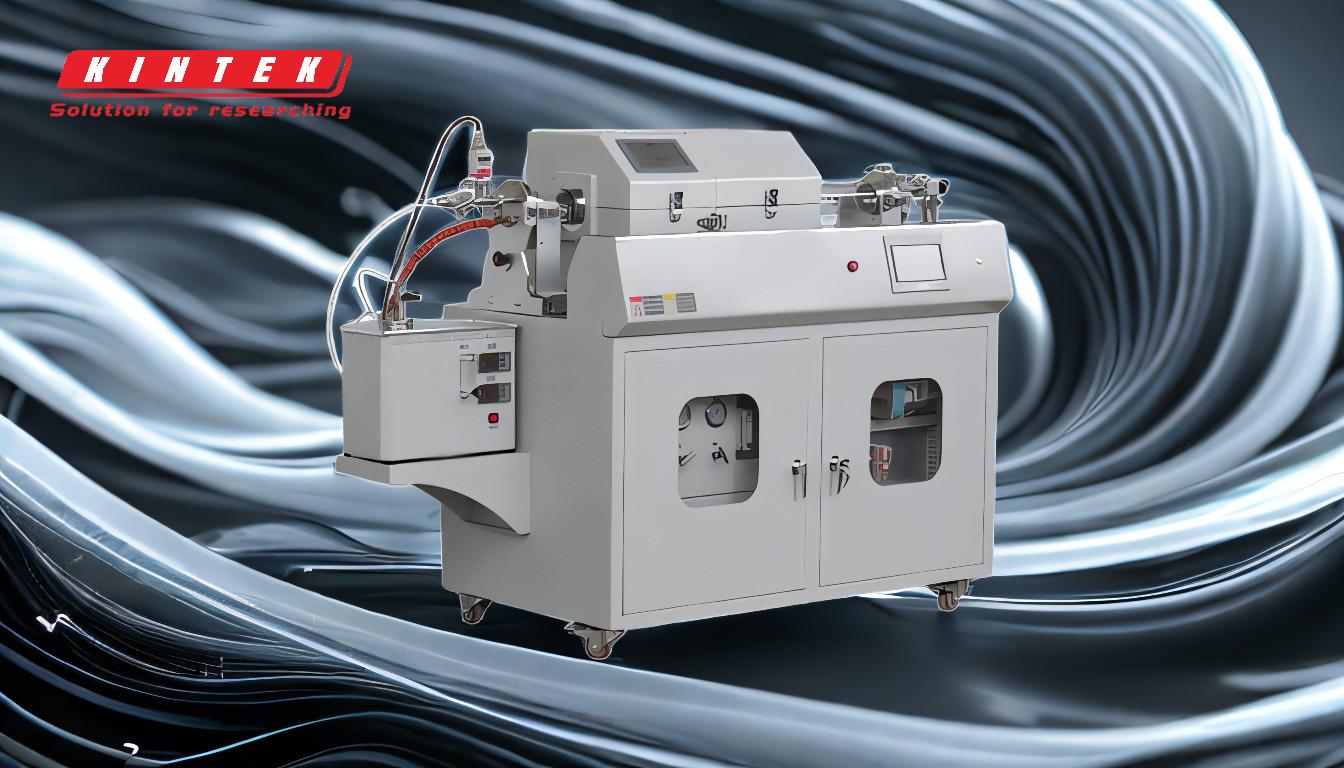
-
Definition and Purpose of PVD:
- PVD is a vacuum-based thin-film deposition process.
- It is used to create high-quality, durable coatings on substrates.
- Applications include semiconductor manufacturing, optical coatings, and tool coatings.
-
Key Steps in the PVD Process:
-
Vaporization:
- The solid material (target) is vaporized using methods like evaporation, sputtering, or laser ablation.
- This step converts the solid material into a vapor of atoms, molecules, or ions.
-
Transportation:
- The vaporized particles are transported through a vacuum or low-pressure environment.
- This step ensures that the particles move toward the substrate without contamination.
-
Reaction (Optional):
- In reactive PVD, a reactive gas (e.g., nitrogen or oxygen) is introduced to form a compound with the vaporized material.
- This step is used to create coatings with specific chemical compositions, such as nitrides or oxides.
-
Deposition:
- The vaporized particles condense onto the substrate, forming a thin, uniform layer.
- The substrate is typically held at a lower temperature to promote adhesion and film growth.
-
Vaporization:
-
Methods of Vaporization:
-
Evaporation:
- The target material is heated until it evaporates.
- Common techniques include thermal evaporation and electron beam evaporation.
-
Sputtering:
- High-energy ions bombard the target material, ejecting atoms from its surface.
- This method is widely used due to its ability to deposit a wide range of materials.
-
Laser Ablation:
- A high-power laser is used to vaporize the target material.
- This method is often used for materials that are difficult to evaporate or sputter.
-
Evaporation:
-
Environmental Conditions:
- PVD is performed under high vacuum conditions (typically 10^-6 to 10^-3 torr).
- The vacuum environment minimizes contamination and ensures precise control over the deposition process.
- The process operates at relatively low temperatures, making it suitable for temperature-sensitive substrates.
-
Advantages of PVD:
- Produces high-quality, durable coatings with excellent adhesion.
- Allows precise control over film thickness and composition.
- Suitable for a wide range of materials, including metals, ceramics, and polymers.
- Environmentally friendly compared to some other coating processes, as it generates minimal waste.
-
Applications of PVD:
-
Semiconductors:
- Used to deposit thin films for integrated circuits and microelectronics.
-
Optics:
- Creates anti-reflective, reflective, and protective coatings for lenses and mirrors.
-
Tool Manufacturing:
- Enhances the hardness and wear resistance of cutting tools and molds.
-
Decorative Coatings:
- Used to apply durable, aesthetically pleasing coatings on jewelry, watches, and consumer electronics.
-
Semiconductors:
-
Comparison to Other Deposition Techniques:
- PVD is distinct from Chemical Vapor Deposition (CVD), which involves chemical reactions to form the coating.
- PVD typically operates at lower temperatures than CVD, making it more suitable for temperature-sensitive substrates.
- PVD coatings are generally denser and more durable than those produced by electroplating or other wet-chemical methods.
By understanding the PVD process, purchasers of equipment and consumables can make informed decisions about the suitability of PVD for their specific applications, ensuring optimal performance and cost-effectiveness.
Summary Table:
Aspect | Details |
---|---|
Definition | Vacuum-based thin-film deposition process. |
Key Steps | Vaporization, Transportation, Reaction (optional), Deposition. |
Vaporization Methods | Evaporation, Sputtering, Laser Ablation. |
Advantages | High-quality coatings, precise control, environmentally friendly. |
Applications | Semiconductors, optics, tool manufacturing, decorative coatings. |
Comparison to CVD | Lower temperatures, denser, and more durable coatings. |
Discover how PVD can enhance your manufacturing process—contact us today for expert advice!