A rubber mixing mill, also known as a rolling mill, is a specialized piece of equipment used in the rubber manufacturing industry to create rubber compounds. Its primary function is to mix a rubber base material with various additives such as fillers, softeners, processing aids, and colorants. The process involves feeding an untreated rubber block into the nip between two rotating rolls that move in opposite directions. The rubber is repeatedly passed through the rolls, incorporating additives and ensuring a homogeneous mixture. Once the mixing is complete, the rubber compound is shaped and vulcanized for further use in manufacturing rubber products.
Key Points Explained:
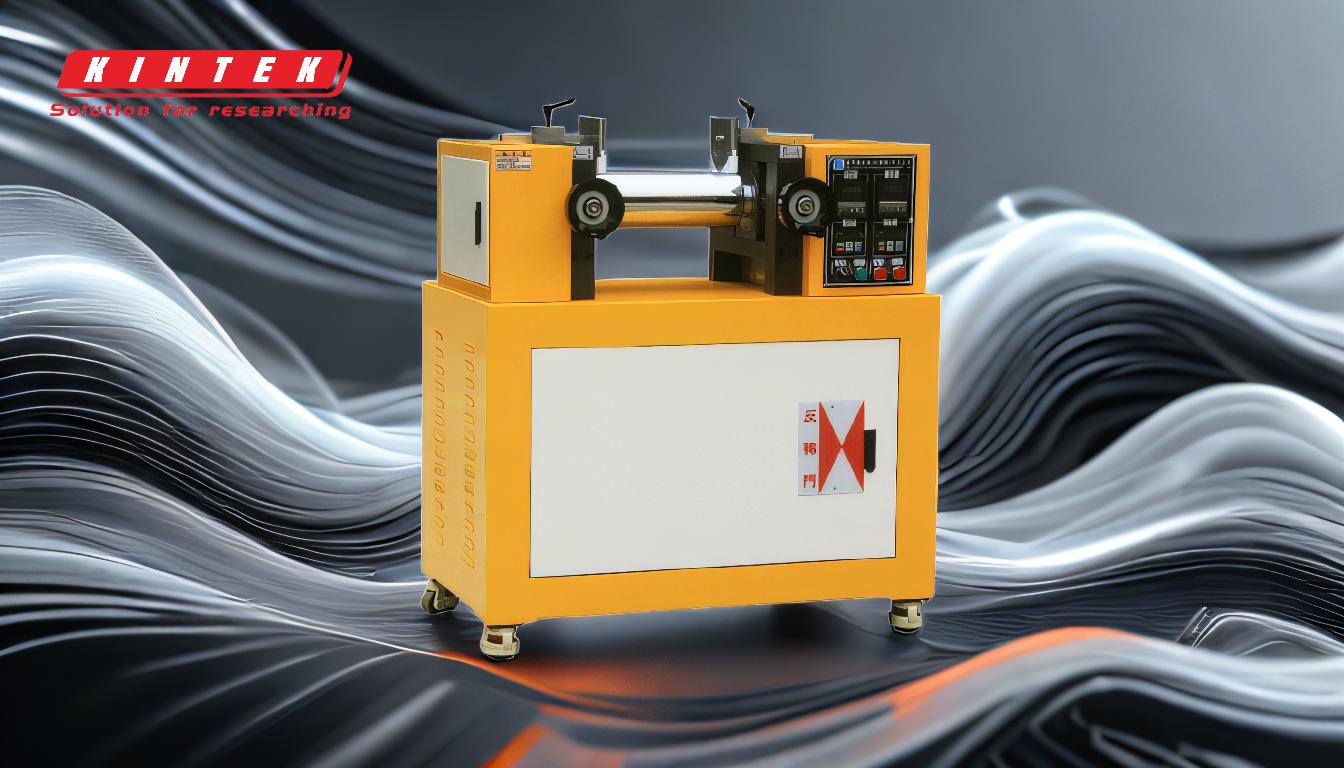
-
Purpose of a Rubber Mixing Mill:
- Rubber mixing mills are used to manufacture rubber compounds by blending a rubber base material with additives like fillers, softeners, processing aids, and colorants.
- This process ensures the rubber compound has the desired properties, such as strength, elasticity, and color, for use in various applications.
-
Basic Structure and Operation:
- A rubber mixing mill consists of two rolls that rotate in opposite directions.
- The rolls generate heat and friction, which helps in mixing the rubber and additives.
- One roll typically rotates faster than the other, creating shearing forces in the nip (gap) between the rolls. This shearing action is crucial for effective mixing.
-
Mixing Process:
- The process begins by inserting an untreated rubber block into the roll nip.
- The rubber block is pulled into the nip and wraps around the front roll.
- Additives are then fed into the nip, where they are incorporated into the rubber through repeated passes.
- The rubber is separated transversely and wound up to ensure uniform mixing. This process is repeated until the additives are fully integrated into the rubber base material.
-
Role of Additives:
- Fillers: Enhance the strength and durability of the rubber.
- Softeners: Improve flexibility and workability.
- Processing Aids: Facilitate easier mixing and shaping.
- Colorants: Provide the desired color to the rubber compound.
-
Final Stages of the Process:
- Once the mixing is complete, the rubber compound is shaped into the desired form.
- The shaped rubber is then vulcanized, a process that involves heating the rubber with sulfur or other agents to improve its strength, elasticity, and resistance to wear and tear.
-
Applications of Rubber Mixing Mills:
- Rubber mixing mills are essential in the production of a wide range of rubber products, including tires, seals, gaskets, hoses, and industrial rubber components.
- They are also used in the plastic industry for mixing plastic materials with additives.
-
Advantages of Using a Rubber Mixing Mill:
- Ensures a homogeneous mixture of rubber and additives.
- Provides precise control over the mixing process, allowing for consistent quality.
- Enhances the physical and chemical properties of the rubber compound.
-
Considerations for Purchasing a Rubber Mixing Mill:
- Roll Size and Speed: The size and speed of the rolls determine the capacity and efficiency of the mill.
- Heating and Cooling Systems: Proper temperature control is crucial for effective mixing and preventing material degradation.
- Durability and Maintenance: High-quality materials and ease of maintenance are important for long-term use.
- Safety Features: Ensure the mill has safety mechanisms to protect operators during operation.
By understanding these key points, a purchaser can make informed decisions when selecting a rubber calender for their specific manufacturing needs.
Summary Table:
Key Aspect | Details |
---|---|
Purpose | Mix rubber base material with additives for desired properties. |
Structure | Two counter-rotating rolls with controlled speed and heat generation. |
Mixing Process | Rubber is repeatedly passed through rolls to ensure uniform mixing. |
Additives | Fillers, softeners, processing aids, and colorants enhance properties. |
Applications | Used in tires, seals, gaskets, hoses, and industrial rubber components. |
Advantages | Homogeneous mixing, precise control, and enhanced rubber properties. |
Purchasing Factors | Roll size, speed, heating/cooling systems, durability, and safety features. |
Ready to enhance your rubber manufacturing process? Contact us today to find the perfect rubber mixing mill for your needs!