A sintering furnace is a specialized piece of equipment used in powder metallurgy to heat compacted metal powders to temperatures just below their melting points. This process, known as sintering, bonds the metal particles together, enhancing the mechanical strength, density, and structural integrity of the final product. Sintering furnaces are designed to achieve precise temperature control and uniform heating, which are critical for producing high-quality components from high-strength metals with high melting points. The sintering process transforms powdered metal into a solid, durable part, making it essential for manufacturing components in industries such as automotive, aerospace, and electronics.
Key Points Explained:
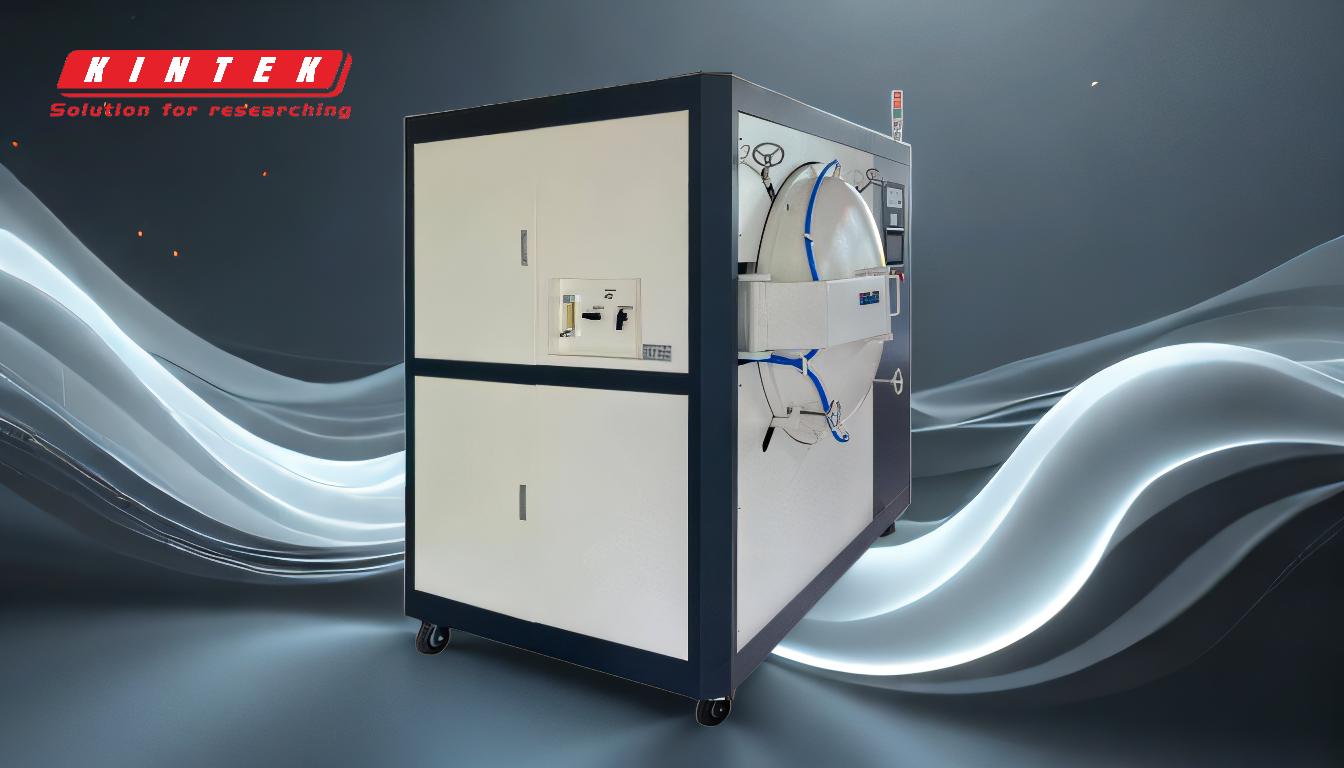
-
Definition of Sintering:
- Sintering is a heat treatment process used in powder metallurgy where powdered metal is compacted into a specific shape and then heated to bond the particles together without melting the material. This process enhances the mechanical properties of the final product, such as strength, density, and structural integrity.
-
Role of a Sintering Furnace:
- A sintering furnace is the equipment used to carry out the sintering process. It provides a controlled environment with precise temperature regulation and uniform heating, which are essential for achieving consistent and high-quality results. The furnace must reach refractory temperatures to bond high-strength metals effectively.
-
Temperature Control and Uniformity:
- Sintering furnaces are designed to maintain precise temperature control and heating uniformity. This is crucial because sintering occurs at temperatures just below the melting point of the metal powder. Accurate temperature management ensures that the particles bond properly without melting, which could compromise the structural integrity of the part.
-
Applications in Powder Metallurgy:
- Sintering is widely used in powder metallurgy to produce components with complex shapes and high strength. Industries such as automotive, aerospace, and electronics rely on sintering to manufacture parts like gears, bearings, and filters. The process allows for the production of near-net-shape components, reducing the need for additional machining.
-
Benefits of Sintering:
- The sintering process offers several advantages, including:
- Enhanced mechanical properties, such as increased strength and density.
- Improved structural integrity and stability of the final product.
- The ability to produce complex shapes with high precision.
- Cost-effectiveness due to reduced material waste and minimal post-processing requirements.
- The sintering process offers several advantages, including:
-
Types of Sintering Furnaces:
- There are various types of sintering furnaces, including batch furnaces, continuous furnaces, and vacuum furnaces. Each type is suited for specific applications and materials, depending on factors such as production volume, material properties, and desired outcomes.
By understanding the role and functionality of a sintering furnace, manufacturers can optimize the sintering process to produce high-quality, durable components for a wide range of industrial applications.
Summary Table:
Aspect | Details |
---|---|
Definition | A sintering furnace heats compacted metal powders to bond particles without melting. |
Key Features | Precise temperature control, uniform heating, and refractory temperatures. |
Applications | Automotive, aerospace, and electronics industries. |
Benefits | Enhanced strength, density, and cost-effectiveness. |
Types | Batch, continuous, and vacuum furnaces. |
Optimize your sintering process with our advanced furnaces—contact us today for expert guidance!