A sintering furnace for metal is a specialized piece of equipment used to heat metal powders to high temperatures, causing them to bond together without reaching their melting point. This process, known as sintering, reduces porosity and increases the density and strength of the final product. Sintering furnaces are essential in various industries, including automotive, aerospace, and electronics, for producing components like gears, bearings, and electrical contacts. The furnace operates under controlled conditions, often involving vacuum or specific atmospheric environments, to prevent oxidation and contamination, ensuring high-quality results. Safety is a critical feature due to the high temperatures and pressures involved.
Key Points Explained:
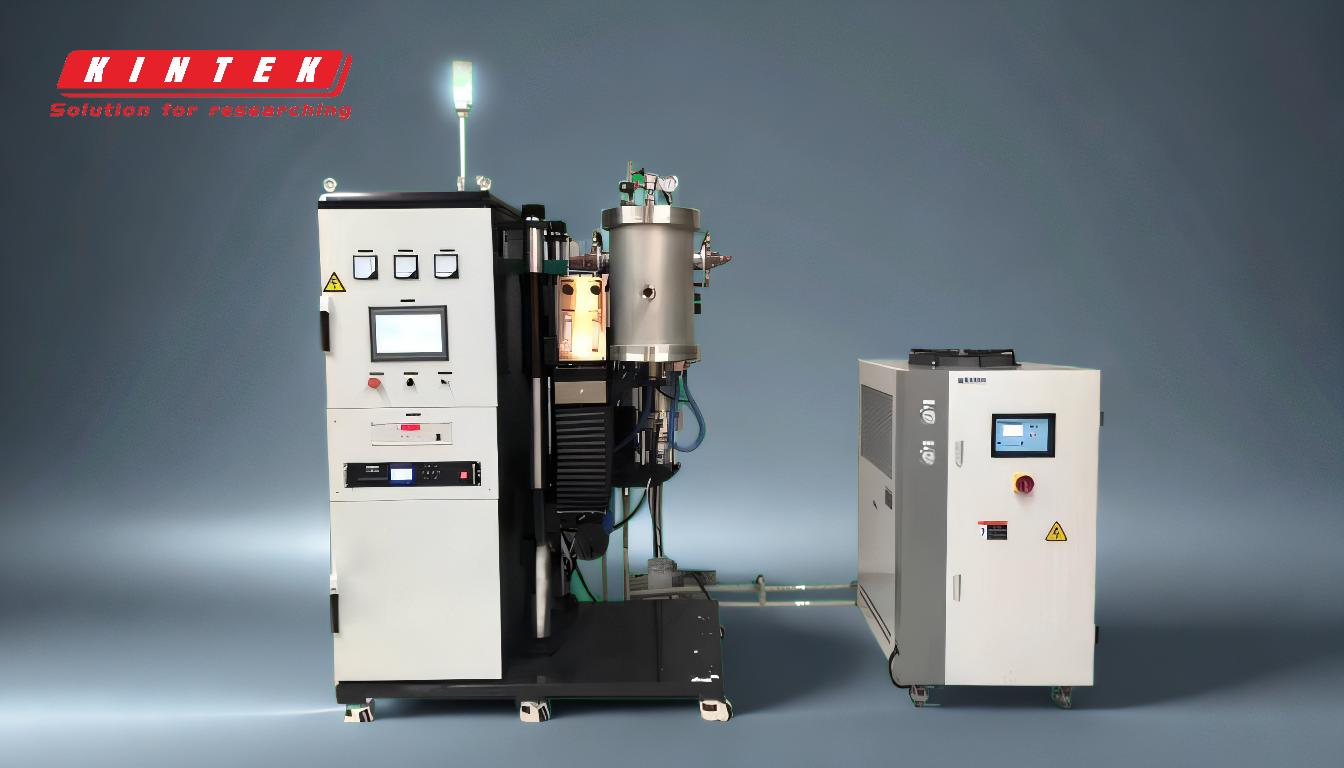
-
Definition and Purpose of a Sintering Furnace:
- A sintering furnace is designed to heat metal powders to temperatures below their melting point, allowing them to bond and form a solid, dense material.
- This process is crucial for producing high-strength, low-porosity metal components used in various industries.
-
Types of Sintering Furnaces:
- Hot Press Sintering Furnace: Combines high temperature and pressure in a vacuum environment to sinter materials, commonly used for ceramics and metals.
- Atmosphere Sintering Furnace: Controls the atmosphere (e.g., nitrogen, argon) to create an optimal sintering environment, preventing oxidation and contamination.
- Vacuum Sintering Furnace: Operates in a vacuum or hydrogen-protected state, ideal for sintering refractory metals like tungsten and molybdenum, as well as semiconductor components.
-
Key Components of a Sintering Furnace:
- Furnace Body: Houses the heating elements and the material to be sintered.
- Heater: Provides the necessary high temperatures for the sintering process.
- Pressure System: Applies pressure to compact the material, enhancing density and strength.
- Vacuum System: Creates a vacuum environment to prevent oxidation and contamination, crucial for high-quality sintering.
-
Sintering Process:
- Loading: Metal powder is placed inside the furnace.
- Vacuuming: The furnace is evacuated to remove air and create a vacuum.
- Heating: The material is heated to the required sintering temperature.
- Pressure Application: Pressure is applied to compact the material.
- Cooling: The sintered material is cooled slowly to prevent cracking and ensure structural integrity.
-
Applications of Sintering Furnaces:
- Automotive Industry: Production of gears, bearings, and other high-strength components.
- Aerospace Industry: Manufacturing of lightweight, durable parts.
- Electronics Industry: Sintering of semiconductor components and electrical contacts.
- Dental Industry: Processing of zirconia for dental restorations like crowns and bridges.
-
Advantages of Sintering:
- Cost-Effective: Sintering is less expensive than melting and casting processes.
- Efficient: The process is highly versatile and can be used for a wide range of materials.
- High-Quality Products: Produces dense, strong, and low-porosity materials with excellent mechanical properties.
-
Safety Considerations:
- Sintering furnaces operate at extremely high temperatures and use high amperage, making safety a paramount concern.
- Proper maintenance, regular inspections, and adherence to safety protocols are essential to prevent accidents and ensure long-term operation.
In summary, a sintering furnace for metal is a vital tool in modern manufacturing, enabling the production of high-quality, durable metal components through a controlled and efficient process. Its applications span multiple industries, and its design ensures safety and reliability in high-temperature operations.
Summary Table:
Aspect | Details |
---|---|
Definition | Heats metal powders below melting point to bond and form dense materials. |
Types | Hot Press, Atmosphere, Vacuum Sintering Furnaces. |
Key Components | Furnace body, heater, pressure system, vacuum system. |
Applications | Automotive, aerospace, electronics, dental industries. |
Advantages | Cost-effective, efficient, produces high-quality, durable materials. |
Safety Considerations | High temperatures and pressures require strict safety protocols. |
Ready to optimize your metal production process? Contact us today to learn more about sintering furnaces!